Welding aluminum to aluminum requires specific techniques and equipment. Use the right filler materials and ensure proper preparation.
Welding aluminum can be challenging due to its unique properties. Aluminum has a high thermal conductivity and low melting point, making it susceptible to warping and cracking. Using the correct welding process, such as TIG or MIG, is essential for achieving strong welds.
Clean the aluminum thoroughly to remove any oxidation or contaminants. Selecting the appropriate filler material, typically 4043 or 5356 alloys, enhances weld quality. Employing proper techniques and equipment ensures successful aluminum-to-aluminum welding, resulting in durable and reliable joints. Practice and precision are crucial for mastering aluminum welding and achieving professional-grade results.
Introduction To Welding Aluminum
Welding aluminum is a unique and rewarding skill. This process requires precision and knowledge. Aluminum is a versatile and lightweight metal. It is used in many industries. Learning to weld aluminum can open many opportunities. Let’s dive into why aluminum is special and its common applications.
Why Aluminum?
Aluminum is a popular choice in welding for several reasons. First, it’s lightweight, making it easy to handle. Second, aluminum has excellent corrosion resistance. This makes it ideal for outdoor and marine applications. Third, it has a high strength-to-weight ratio. This means it can withstand heavy loads without being bulky.
- Lightweight – Easy to handle and transport.
- Corrosion resistance – Suitable for harsh environments.
- High strength-to-weight ratio – Strong yet not bulky.
Common Applications
Aluminum welding is used in various industries. Here are some common applications:
- Automotive Industry: Aluminum is used in car frames and parts. It helps to reduce vehicle weight and improve fuel efficiency.
- Aerospace Industry: Aircraft structures rely on aluminum. Its lightweight properties are crucial for flight.
- Construction: Aluminum is used in building frameworks and bridges. It provides strength without adding excessive weight.
- Marine Industry: Boats and ships utilize aluminum due to its resistance to seawater corrosion.
- Consumer Goods: Everyday items like bicycles and ladders often use aluminum.
Understanding these applications can help you appreciate the value of aluminum welding. This skill is both practical and in demand across many sectors.
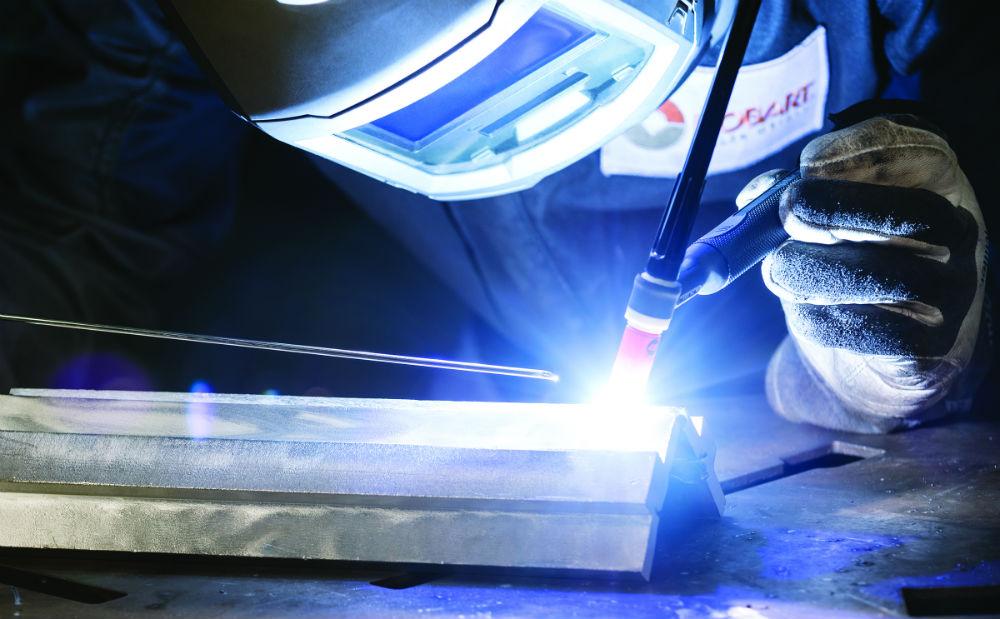
Credit: www.thefabricator.com
Types Of Aluminum Alloys
Welding aluminum to aluminum requires a good understanding of the different types of aluminum alloys. Aluminum alloys are categorized based on their primary alloying elements, which affect their properties and weldability. Knowing the different alloy series helps in selecting the right material for your welding project.
