Types of laser welding include keyhole welding, conduction welding, and hybrid laser welding. Each type offers unique advantages for specific applications.
Laser welding is a versatile and precise welding technique used in various industries. It uses a laser beam to join multiple pieces of metal by melting their surfaces. Keyhole welding creates deep, narrow welds ideal for thick materials. Conduction welding is suitable for thin materials and provides high-quality, aesthetically pleasing welds.
Hybrid laser welding combines laser welding with another welding method, enhancing speed and weld quality. This advanced welding method is popular in automotive, aerospace, and electronics industries due to its efficiency and precision. Understanding the different types of laser welding helps in selecting the most suitable method for specific projects.
Introduction To Laser Welding
Laser welding is a modern technique that uses laser beams to join materials. It is known for its precision and efficiency. This method is popular in various industries, including automotive and aerospace.
What Is Laser Welding?
Laser welding is a process where a focused laser beam melts the materials. The melted materials then fuse together to form a strong joint. The laser provides a high-energy beam that can be controlled with precision.
This technique is ideal for joining metals and thermoplastics. It allows for deep welds with minimal distortion. The process can be automated, making it suitable for mass production.
Laser welding is different from traditional welding methods. It uses a concentrated light beam, rather than an electric arc or flame.
Brief History
Laser welding technology started in the 1960s. It was first developed for the aerospace industry. Early lasers were not very powerful, but they showed the potential for precise welding.
In the 1970s, advancements in laser technology made it more practical for industrial use. The automotive industry began adopting laser welding for manufacturing car bodies.
Today, laser welding is used in various sectors. It includes electronics, medical devices, and jewelry making. The technology continues to evolve, offering even more precise and efficient solutions.
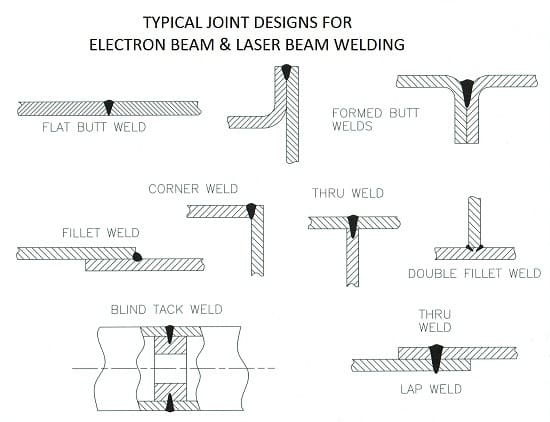
Credit: ebindustries.com
Benefits Of Laser Welding
Laser welding offers numerous benefits that make it a preferred method in various industries. From precision to speed, laser welding stands out as a highly efficient welding technique. Here are some key benefits of laser welding:
Precision And Accuracy
Laser welding provides high precision and accuracy, making it ideal for intricate designs. The focused laser beam allows for minimal distortion and exact welds. This ensures that even the smallest parts can be welded with high accuracy. Industries like aerospace and electronics favor laser welding for its precision.
Speed And Efficiency
Laser welding is known for its high speed and efficiency. The process can weld materials quickly, reducing production time. This results in higher throughput and lower costs. The ability to automate laser welding further enhances its efficiency. Companies can achieve consistent quality and faster production cycles.
Benefit | Description |
---|---|
Precision | Highly accurate welds for intricate designs |
Speed | Quick welding process reduces production time |
Efficiency | Automated process ensures consistent quality |
- Minimal distortion
- Exact welds
- High throughput
- Lower production costs
- Prepare the materials
- Set the laser parameters
- Start the welding process
Common Types Of Laser Welding
Laser welding is a versatile process used in various industries. It offers precision and efficiency. There are several types of laser welding. Here are the common types of laser welding you should know about.
Conduction Welding
Conduction welding is a popular type of laser welding. It uses a low power density laser. The laser heats the material’s surface. The heat then conducts into the material.
