If you’re a stick welding enthusiast, you know that even the most skilled welders encounter problems from time to time. Whether you’re experiencing issues with your electrode sticking, poor bead quality, or difficulty striking an arc, stick welding problems can be frustrating and time-consuming. But fear not! In this article, we will explore common stick welding problems and provide you with practical solutions to overcome them.
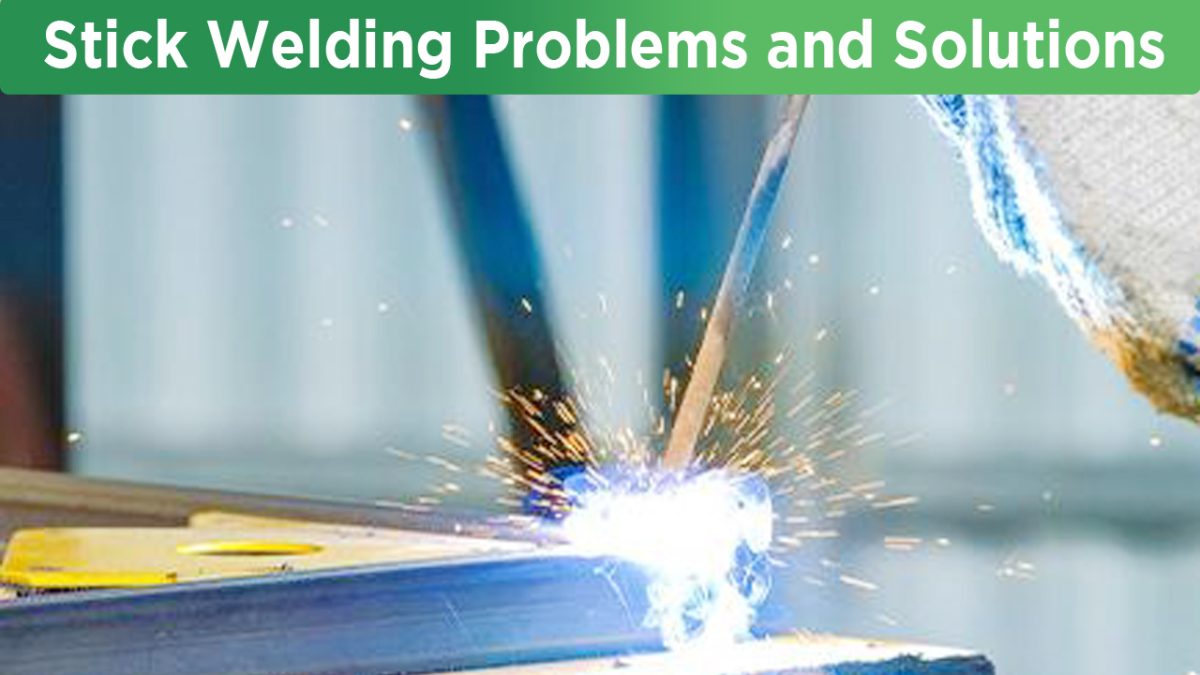
image by blog.red-d-arc
Common stick welding problems
Lack of penetration
One of the most common issues faced by stick welders is a lack of penetration. This occurs when the weld does not penetrate deep enough into the base metal, resulting in weak and unreliable joints. There are several factors that can contribute to this problem, including incorrect amperage settings, inadequate cleaning of the base metal, or improper electrode angle.
To ensure proper penetration, it is crucial to select the correct amperage for the thickness of the metal being welded. Too low of an amperage can result in insufficient heat, while too high of an amperage can cause excessive heat and burn through the metal. Additionally, thoroughly cleaning the base metal before welding is essential to remove any dirt, rust, or paint that may interfere with the welding process. Finally, maintaining the correct electrode angle is crucial for achieving proper penetration. A slight drag angle, where the electrode is tilted slightly backward, can help ensure deep and consistent penetration.
Excessive spatter
Another common problem faced by stick welders is excessive spatter. Spatter refers to the small droplets of molten metal that can splatter onto the surrounding area during welding. Excessive spatter not only creates a messy work environment but can also interfere with the quality of the weld.