Series Classifications
Aluminum alloys are divided into series, which are identified by a four-digit number. Each series has unique characteristics:
Series | Main Alloying Element | Characteristics |
---|---|---|
1000 | Aluminum (99% or more) | High corrosion resistance, excellent thermal and electrical conductivity. |
2000 | Copper | High strength, good machinability, but lower corrosion resistance. |
3000 | Manganese | Good corrosion resistance, moderate strength, good workability. |
4000 | Silicon | Low melting point, good wear resistance, often used in welding wire. |
5000 | Magnesium | High strength, good corrosion resistance, excellent weldability. |
6000 | Magnesium and Silicon | Good mechanical properties, good corrosion resistance, very weldable. |
7000 | Zinc | Very high strength, moderate corrosion resistance, difficult to weld. |
8000 | Other elements | Specialized applications, properties vary widely. |
Choosing The Right Alloy
Choosing the right aluminum alloy is crucial for a successful welding project. Consider the following factors:
- Strength Requirements: Determine if high strength is necessary for your project.
- Corrosion Resistance: Choose an alloy with good corrosion resistance for outdoor use.
- Weldability: Select alloys that are known for their excellent weldability, like the 5000 and 6000 series.
- Thermal Conductivity: High thermal conductivity alloys are useful for heat exchangers.
- Application: Match the alloy to the specific application needs, such as marine or aerospace.
By understanding these classifications and factors, you can make an informed decision on the best alloy for your aluminum welding projects.
Preparation For Welding
Preparing aluminum for welding is crucial. It ensures strong and clean welds. Proper preparation involves cleaning, degreasing, and checking material thickness.
Cleaning And Degreasing
Cleaning aluminum surfaces is essential. It removes contaminants. Follow these steps:
- Use a wire brush or grinder to remove dirt.
- Apply a degreasing solution. This removes oils and grease.
- Rinse with clean water and dry thoroughly.
Degreasing prevents welding defects. It ensures a stable arc.
Material Thickness Considerations
Material thickness affects welding. Thicker materials need more heat. Thinner materials require less heat. Consider these points:
- Thinner aluminum can warp easily.
- Thicker aluminum needs higher amperage.
- Use proper welding techniques for different thicknesses.
Material Thickness | Recommended Amperage |
---|---|
1-2 mm | 30-50 amps |
3-4 mm | 50-70 amps |
5-6 mm | 70-90 amps |
Welding Techniques
Welding aluminum to aluminum requires specific techniques. The process can be challenging due to aluminum’s properties. Here, we discuss two popular methods: TIG Welding and MIG Welding.
Tig Welding
TIG Welding (Tungsten Inert Gas) offers high precision. It is perfect for thin aluminum sheets. The method uses a non-consumable tungsten electrode. This creates a clean and strong weld.
Key points about TIG Welding:
- Great for detailed work
- Produces high-quality welds
- Requires skilled operation
The process involves:
- Preparing the aluminum surface
- Setting the TIG welder parameters
- Using a filler rod for added strength
Mig Welding
MIG Welding (Metal Inert Gas) is faster than TIG. It is suitable for thicker aluminum pieces. The method uses a consumable wire electrode. This makes it easier for beginners.
Key points about MIG Welding:
- Faster process
- Ideal for thicker materials
- Less precision than TIG
The process involves:
- Cleaning the aluminum surface
- Setting the MIG welder parameters
- Using a spool gun for feeding wire
Welding Equipment
Welding aluminum requires specialized equipment. The right tools and safety gear make the process easier and safer. Let’s explore the essential tools and safety gear needed for welding aluminum.
Essential Tools
To weld aluminum, you need a few key tools. These tools help ensure strong and clean welds.
- TIG Welder: The best choice for welding aluminum. Provides precise control.
- MIG Welder: Suitable for thicker aluminum. Easier for beginners.
- Spool Gun: Useful for feeding aluminum wire. Reduces wire tangling.
- Wire Brush: Cleans the aluminum surface. Essential for removing oxidation.
- Clamps: Hold the pieces in place. Ensure stability during welding.
Safety Gear
Safety is crucial when welding aluminum. Wear the right safety gear to protect yourself.
Gear | Description |
---|---|
Welding Helmet | Protects your eyes and face from sparks and UV rays. |
Welding Gloves | Protects your hands from heat and burns. |
Fire-Resistant Jacket | Prevents burns from sparks and hot metal. |
Welding Apron | Shields your body from sparks and debris. |
Welding Boots | Protects your feet from falling objects and hot metal. |
Respirator | Filters out harmful fumes. Essential for your lung health. |
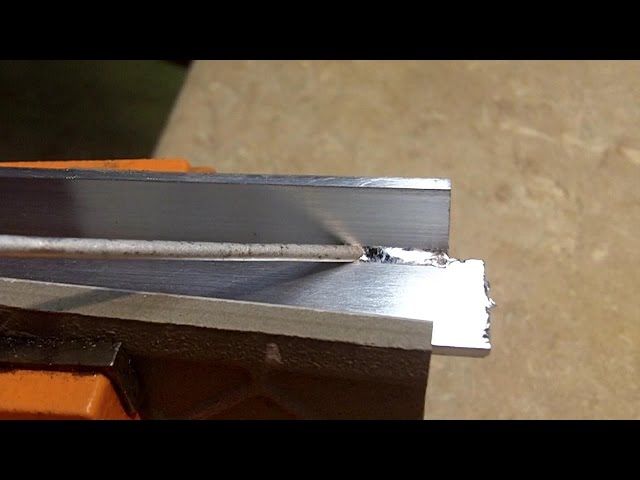
Credit: m.youtube.com
Common Challenges
Welding aluminum to aluminum can be tricky. This process often presents unique challenges. Understanding these issues is crucial for successful welds. In this section, we will explore two major problems: porosity and cracking.