- Low power density laser
- Surface heating process
- Heat conducts into the material
This method is ideal for thin materials. It creates smooth and clean welds. Conduction welding is perfect for delicate tasks. It is often used in electronics and jewelry.
Keyhole Welding
Keyhole welding is another common type. It uses a high power density laser. The laser creates a small, deep hole in the material. This hole is called a keyhole.
- High power density laser
- Creates a small, deep hole
- Called a keyhole
Heat is absorbed around the keyhole. This causes the material to melt. The molten material fills the keyhole as it moves. This results in a strong, deep weld.
Keyhole welding is suitable for thick materials. It is used in automotive and aerospace industries. This method ensures high penetration and strength.
Type | Power Density | Application |
---|---|---|
Conduction Welding | Low | Thin materials, electronics, jewelry |
Keyhole Welding | High | Thick materials, automotive, aerospace |
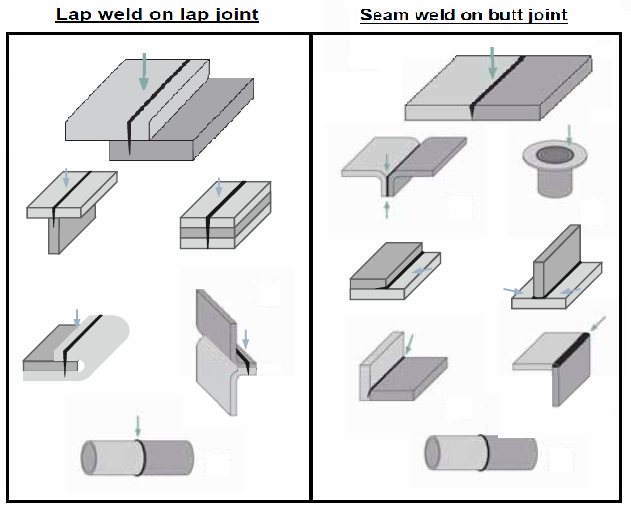
Credit: ahssinsights.org
Fiber Laser Welding
Fiber laser welding is a highly precise and efficient welding technique. It uses a fiber laser to join materials with minimal distortion. This method is known for its speed and accuracy, making it ideal for a variety of applications.
How It Works
Fiber laser welding works by focusing a high-intensity laser beam on the materials to be joined. The laser beam melts the material at the joint, creating a strong weld. The heat is concentrated in a small area, resulting in less thermal distortion.
The laser beam is delivered through an optical fiber, which provides flexibility and precision. This allows for welding in difficult-to-reach areas. The process can be automated, increasing efficiency and consistency.
Applications
Fiber laser welding is used in various industries due to its precision and efficiency. Below are some common applications:
- Automotive Industry: Used for welding components like gears and transmission parts.
- Electronics: Ideal for welding small, delicate components.
- Aerospace: Used for welding aircraft parts, ensuring strong and lightweight joints.
- Medical Devices: Ensures high precision in welding medical instruments and implants.
Fiber laser welding offers numerous advantages, such as speed and precision. Its versatility makes it suitable for a wide range of applications, enhancing productivity and product quality.
Co2 Laser Welding
CO2 laser welding uses a carbon dioxide laser to join materials. This method is highly efficient and widely used in various industries. Let’s explore the mechanism and advantages of CO2 laser welding.
Mechanism
CO2 laser welding operates using a gas mixture of carbon dioxide, nitrogen, and helium. The laser beam is generated when electricity excites the gas molecules. This beam is then focused onto the welding area using lenses or mirrors.
The intense heat from the laser melts the metal surfaces. This creates a strong bond as the materials cool and solidify. The welding process is precise, allowing for accurate and clean welds.
