Are you interested in learning more about X-Ray non-destructive testing (NDT)? In this article, we will explore the advantages and disadvantages of this widely used technology. X-Ray NDT is a non-invasive testing method that uses X-Rays to evaluate the integrity and quality of materials and structures without causing any damage. This technique is commonly used in various industries, such as aerospace, automotive, and manufacturing, to detect defects, flaws, or cracks that may not be visible to the naked eye.
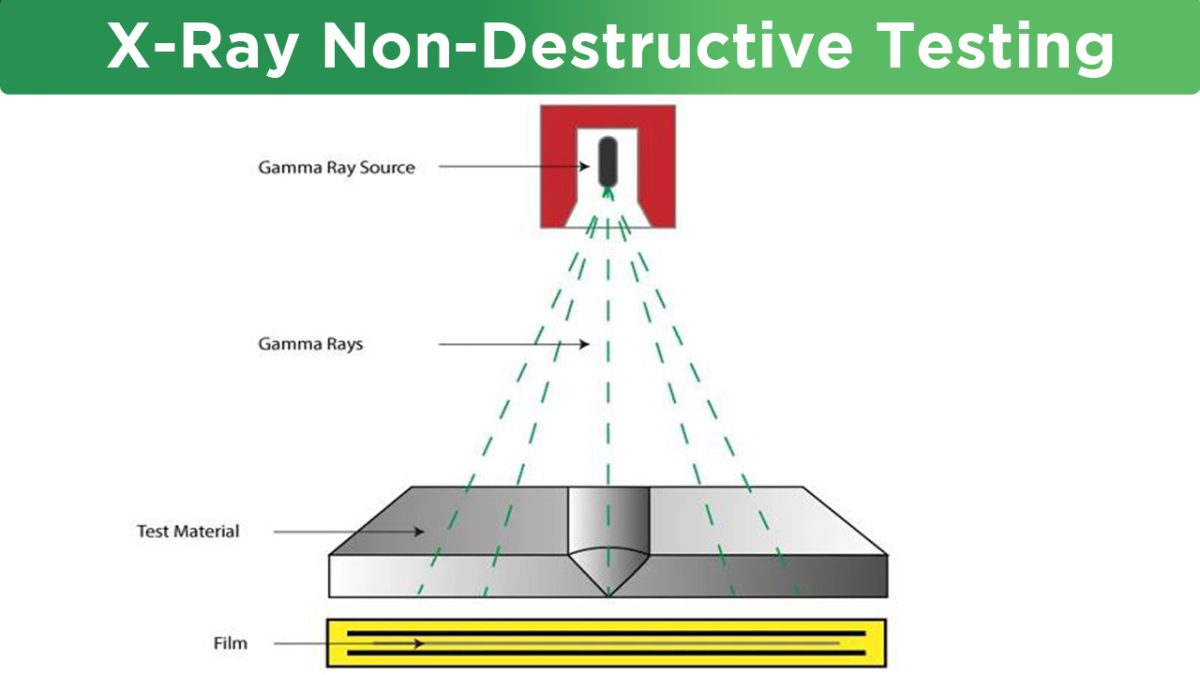
What is X-ray non-destructive testing (NDT)?
X-Ray non-destructive testing (NDT) is a technique used to evaluate the internal structure and integrity of materials and structures without causing any damage. It involves the use of X-Rays to penetrate the object being tested and produce images that can reveal defects, flaws, or cracks that may not be visible to the naked eye. This technique is widely used in industries such as aerospace, automotive, and manufacturing, where the quality and reliability of materials and structures are of utmost importance.
Advantages of X-ray NDT
X-Ray non-destructive testing offers several advantages over other testing methods. One of the major advantages is its ability to provide detailed and accurate insights into the internal structure of an object. X-Rays can penetrate through the material and produce high-resolution images that can reveal even the smallest defects or cracks. This enables engineers and technicians to assess the condition of the object and make informed decisions regarding its usability or the need for repairs.
Another advantage of X-Ray NDT is its efficiency. This technique is relatively quick and efficient, allowing for rapid inspection and evaluation. Unlike destructive testing methods that require samples to be taken and analyzed, X-Ray NDT can be performed on the object as a whole, saving time and reducing costs. This makes it an attractive option for industries where time is of the essence, such as aerospace and manufacturing.
