Plasma welding is an advanced welding technique that utilizes a high-temperature plasma gas to create precise and efficient welds. Unlike traditional welding methods, plasma welding offers numerous advantages, making it a preferred choice in industries such as automotive, aerospace, and manufacturing.
The process of plasma welding starts with the generation of an electric arc between a tungsten electrode and the workpiece. This arc ionizes and heats the gas flowing through the plasma torch, creating a high-temperature plasma gas that reaches temperatures up to 30,000 degrees Fahrenheit. This intense heat allows for the precise and controlled welding of various materials.
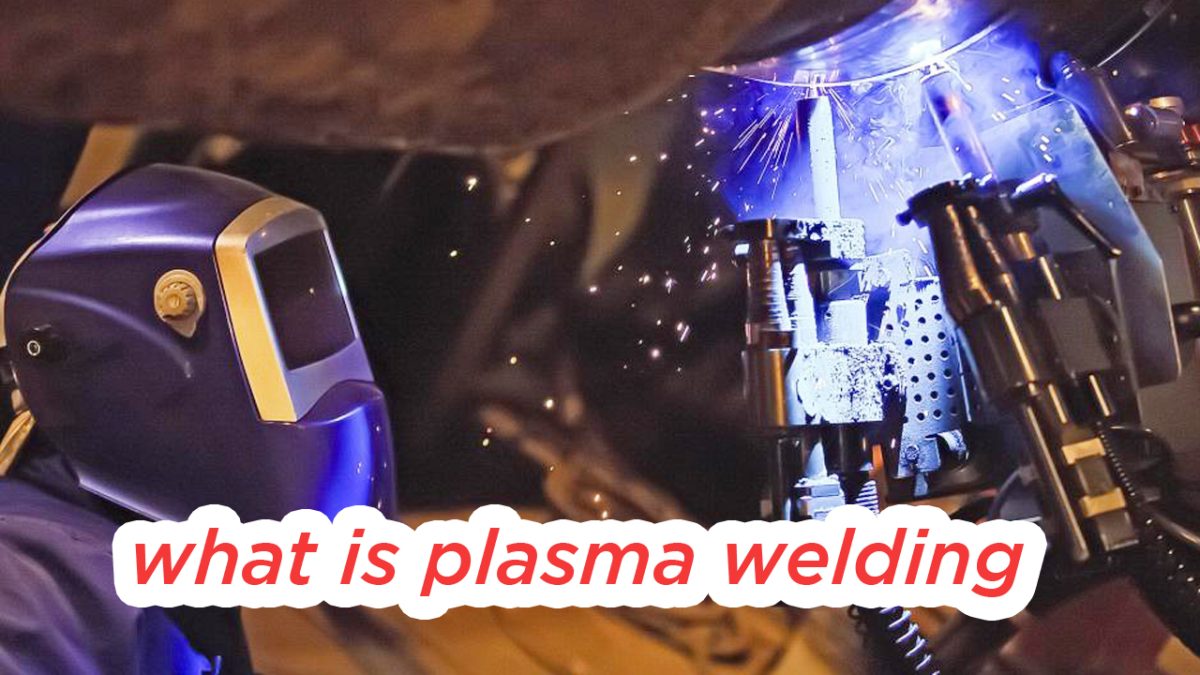
Image by thefabricator
One of the key benefits of plasma welding is its high energy density and focused heat. This makes it especially suitable for welding thin materials and intricate components. The ability to concentrate heat in a specific area results in minimal distortion and precise weld penetration, ensuring high-quality welds.
Plasma welding also offers excellent control over the heat input, which is essential for welding materials with different thicknesses. By adjusting the current, gas flow rate, and torch position, welders can achieve optimal heat control, reducing the risk of overheating or underheating the workpiece.
Advantages of plasma welding
Plasma welding offers several advantages over other welding techniques, making it an attractive choice for industries that require high precision and efficiency.
One of the main advantages is the ability to weld a wide range of materials, including stainless steel, aluminum, titanium, and other exotic alloys. This versatility makes plasma welding a valuable tool in industries where different materials are commonly used.
Another notable advantage is the high-quality welds produced by plasma welding. The focused heat and precise control over the welding process result in clean and aesthetically pleasing welds, with minimal spatter. This not only enhances the visual appeal of the finished product but also reduces the need for post-weld cleanup.
Additionally, plasma welding offers lower heat input compared to other welding techniques. This means that there is less heat transferred to the workpiece, reducing the risk of distortion or damage to sensitive components. The lower heat input also minimizes the need for subsequent heat treatment, saving time and costs.
Plasma welding process explained
The process of plasma welding involves several key components and steps that work together to create high-quality welds. Understanding the process is essential for welders to achieve optimal results.
Firstly, the plasma welding setup consists of a power supply, a plasma torch, and a shielding gas system. The power supply provides the necessary electric current to generate the arc, while the plasma torch directs the flow of gas and controls the arc. The shielding gas system ensures that the arc and the molten metal are protected from oxidation, preventing the formation of defects in the weld.