To minimize spatter, it is important to ensure that the electrode is clean and free from any contaminants. Using the correct amperage and maintaining the correct electrode angle can help reduce spatter. Welding at too high of an amperage or with an incorrect electrode angle can cause excessive spatter. It is also helpful to use anti-spatter spray or gel on the base metal before welding. These products create a barrier between the metal and the spatter, making it easier to remove after welding.
Porosity in welds
Porosity refers to the presence of small gas pockets or voids within the weld. These pockets weaken the weld and can lead to structural failures. Porosity is often caused by inadequate shielding gas coverage, contaminated electrodes, or improper welding techniques.
To prevent porosity, it is essential to ensure proper shielding gas coverage during welding. Shielding gas protects the weld from atmospheric contamination, and inadequate coverage can result in porosity. Additionally, using clean and dry electrodes is crucial to avoid introducing contaminants into the weld. Storing electrodes in a moisture-resistant container and properly drying them before use can help prevent porosity. Finally, using the proper welding technique, such as maintaining a consistent travel speed and avoiding excessive weaving, can minimize the risk of porosity.
Uneven bead appearance
Achieving a smooth and uniform bead appearance is essential for producing high-quality welds. However, many welders struggle with achieving an even bead appearance, which can be attributed to various factors.
One common cause of uneven bead appearance is an inconsistent travel speed. Welding too slowly can result in a wider and flatter bead, while welding too quickly can lead to a narrower and higher bead. Maintaining a steady and consistent travel speed throughout the weld can help achieve an even bead appearance.
Another factor that can affect bead appearance is electrode manipulation. The angle and direction in which the electrode is moved during welding can impact the shape and appearance of the bead. Experimenting with different techniques, such as pushing or pulling the electrode, and practicing precise manipulation can help achieve the desired bead appearance.
Electrode sticking and difficult arc striking
Electrode sticking occurs when the electrode fuses to the base metal, preventing smooth and consistent welding. Difficulty in striking an arc, on the other hand, refers to the challenges faced when starting the welding process. Both of these issues can be frustrating and hinder the welding progress.
To prevent electrode sticking, it is important to maintain the correct arc length. The arc length refers to the distance between the electrode and the base metal. A short arc length can cause the electrode to stick, while a long arc length can result in an unstable arc. Finding the optimal arc length, typically around 1/8 to 3/16 inch, can help prevent electrode sticking.
Difficulty in striking an arc can be caused by several factors, including incorrect amperage settings, improper electrode angle, or insufficient cleaning of the base metal. Ensuring the correct amperage, maintaining the proper electrode angle, and thoroughly cleaning the base metal can help overcome this challenge.
Solutions to stick welding problems
Now that we have explored common stick welding problems, let’s discuss some practical solutions to overcome these challenges.
Stick welding troubleshooting tips
- Always ensure that you have selected the correct amperage for the thickness of the metal being welded. Adjust the amperage as needed to achieve the desired penetration and bead appearance.
- Thoroughly clean the base metal before welding to remove any dirt, rust, or paint that may interfere with the welding process. Use a wire brush or grinder to clean the metal surface.
- Practice maintaining the correct electrode angle. Experiment with different angles to find the one that works best for your welding technique.
- Use anti-spatter spray or gel on the base metal to minimize spatter. Apply a thin and even coat before welding.
- Store electrodes in a moisture-resistant container and dry them properly before use to avoid introducing contaminants into the weld.
- Maintain a steady and consistent travel speed throughout the weld to achieve an even bead appearance.
- Experiment with different electrode manipulation techniques to achieve the desired bead appearance. Practice precise manipulation to improve your skills.
- Ensure the correct arc length to prevent electrode sticking. Aim for an arc length of around 1/8 to 3/16 inch.
- Double-check the amperage settings, maintain the proper electrode angle, and thoroughly clean the base metal to facilitate easier arc striking.
Final Thoughts
Stick welding problems can be frustrating, but with the right techniques and troubleshooting tips, you can overcome these challenges and become a more confident and skilled stick welder. Remember to select the correct amperage, maintain the proper electrode angle, and thoroughly clean the base metal for optimal results. By following these steps and practicing your welding skills, you’ll be able to produce clean, high-quality welds every time.
So, don’t let stick welding problems hold you back – tackle them head-on and enjoy the satisfaction of mastering this versatile welding technique.