Aerospace welding plays a vital role in the aerospace industry, as it is responsible for ensuring the structural integrity and safety of aircraft. The welding process involves joining metal components through the application of heat and pressure, creating strong and durable connections. In the aerospace industry, where aircraft are subjected to extreme temperatures, high pressure, and various environmental conditions, precision and expertise are crucial.
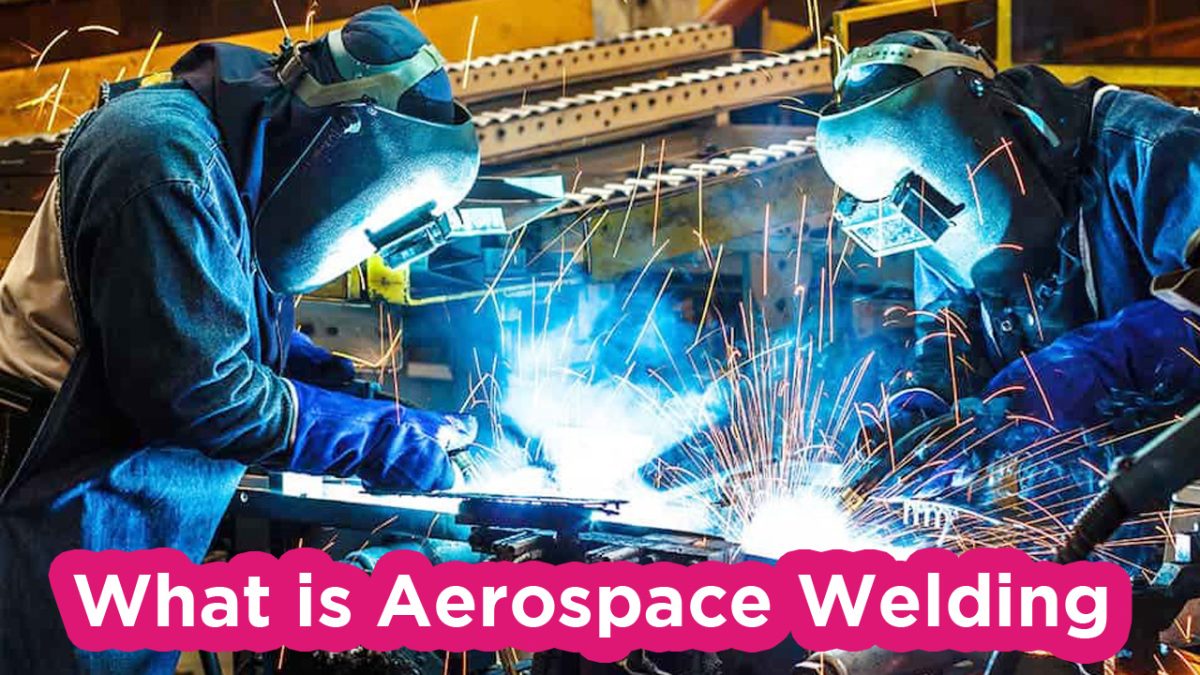
Importance of Aerospace Welding
One of the key reasons why aerospace welding is of utmost importance is the need to maintain the structural integrity of aircraft. The wings, fuselage, and other components of an aircraft experience tremendous forces during flight. A failure in any of these components due to a weak weld could have catastrophic consequences. Aerospace welders, therefore, have the critical responsibility of ensuring that the welds can withstand these forces and function flawlessly under extreme conditions.
In addition to ensuring structural integrity, aerospace welding also contributes to the overall performance and efficiency of aircraft. By joining metal components together, welders create a unified structure that enhances the aerodynamic properties of the aircraft. This, in turn, improves fuel efficiency and reduces drag, allowing aircraft to travel faster and consume less fuel. Aerospace welding, therefore, plays a crucial role in the development of more advanced and efficient aircraft.
Aerospace welding is essential for the safety of pilots, crew members, and passengers. Welded components, such as engine mounts and landing gear, must be able to withstand the stresses and forces encountered during takeoff, landing, and flight. Without the expertise of aerospace welders, these critical components could fail, jeopardizing the safety of everyone on board.
Aerospace welding is of utmost importance in the aerospace industry due to its role in ensuring the structural integrity, performance, and safety of aircraft. The expertise and precision of aerospace welders are essential in creating strong and durable connections that can withstand extreme conditions.
Types of welding techniques used in aerospace welding
Aerospace welding encompasses a wide range of techniques that are used to join metal components together. Each technique has its own advantages and is selected based on the specific requirements of the project. Here are some of the most commonly used welding techniques in aerospace welding:
TIG (Tungsten Inert Gas) Welding
TIG welding is a widely used technique in aerospace welding due to its versatility and ability to produce high-quality welds. It involves the use of a tungsten electrode and an inert gas, typically argon, to create a controlled arc between the electrode and the workpiece. The arc generates the heat necessary to melt the metal, while the inert gas shields the weld from atmospheric contamination.