To start the welding process, the operator selects the appropriate settings on the power supply, such as the current and gas flow rate. The operator then positions the plasma torch at the desired location on the workpiece and initiates the arc by pressing the foot pedal or using a remote control.
Once the arc is established, the high-temperature plasma gas is generated, creating a small, concentrated heat source. The operator carefully manipulates the torch to guide the plasma gas along the welding path, melting the base material and creating a molten pool. The tungsten electrode and the filler metal, if used, are also consumed during the welding process, adding material to the molten pool.
As the operator moves the torch along the joint, the molten pool solidifies, forming a strong and durable weld. The shielding gas flowing from the plasma torch protects the weld zone from atmospheric contamination, ensuring the integrity of the weld.
Equipment and setup for plasma welding
To perform plasma welding, welders require specific equipment and a proper setup to achieve consistent and high-quality welds.
The main equipment needed for plasma welding includes a power supply, a plasma torch, and a shielding gas system. The power supply generates the electric current necessary to initiate and maintain the arc. It is important to select a power supply that matches the requirements of the welding application, considering factors such as the welding current range, duty cycle, and control features.
The plasma torch is another essential component of the plasma welding setup. It directs the flow of gas and controls the arc, ensuring precise and controlled welding. The torch should be selected based on factors such as the desired amperage range, torch cooling method, and torch configuration (handheld or machine-mounted).
The shielding gas system is crucial for protecting the arc and the molten metal from oxidation. It typically includes a gas flowmeter, gas hoses, and a gas source such as argon or a mixture of argon and helium. The gas flow rate should be adjusted according to the welding parameters and the specific requirements of the welding application.
In addition to the main equipment, welders may also need other tools and accessories such as tungsten electrodes, filler metals, welding cables, and safety equipment. It is important to ensure that all equipment is properly maintained and calibrated to achieve consistent and reliable welding results.
Plasma welding vs other welding techniques
Plasma welding offers distinct advantages over other welding techniques, making it a preferred choice in many applications. Let’s compare plasma welding with some commonly used welding methods to understand its unique benefits.
Plasma welding vs TIG welding
Tungsten Inert Gas (TIG) welding is a widely used welding technique known for its versatility and high-quality welds. While both plasma welding and TIG welding use a tungsten electrode and an inert gas, there are some key differences between the two.
One of the main differences is the arc characteristics. In plasma welding, the arc is more concentrated and intense, resulting in higher energy density and faster welding speeds compared to TIG welding. This makes plasma welding more suitable for welding thin materials and achieving deeper penetration.
Another difference is the gas flow. In TIG welding, the shielding gas flows around the electrode, protecting the weld zone. In plasma welding, the gas flows through the electrode, creating a high-temperature plasma gas that shields the arc and the molten metal. This offers better protection against oxidation and contamination, resulting in cleaner and more aesthetically pleasing welds.
Additionally, plasma welding allows for better control over the heat input due to its focused heat and precise arc control. This makes it easier to weld materials with different thicknesses and reduces the risk of overheating or underheating the workpiece.
Plasma welding vs MIG welding
Metal Inert Gas (MIG) welding, also known as Gas Metal Arc Welding (GMAW), is a popular welding method due to its ease of use and high productivity. While plasma welding vs MIG welding are both versatile welding techniques, they have some fundamental differences.
The main difference lies in the heat source. In MIG welding, the heat is generated by an electric arc between a continuously fed consumable electrode and the workpiece. In plasma welding, the heat is generated by an arc between a tungsten electrode and the workpiece, creating a high-temperature plasma gas. The concentrated heat of plasma welding allows for better control and precision, making it suitable for welding thin materials and intricate components.
Another difference is the shielding gas. In MIG welding, an external shielding gas, such as argon or a mixture of argon and carbon dioxide, is used to protect the arc and the weld zone. In plasma welding, the shielding gas is generated internally, ensuring better protection against oxidation and contamination.
Furthermore, plasma welding offers lower heat input compared to MIG welding. This reduces the risk of distortion or damage to the workpiece, especially when welding materials with different thicknesses. The lower heat input also results in less need for subsequent heat treatment, saving time and costs.
Plasma welding vs Laser welding
Laser welding is a precise and efficient welding technique that utilizes a high-energy laser beam to create welds. While laser welding vs plasma welding both offer high precision and control, they have some notable differences.
One of the main differences is the heat source. In laser welding, the heat is generated by a laser beam that is focused on the weld zone. In plasma welding, the heat is generated by an electric arc, creating a high-temperature plasma gas. The concentrated heat of plasma welding allows for better control and deeper penetration, making it suitable for welding thicker materials.
Another difference is the welding speed. Laser welding is known for its high welding speeds, making it ideal for applications that require rapid production rates. Plasma welding, on the other hand, offers a balance between speed and precision, making it suitable for a wide range of applications.
