Are you having trouble with a leaky aluminum radiator? Soldering an aluminum radiator is a cost-effective and straightforward solution that can save you the hassle and expense of replacing the entire unit. In this article, we will guide you step-by-step on how to solder an aluminum radiator effectively.
Soldering an aluminum radiator may seem daunting at first, but with the right tools and techniques, it can be a simple DIY project. Whether you have a pinhole leak or a crack in your radiator, soldering can provide a reliable and long-lasting fix.
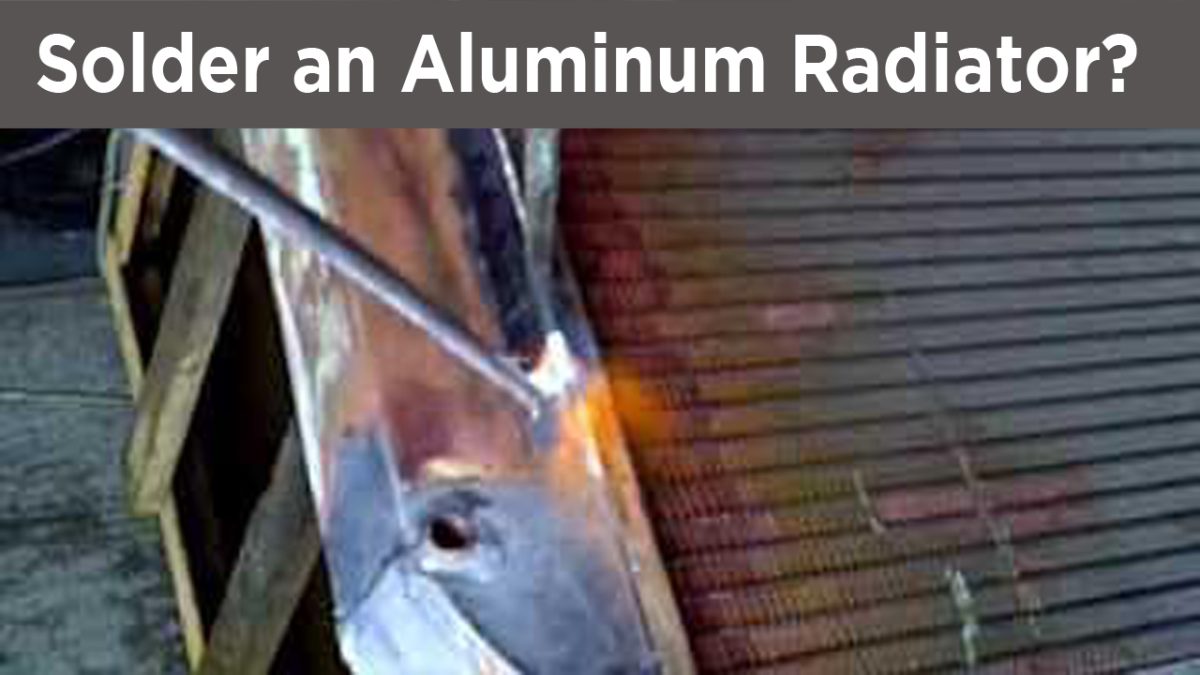
Photo by carsconversation4778
Tools and materials needed for soldering
To begin soldering your aluminum radiator, you’ll need a few essential tools and materials. Here’s a list of what you’ll need:
Aluminum soldering flux: This special flux is designed to work specifically with aluminum, helping the solder adhere properly.
Aluminum solder wire: Opt for a high-quality aluminum solder wire with a low melting point for better results.
Soldering iron: Choose a soldering iron with adjustable temperature settings to ensure precise control.
Sandpaper or emery cloth: Use fine-grit sandpaper or emery cloth to clean the radiator’s surface before soldering.
Cleaning solution: A mild cleaning solution or rubbing alcohol can be used to remove any grease or dirt from the radiator.
Safety gear: Don’t forget to wear safety goggles and heat-resistant gloves to protect yourself during the soldering process.
Once you have gathered all the necessary tools and materials, you’re ready to prepare your aluminum radiator for soldering.
Preparing the aluminum radiator for soldering
Before you begin soldering, it’s crucial to properly prepare the aluminum radiator to ensure a strong bond. Follow these steps:
- Turn off the radiator: Make sure the radiator is completely cool before starting the soldering process.
- Clean the surface: Use sandpaper or emery cloth to clean the area around the leak or crack. Remove any rust, paint, or debris that may hinder the solder from adhering properly.
- Apply the flux: Apply a small amount of aluminum soldering flux to the cleaned surface. Spread it evenly, ensuring it covers the entire area you will be soldering.
- Heat the radiator: Use a heat gun or propane torch to heat the area surrounding the leak or crack. This will help the flux activate and prepare the surface for soldering.
Now that your radiator is prepped and ready, it’s time to choose the right soldering technique for aluminum.
Choosing the right soldering technique for aluminum
When it comes to soldering aluminum, there are two common techniques you can use: torch soldering and soldering iron soldering. Each technique has its advantages and is suitable for different situations.
Torch soldering is ideal for larger cracks or leaks. It involves using a propane torch to heat the aluminum and melting the solder onto the surface. Torch soldering provides a quick and efficient way to repair your radiator.