Porosity Issues
Porosity in aluminum welding is a common issue. It occurs when gas gets trapped in the weld pool. This leads to weak welds and poor aesthetics.
Here are some causes and solutions:
- Contamination: Clean the aluminum surface thoroughly.
- Moisture: Store aluminum in a dry place.
- Improper shielding gas: Use pure argon gas.
- High welding speed: Slow down your welding speed.
Following these tips can minimize porosity issues in your welds.
Cracking Problems
Cracking is another major challenge in aluminum welding. It can occur during or after welding. Cracks weaken the weld and can cause failures.
Two main types of cracking are:
- Hot Cracking: Happens during solidification.
- Cold Cracking: Occurs after the weld has cooled.
Preventing cracks involves:
Type of Crack | Prevention Method |
---|---|
Hot Cracking | Use proper filler materials and control heat input. |
Cold Cracking | Preheat the material and ensure slow cooling. |
By following these methods, you can reduce the risk of cracks in your welds.
Post-welding Procedures
After welding aluminum to aluminum, the work is not done yet. Post-welding procedures are crucial to ensure the weld’s durability and strength. These steps help in identifying any potential issues that may compromise the weld. This section covers the essential post-welding procedures, focusing on inspection methods and heat treatment.
Inspection Methods
Inspection is vital to check the integrity of the weld. Various methods are available to inspect welded aluminum.
- Visual Inspection: This is the simplest method. Check for visible defects like cracks, porosity, or incomplete fusion.
- Ultrasonic Testing: High-frequency sound waves detect internal flaws. This method is effective for thicker materials.
- Radiographic Testing: X-rays or gamma rays create images of the weld. This reveals internal defects and ensures thorough inspection.
- Dye Penetrant Testing: Dye is applied to the weld. It reveals surface cracks when exposed to ultraviolet light.
Each method has its advantages. Choose the one that best fits your needs for accurate results.
Heat Treatment
Heat treatment is essential for restoring the material’s properties. Aluminum loses some of its strength during welding due to high temperatures. Different heat treatments help in restoring and enhancing these properties.
Heat Treatment | Purpose |
---|---|
Annealing | Reduces hardness and increases ductility. This makes the material easier to work with. |
Solution Heat Treatment | Involves heating to a high temperature. This dissolves alloying elements, followed by rapid cooling. |
Age Hardening | Improves the material’s strength and hardness. This is done by heating at lower temperatures over a longer period. |
Proper heat treatment enhances the welded aluminum’s performance. It ensures long-term durability and reliability.
Expert Tips For Success
Welding aluminum to aluminum requires skill and precision. These expert tips ensure a successful weld. Read on to learn vital techniques and methods.
Maintaining Consistent Speed
Maintaining a consistent speed is crucial. Uneven speed can cause weak joints.
- Use a steady hand.
- Practice with scrap pieces.
- Adjust your speed based on the material thickness.
Keep your movements smooth and controlled. This helps in creating uniform welds.
Avoiding Contamination
Contamination can ruin your welds. Clean the aluminum thoroughly before welding.
Step | Action |
---|---|
1 | Remove all dirt and grease. |
2 | Use a stainless steel brush. |
3 | Wipe with acetone. |
Ensure your workspace is free from contaminants. Keep tools and materials clean.

Credit: www.youtube.com
Frequently Asked Questions
What Is The Best Way To Weld Aluminum?
Using a TIG welder is the best way to weld aluminum. It provides precise control and clean welds. MIG welding is another good option for thicker aluminum.
Can You Weld Aluminum With A Stick Welder?
Welding aluminum with a stick welder is possible but challenging. It requires special aluminum electrodes. It is not the preferred method due to difficulty and lower quality results.
Do You Need Special Equipment To Weld Aluminum?
Yes, welding aluminum requires specific equipment. A TIG or MIG welder is essential. Additionally, an AC power source and proper shielding gas like argon are needed.
What Are Common Mistakes When Welding Aluminum?
Common mistakes include using incorrect settings, poor joint preparation, and inadequate cleaning. Proper cleaning and preparation are crucial for successful aluminum welding.
Conclusion
Mastering aluminum welding requires skill and the right techniques. Practice and patience ensure strong, durable welds. Always prioritize safety and use quality equipment. By following these tips, you’ll achieve professional results. Happy welding!