Additionally, laser welding is a non-contact welding method, which means that there is no physical contact between the heat source and the workpiece. This eliminates the risk of contamination from the welding tool and reduces the need for post-weld cleanup. Plasma welding, on the other hand, requires the use of a torch that comes into direct contact with the workpiece.
Applications of plasma welding
Plasma welding finds applications in various industries where high precision, efficiency, and quality are essential. Let’s explore some of the key applications of this advanced welding technique.
Automotive industry
The automotive industry relies on plasma welding for various welding applications. Plasma welding’s ability to weld thin materials and intricate components makes it suitable for welding automotive body panels, exhaust systems, and engine components. The high-quality welds produced by plasma welding ensure the structural integrity and longevity of these critical automotive parts.
Aerospace industry
In the aerospace industry, where safety and reliability are paramount, plasma welding plays a crucial role. Plasma welding is used to weld aircraft components such as fuel tanks, engine parts, and structural components. The precise control and high-quality welds provided by plasma welding ensure the integrity and performance of these aerospace parts under extreme conditions.
Manufacturing industry
The manufacturing industry benefits from plasma welding in various ways. Plasma welding is commonly used to weld stainless steel and aluminum components, such as kitchen appliances, furniture, and industrial equipment. The versatility and high-quality welds produced by plasma welding contribute to the overall efficiency and quality of manufacturing processes.
Electronics industry
The electronics industry requires precise and controlled welding for the assembly of electronic components. Plasma welding is used to weld delicate components such as connectors, wires, and circuit boards. The focused heat and minimal heat input of plasma welding ensure the integrity and functionality of these sensitive electronic parts.
Power generation industry
The power generation industry relies on plasma welding for the fabrication and repair of power plant components. Plasma welding is used to weld turbine blades, boiler tubes, and other critical components. The high-quality welds provided by plasma welding ensure the efficiency and reliability of power generation systems.
Safety considerations for plasma welding
While plasma welding offers numerous benefits, it is important to prioritize safety when performing this advanced welding technique. Here are some key safety considerations to keep in mind.
Personal protective equipment (PPE)
Welders should always wear appropriate personal protective equipment (PPE) to protect themselves from potential hazards. This includes welding gloves, safety glasses or goggles, welding helmets with appropriate filters, and flame-resistant clothing. The PPE should be in good condition and properly fitted to provide optimal protection.
Ventilation
Plasma welding generates fumes and gases that can be hazardous if inhaled. It is essential to have proper ventilation in the welding area to remove these fumes and maintain a safe working environment. Local exhaust ventilation systems or portable fume extractors can be used to effectively capture and remove welding fumes.
Fire safety
Plasma welding involves the use of high temperatures and electrical currents, which can pose a fire hazard. It is important to have fire safety measures in place, such as fire extinguishers and fire blankets, to quickly respond to any potential fires. Additionally, combustible materials should be kept away from the welding area to prevent accidental ignition.
Training and certification for safety
To ensure safety and proficiency in plasma welding, welders should undergo proper training and obtain the necessary certifications. Training programs provide valuable knowledge and skills, covering topics such as welding techniques, equipment setup, safety procedures, and troubleshooting. Certification validates the welder’s competence and ensures compliance with industry standards.
Training and certification for plasma welding
Training and certification are essential for welders who want to excel in plasma welding. Proper training equips welders with the necessary knowledge and skills, while certification validates their competence and ensures adherence to industry standards.
Welders can undergo training programs offered by welding schools, vocational schools, or technical institutes. These programs cover various aspects of plasma welding, including welding theory, equipment setup, welding procedures, safety protocols, and hands-on practice. The duration and content of the training programs may vary depending on the institution and the desired level of expertise.
Upon completing the training program, welders can pursue certification to validate their skills and knowledge. Certification is typically offered by recognized organizations such as the American Welding Society (AWS) or the International Institute of Welding (IIW). The certification process may involve written exams, practical tests, and documentation of work experience.
Obtaining certification not only demonstrates a welder’s proficiency in plasma welding but also enhances their career prospects. Certified welders are often preferred by employers due to their demonstrated expertise and adherence to industry standards.
Final Thoughts
Plasma welding is an advanced welding technique that offers precise control, high-quality welds, and lower heat input for industries requiring high precision and efficiency. Its high energy density and focused heat make it suitable for welding thin materials and intricate components, while its versatility allows for the welding of various materials. Plasma welding finds applications in industries such as automotive, aerospace, manufacturing, electronics, and power generation.
To achieve optimal results in plasma welding, it is crucial to have the appropriate equipment and setup. The power supply, plasma torch, and shielding gas system play key roles in creating consistent and high-quality welds. Safety considerations should also be prioritized, including the use of personal protective equipment, proper ventilation, fire safety measures, and adherence to industry standards.
Welders can enhance their skills and knowledge in plasma welding through training programs and obtain certification to validate their competence. By mastering the art of plasma welding, welders can contribute to the efficiency, quality, and reliability of various industries that rely on this advanced welding technique.