On the other hand, soldering iron soldering is more suitable for smaller leaks or delicate areas. It requires a soldering iron with a pointed tip to apply the solder directly onto the radiator. This technique allows for more precise control and is less likely to damage surrounding components.
Choose the technique that best suits your needs and comfort level. Let’s dive into the step-by-step guide to soldering an aluminum radiator.
Step-by-step guide to soldering an aluminum radiator
Position the solder
Begin by positioning the solder wire near the leak or crack on the radiator. Make sure it’s in a convenient place for easy access during the soldering process.
Heat the radiator
Using your chosen soldering technique (torch or soldering iron), apply heat to the area surrounding the leak or crack. Heat the aluminum until it reaches the melting point of the solder.
Apply the solder
Once the aluminum is heated, touch the solder wire to the heated area. The solder should melt and flow smoothly onto the radiator’s surface. Move the solder along the entire length of the leak or crack, ensuring it covers the entire damaged area.
Smooth the solder
Use a soldering iron or a soldering iron stand with a built-in scraper to smooth out the solder and create an even surface. Be careful not to apply too much pressure, as this may damage the radiator.
Inspect and clean
After soldering, inspect the soldered area for any imperfections or gaps. If necessary, reheat the solder and make any necessary adjustments. Once you’re satisfied with the soldering job, clean the radiator with a mild cleaning solution to remove any flux residue.
Tips for successful soldering
While soldering an aluminum radiator is a relatively straightforward process, there are a few tips that can help ensure a successful outcome:
Practice on scrap aluminum
If you’re new to soldering or unsure about your technique, it’s a good idea to practice on scrap aluminum before working on your radiator. This will help you get a feel for the soldering process and build confidence.
Use the right soldering iron tip
When soldering small or delicate areas, choose a soldering iron with a fine, pointed tip. This will allow for more precise control and minimize the risk of damaging surrounding components.
Be patient
Take your time during the soldering process. Rushing can lead to mistakes or a poor solder joint. Remember, precision and attention to detail are key to a successful soldering job.
Keep the soldering iron clean
Regularly clean the soldering iron tip using a damp sponge or brass wire cleaner. A clean tip ensures better heat transfer and improves the soldering process.
Practice proper safety precautions
Wear safety goggles and heat-resistant gloves to protect yourself from potential hazards during soldering. Work in a well-ventilated area to avoid inhaling toxic fumes.
Common mistakes to avoid when soldering aluminum radiators
While soldering an aluminum radiator is relatively simple, there are a few common mistakes to avoid:
Overheating
Excessive heat can damage the radiator or surrounding components. Be mindful of the temperature and avoid overheating the aluminum.
Insufficient cleaning
Failing to properly clean the surface before soldering can result in a weak bond. Make sure to remove all rust, paint, and debris from the radiator.
Using the wrong solder
Select a solder specifically designed for aluminum. Using the wrong type can lead to poor adhesion and an unreliable fix.
Not applying enough flux
Flux is essential for proper adhesion. Be sure to apply enough flux to cover the entire area you’ll be soldering.
Not practicing proper safety precautions
Always wear safety goggles and heat-resistant gloves when soldering. Failing to do so can result in serious injury.
Safety precautions when soldering aluminum radiators
Soldering aluminum radiators involves working with high temperatures and potentially toxic fumes. To ensure your safety, follow these precautions:
Work in a well-ventilated area: Adequate ventilation is crucial to prevent the buildup of toxic fumes. If possible, work near an open window or use a ventilation fan to keep the air circulating.
Wear safety goggles: Protect your eyes from flying debris or splattering solder by wearing safety goggles throughout the soldering process.
Use heat-resistant gloves: Aluminum radiators can become extremely hot during the soldering process. Wear heat-resistant gloves to protect your hands from burns or injuries.
Handle the soldering iron with care: The soldering iron can reach high temperatures. Avoid touching the tip or placing it on flammable surfaces to prevent accidents.
Keep a fire extinguisher nearby: In case of a fire, have a fire extinguisher readily available to quickly extinguish any flames.
Troubleshooting soldering issues
Even with proper preparation and technique, soldering issues can still arise. Here are a few common problems and their potential solutions:
Solder not adhering
If the solder doesn’t adhere to the radiator, double-check that the surface is clean and free of debris. Ensure that you’re using the correct solder and that the radiator is properly heated.
Solder joint cracking
A cracked solder joint may indicate insufficient heat or a weak bond. Reheat the soldered area and add additional solder if necessary.
Excessive soldering
Too much solder can create a messy joint or lead to poor heat dissipation. Use the appropriate amount of solder to ensure a clean and functional repair.
Uneven solder surface
If the solder surface is uneven or lumpy, use a soldering iron or scraper to smooth it out while the solder is still hot. Be careful not to damage the radiator in the process.
Conclusion and final thoughts
Soldering an aluminum radiator is an effective and budget-friendly solution for repairing leaks or cracks. By following the step-by-step guide and tips provided in this article, you can confidently tackle any radiator soldering project.
Remember to gather all the necessary tools and materials, prepare the radiator properly, and choose the appropriate soldering technique for your specific needs. Take your time during the soldering process, practice proper safety precautions, and troubleshoot any issues that may arise.
With the knowledge and skills gained from this article, you’ll be able to extend the lifespan of your aluminum radiator and save money on costly replacements. So grab your tools, put on your safety gear, and get ready to solder your way to a leak-free radiator!