In the field of engineering and material science, testing plays a crucial role in ensuring the safety, reliability, and performance of various products and structures. Two primary methods employed for testing are destructive testing (DT) and nondestructive testing (NDT). Both methods serve distinct purposes and have their own advantages and limitations. In this article, we will delve into the world of destructive and nondestructive testing, exploring their definitions, applications, benefits, and differences.
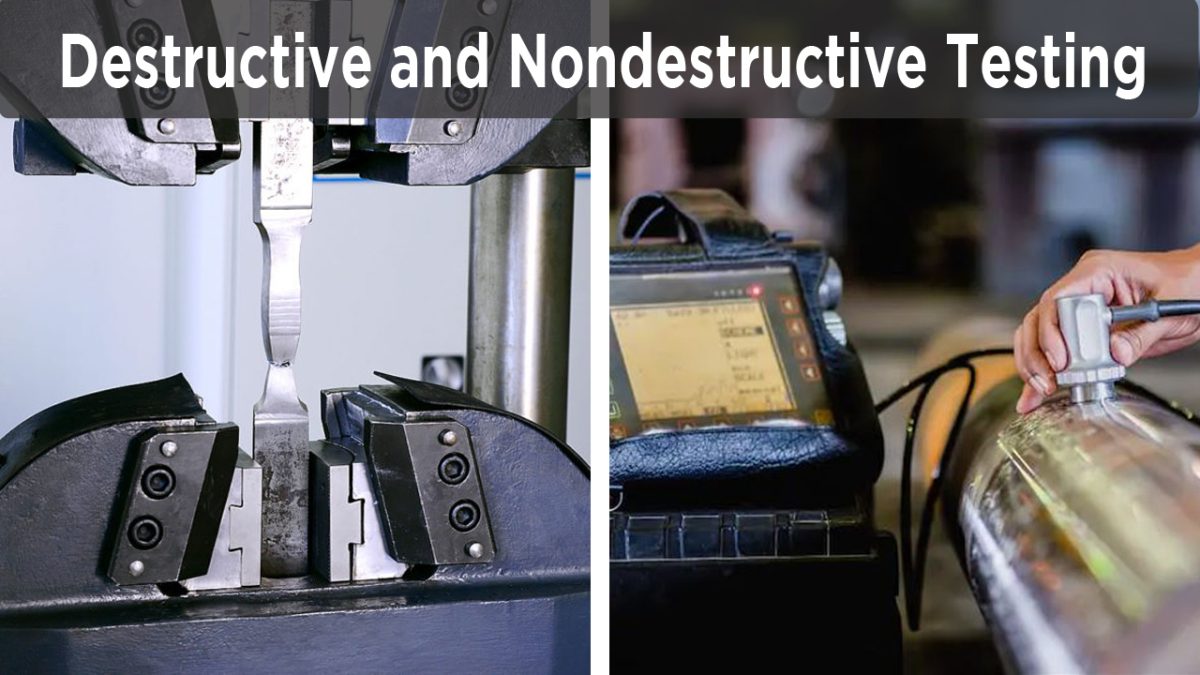
Image by fractory & werkstofftechnik
What is Destructive Testing?
Destructive testing involves subjecting a sample or component to a controlled level of stress or loading until it fails. The primary objective of destructive testing is to determine the mechanical properties, strength, and durability of the material or component being tested. By intentionally causing failure, engineers can gather valuable data about the material’s behavior and performance under extreme conditions.
Applications and Benefits of Destructive Testing
Destructive testing finds applications in various industries, including aerospace, automotive, construction, and manufacturing. It is commonly used to evaluate the quality and integrity of materials, components, and structures. By subjecting materials to extreme conditions, engineers can assess their suitability for specific applications, identify weaknesses, and improve designs.
The benefits of destructive testing are numerous. It allows engineers to obtain precise measurements of mechanical properties, such as tensile strength, hardness, and fracture toughness. It also provides valuable insights into failure modes, enabling engineers to enhance product safety and reliability. Additionally, destructive testing can assist in the development of new materials and in the validation of computer simulations.