Advantages
Advantage | Description |
---|---|
High Precision | CO2 laser welding offers high precision and accuracy. |
Non-Contact Process | The laser beam does not physically touch the material. |
Versatility | Can weld various materials including metals and plastics. |
Speed | Fast welding process, reducing production time. |
Minimal Distortion | Reduces the risk of warping or distortion of materials. |
CO2 laser welding is a powerful and versatile technique. It provides high precision and speed. It is ideal for many industrial applications.
Nd:yag Laser Welding
Nd:YAG Laser Welding, also known as Neodymium-doped Yttrium Aluminum Garnet laser welding, is a versatile and popular welding technique. It utilizes a solid-state laser that offers high precision and control, making it ideal for a variety of industrial applications. This method is known for its ability to weld complex geometries and materials with minimal distortion.
Overview
Nd:YAG Laser Welding employs a crystal laser medium of Neodymium-doped Yttrium Aluminum Garnet. It operates at a wavelength of 1064 nm, making it suitable for welding reflective metals. The process provides deep penetration and can be used in both continuous and pulsed modes. This flexibility allows for precise control over heat input and weld characteristics.
Parameter | Details |
---|---|
Laser Type | Solid-state |
Wavelength | 1064 nm |
Operation Modes | Continuous and Pulsed |
Applications | Metals, Alloys, Reflective Materials |
Use Cases
Nd:YAG Laser Welding is used in various industries due to its precision and versatility. Below are some common applications:
- Automotive Industry: Used for welding engine components and body parts.
- Medical Devices: Ideal for manufacturing surgical instruments and implants.
- Electronics: Utilized in creating intricate circuits and connections.
- Aerospace: Employed in fabricating lightweight and durable components.
These use cases highlight the adaptability of Nd:YAG Laser Welding. It is a crucial technology in modern manufacturing processes.
Diode Laser Welding
Diode laser welding is a precise and efficient welding technique. It uses a focused beam of light to join materials. This method is popular for its high-speed and low-heat input. It is ideal for delicate and small parts.
Principles
Diode laser welding works by emitting light from diodes. These diodes are semiconductors that convert electricity into light. The light is then focused into a small spot. This spot generates intense heat, melting the materials to be joined. The molten materials cool down and solidify to form a strong bond.
The process involves several key components:
- Laser Diodes: Generate the laser light.
- Optics: Focus and direct the light beam.
- Workpiece: Materials to be welded.
- Controller: Manages the laser parameters.
The laser parameters include power, speed, and focus. Adjusting these parameters ensures optimal welding results.
Industry Uses
Diode laser welding is used in many industries. It is particularly useful for electronics and medical devices. The method is favored for its precision and control.
Industry | Applications |
---|---|
Electronics | PCB assembly, microelectronics |
Automotive | Battery connections, sensor welding |
Medical | Surgical instruments, implants |
Jewelry | Fine metalwork, repairs |
In the electronics industry, diode laser welding is used for joining tiny components. This includes PCB assembly and microelectronics. The automotive industry uses it for battery connections and sensor welding. In the medical field, it is ideal for making surgical instruments and implants. Jewelers use it for fine metalwork and repairs.
Diode laser welding offers many advantages. It provides high precision, low heat input, and fast processing times. These benefits make it a valuable tool in various industries.