X-Ray NDT is a non-invasive testing method, meaning it does not cause any damage to the object being tested. This is particularly important when testing delicate or expensive materials, as it eliminates the need for destructive testing that could render the object unusable. It also allows for repeated testing without compromising the integrity of the material or structure.
Disadvantages of X-ray NDT
While X-Ray NDT offers several advantages, it does have some disadvantages that need to be considered. One of the main disadvantages is the use of ionizing radiation. X-Rays are a form of ionizing radiation, which can be harmful to human health if proper safety precautions are not followed. It is crucial to implement safety measures, such as shielding and appropriate distance from the X-Ray source, to protect technicians and others in the vicinity from unnecessary exposure.
Another disadvantage is the cost associated with X-Ray NDT equipment and training. The equipment required for X-Ray testing can be expensive, especially for high-resolution imaging systems. Additionally, specialized training is necessary to operate the equipment effectively and interpret the X-Ray images accurately. This can add to the overall cost and may require additional resources for training and certification of technicians.
Applications of X-ray NDT
X-Ray NDT has a wide range of applications across various industries. In the aerospace industry, it is used to inspect aircraft components, such as turbine blades, engine parts, and structural elements, for defects or cracks that could compromise safety and performance. In the automotive industry, X-Ray NDT is used to inspect welds, castings, and other critical components to ensure quality and reliability. In the manufacturing industry, it is used to inspect welds, detect internal defects in metal or plastic components, and ensure the integrity of structures.
How does X-ray NDT work?
X-Ray NDT works by emitting X-Rays from a source towards the object being tested. The X-Rays pass through the material and interact differently with different types of materials and defects. The X-Rays that pass through the material are detected by a sensor, which converts the X-Rays into electrical signals. These signals are then processed to create images that reveal the internal structure and any defects or cracks present. The images can be analyzed by technicians or engineers to assess the condition of the object and determine if further action is required.
X-ray NDT equipment and techniques
X-Ray NDT requires specialized equipment to generate and detect X-Rays. The equipment typically consists of an X-Ray source, a detector, and a control unit. The X-Ray source emits a beam of X-Rays, which is directed towards the object being tested. The detector captures the X-Rays that pass through the object and converts them into electrical signals. The control unit processes the signals and creates images that can be analyzed.
Different techniques can be used in X-Ray NDT, depending on the requirements of the application. These techniques include film radiography, computed radiography, and digital radiography. Film radiography involves exposing a photographic film to X-Rays, which produces a black and white image that can be analyzed. Computed radiography uses a phosphor plate to capture X-Rays, which is then scanned and converted into a digital image. Digital radiography directly captures X-Rays using a digital detector, producing immediate digital images that can be analyzed.
Safety considerations in X-ray NDT
Safety is of utmost importance when performing X-Ray NDT. As mentioned earlier, X-Rays are a form of ionizing radiation, which can be harmful to human health. To ensure safety, proper shielding should be in place to minimize unnecessary exposure to X-Rays. Technicians and others in the vicinity should also follow appropriate distance guidelines to reduce their exposure. It is essential to implement safety protocols and provide proper training to technicians to minimize the risks associated with ionizing radiation.
X-ray NDT in different industries
X-Ray NDT finds applications in various industries where the integrity and quality of materials and structures are crucial. In the aerospace industry, it is used to inspect aircraft components, such as turbine blades, engine parts, and structural elements, for defects or cracks that could compromise safety and performance. In the automotive industry, X-Ray NDT is used to inspect welds, castings, and other critical components to ensure quality and reliability. In the manufacturing industry, it is used to inspect welds, detect internal defects in metal or plastic components, and ensure the integrity of structures.
Conclusion
X-Ray non-destructive testing (NDT) offers valuable insights into the integrity and quality of materials and structures without causing any damage. It provides detailed and accurate information about the internal structure and can reveal defects or cracks that may not be visible to the naked eye. It is essential to consider the advantages and disadvantages of X-Ray NDT before implementing this technique.
Safety precautions should be followed to minimize the risks associated with ionizing radiation, and the cost of equipment and training should be taken into account. X-Ray NDT is a powerful tool that can greatly benefit various industries, but careful consideration is necessary to ensure its effective and safe implementation.