Common Destructive Testing Methods
Several destructive testing methods are commonly employed in different industries. Tensile testing, for example, involves pulling apart a specimen until it fractures, revealing its ultimate tensile strength and elongation properties. Another method, hardness testing, determines the resistance of a material to indentation or scratching. Other common destructive testing methods include impact testing, fatigue testing, and bending testing.
Limitations and Considerations of Destructive Testing
While destructive testing provides invaluable insights, it also has limitations and considerations that need to be taken into account. The primary limitation is the destruction of the tested specimen. Once the test is completed, the sample can no longer be used. This can be costly, especially when testing expensive or rare materials. Additionally, destructive testing can be time-consuming, requiring the preparation of multiple samples and the execution of rigorous testing protocols.
Another consideration is the representativeness of the tested sample. In some cases, the sample might not accurately represent the entire material or component being tested. Variations in manufacturing processes, material properties, or structural features can influence the test results. Careful sample selection and testing protocols are vital to ensure reliable and accurate data.
What is Nondestructive Testing?
Nondestructive testing, as the name suggests, involves evaluating the properties and integrity of a material or structure without causing any permanent damage. NDT techniques rely on various physical principles, such as sound waves, electromagnetic radiation, and thermal properties, to inspect and assess the quality of the material or component.
Applications and Benefits of Nondestructive Testing
Nondestructive testing is widely used across industries where the integrity of materials and structures is of utmost importance. It is extensively employed in aerospace, oil and gas, power generation, and manufacturing sectors. NDT allows engineers to detect flaws, defects, and irregularities that may compromise the structural integrity or performance of the tested object.
The benefits of nondestructive testing are substantial. It provides a non-intrusive and non-disruptive method to inspect materials, components, and structures, minimizing downtime and avoiding unnecessary damage. NDT techniques can detect hidden defects that might not be visible to the naked eye, allowing for timely repairs and maintenance. Moreover, NDT helps in ensuring compliance with safety standards and regulations, enhancing the overall quality and reliability of products.
Common Nondestructive Testing Methods
Various nondestructive testing methods are employed depending on the type of material, the nature of defects, and the desired level of sensitivity. Ultrasonic testing, for instance, uses high-frequency sound waves to detect internal flaws or changes in material thickness. Another widely used method is radiographic testing, which utilizes X-rays or gamma rays to create images of the internal structure of an object. Other common NDT methods include magnetic particle testing, liquid penetrant testing, and eddy current testing.
What is the Difference Between Destructive and Nondestructive Testing?
The key difference between destructive and nondestructive testing lies in the objective and outcome of the test. Destructive testing intentionally causes failure to gather data about the material or component being tested. It provides precise measurements of mechanical properties but destroys the tested sample in the process. Nondestructive testing, on the other hand, aims to assess the quality and integrity of the material or component without causing any damage. It allows for the detection of flaws and defects while preserving the usability of the tested object.
Choosing the Right Testing Method for Your Needs
The choice between destructive and nondestructive testing depends on various factors, including the purpose of the test, the availability of samples, the cost implications, and the desired level of accuracy. Destructive testing is suitable when precise measurements of mechanical properties are required, and the availability of samples is not a constraint. Nondestructive testing, on the other hand, is preferable when the integrity of the tested object needs to be assessed without causing any damage.
Industries That Rely on Destructive and Nondestructive Testing
Destructive and nondestructive testing find applications in a wide range of industries. In aerospace, both methods are crucial for ensuring the structural integrity and performance of aircraft components. The automotive industry relies on destructive and nondestructive testing to evaluate the quality and reliability of vehicle parts. Construction companies utilize these testing methods to ensure the safety and durability of buildings and infrastructure. Additionally, manufacturing industries employ destructive and nondestructive testing to assess the quality of materials and components throughout the production process.
Final Thoughts
Destructive and nondestructive testing are indispensable tools in the field of engineering and material science. While destructive testing provides precise measurements of mechanical properties through intentional failure, nondestructive testing allows for the assessment of material integrity without causing any damage. Both methods have their unique applications, benefits, and limitations. The choice between destructive and nondestructive testing depends on the specific requirements of the testing scenario and the desired outcomes.
By understanding these testing methods and their differences, engineers can make informed decisions to ensure the safety, reliability, and performance of products and structures.