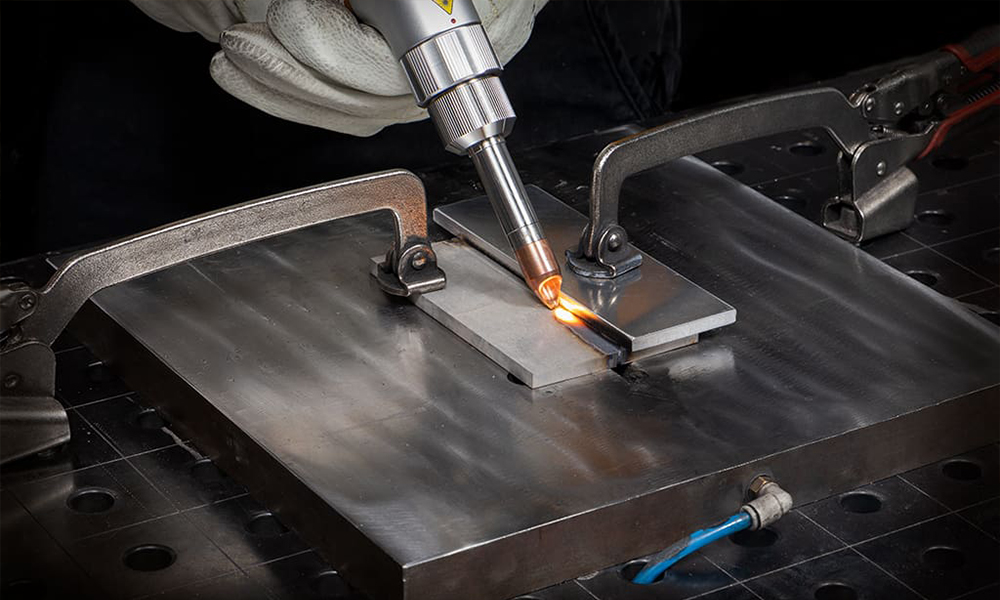
Credit: cobot.systems
Choosing The Best Technique
Laser welding is a precise and efficient method. It joins materials with high energy beams. Choosing the best technique is crucial for optimal results. This guide will help you select the right method.
Factors To Consider
- Material Type: Different materials react differently to lasers.
- Thickness: Material thickness impacts the welding process.
- Speed: Higher speeds can improve efficiency.
- Quality: Desired finish affects technique choice.
Comparative Analysis
Here is a comparative analysis of popular laser welding techniques:
Technique | Best For | Pros | Cons |
---|---|---|---|
Conduction Welding | Thin Materials | High Precision | Lower Depth |
Keyhole Welding | Thicker Materials | Deep Penetration | Complex Setup |
Hybrid Welding | Various Materials | Versatility | Higher Cost |
Future Of Laser Welding
The future of laser welding holds exciting possibilities. It’s evolving rapidly with new technologies and trends. This article explores the advancements and industry trends shaping its future.
Technological Advancements
Technological advancements are driving laser welding forward. New developments are making the process more efficient and precise.
- Fiber Lasers: Fiber lasers offer higher beam quality and energy efficiency.
- Automation: Automation in laser welding ensures consistent quality and faster production times.
- Real-Time Monitoring: Real-time monitoring systems help detect defects during the welding process.
- Advanced Cooling Systems: New cooling systems prevent overheating and improve machine lifespan.
Industry Trends
Industry trends indicate a growing adoption of laser welding in various sectors. These trends are shaping the future of this technology.
Industry | Trend |
---|---|
Automotive | Lightweight materials and electric vehicle production |
Aerospace | Precision welding for complex components |
Medical Devices | Microwelding for delicate parts |
Electronics | Miniaturization and high-volume production |
These trends highlight the versatility and growing importance of laser welding. Businesses are keen on leveraging these advancements and trends to stay competitive.
Frequently Asked Questions
What Is Laser Welding?
Laser welding is a technique that joins materials using concentrated laser beams. It provides high precision and speed.
How Does Laser Welding Work?
Laser welding works by focusing a laser beam to melt materials at the joint. This creates a strong bond.
What Are The Types Of Laser Welding?
There are several types: keyhole welding, conduction welding, and hybrid welding. Each has unique applications.
What Materials Can Be Laser Welded?
Laser welding can be used on metals, plastics, and composites. Common metals include steel, aluminum, and titanium.
Conclusion
Laser welding offers diverse techniques for various applications. Understanding each type ensures optimal results for your projects. Whether it’s keyhole, conduction, or hybrid welding, each method has unique benefits. Choose the right laser welding type to enhance efficiency and quality.
Stay informed and leverage these advanced techniques for superior outcomes.