TIG welding is particularly suitable for welding thin materials and intricate components, as it allows for precise control of the welding parameters. This technique produces clean and aesthetically pleasing welds with minimal spatter, making it ideal for visible or highly critical welds in aerospace applications.
Laser Beam Welding
Laser beam welding is a highly precise and efficient welding technique used in aerospace applications. It involves focusing a high-energy laser beam onto the workpiece, which melts and fuses the metal together. Laser beam welding offers several advantages, including minimal heat input, narrow heat-affected zone, and high welding speeds.
This technique is commonly used for joining thin materials, such as sheet metal, and for welding complex and hard-to-reach areas. It provides excellent control over the welding process and produces high-quality welds with minimal distortion. Laser beam welding is particularly suitable for aerospace applications that require precise and intricate welds.
Electron Beam Welding
Electron beam welding is another technique widely used in aerospace welding. It involves directing a focused beam of high-velocity electrons onto the workpiece, which generates heat and melts the metal. Electron beam welding offers several advantages, including deep penetration, narrow heat-affected zone, and high welding speeds.
This technique is commonly used for welding thick materials and for joining dissimilar metals. Electron beam welding provides excellent control over the weld pool and produces high-quality welds with minimal distortion. It is particularly suitable for aerospace applications that require strong and reliable welds.
In addition to these techniques, other welding methods such as resistance welding, friction stir welding, and plasma arc welding are also utilized in aerospace welding, depending on the specific requirements of the project. The selection of the welding technique is based on factors such as the materials being joined, the desired strength and quality of the weld, and the production requirements.
Materials used in aerospace welding
Aerospace welding involves the joining of various metal components, and the choice of materials is critical to ensuring the strength, durability, and performance of the welds. Different materials have different properties, and selecting the right materials for each project is essential.
One of the most commonly used materials in aerospace welding is aluminum. Aluminum alloys are lightweight, corrosion-resistant, and possess excellent strength-to-weight ratio, making them ideal for aerospace applications. Aluminum welds well using various welding techniques, such as TIG welding and laser beam welding, and is commonly used in the construction of aircraft frames, wings, and other components.
Another important material used in aerospace welding is titanium. Titanium alloys offer high strength, excellent corrosion resistance, and good heat resistance, making them suitable for extreme aerospace environments. Titanium welding requires specialized techniques, such as TIG welding and electron beam welding, due to the reactive nature of the metal.
Steel is also commonly used in aerospace welding, particularly for components that require high strength and durability. Carbon steel and stainless steel alloys are often used in the construction of engine mounts, landing gear, and other critical components. Welding steel requires careful attention to preheating, heat input, and post-weld heat treatment to ensure the desired properties of the weld.
In addition to these materials, aerospace welding may involve the joining of other metals and alloys, such as nickel alloys, superalloys, and composites. Each material has its own unique properties and welding requirements, and aerospace welders must have a thorough understanding of metallurgy and materials science to select the appropriate materials and welding processes for each project.
By carefully selecting the right materials and employing the appropriate welding techniques, aerospace welders can ensure the strength, durability, and performance of the welds, contributing to the overall safety and reliability of aircraft.
Safety precautions in aerospace welding
Safety is of paramount importance in aerospace welding, as the process involves the use of high temperatures, electrical currents, and potentially hazardous materials. Without proper safety precautions, aerospace welders are at risk of injury or exposure to harmful substances. Implementing safety measures is essential to protect the welders and ensure a safe working environment.
One of the primary safety precautions in aerospace welding is the use of personal protective equipment (PPE). Welders must wear appropriate PPE, including welding helmets with auto-darkening filters, safety glasses, welding gloves, flame-resistant clothing, and steel-toed boots. These protective gears provide protection against the intense light, sparks, heat, and molten metal associated with welding.
In addition to PPE, proper ventilation is crucial in aerospace welding to prevent the inhalation of harmful fumes and gases. Welding fumes can contain toxic substances, such as metal oxides and shielding gases, which can pose health risks if inhaled. Adequate ventilation, such as local exhaust ventilation or fume extraction systems, should be in place to remove and control welding fumes.
Another important safety precaution is the proper handling and storage of welding materials and equipment. Welding gases, such as argon, helium, and nitrogen, are typically used in aerospace welding and must be handled with care. These gases can displace oxygen and pose a suffocation risk if not used or stored properly. Welding equipment, including welding machines and tools, should be regularly inspected and maintained to ensure safe and reliable operation.
Furthermore, aerospace welders must be trained in proper welding techniques and safety procedures. They should have a thorough understanding of the hazards associated with welding and be knowledgeable about safe work practices. Regular training and certification programs are essential to keep welders up-to-date with the latest industry standards and best practices.
Overall, safety precautions in aerospace welding are essential to protect the welders and create a safe working environment. By implementing proper safety measures, aerospace welders can minimize the risk of injury or exposure to hazardous substances, ensuring the well-being of themselves and their colleagues.
How to Become an Aerospace Welder?
If you aspire to become an aerospace welder, there are several steps you can take to build a successful career in this field. Becoming an aerospace welder requires a combination of specialized training, certification, and hands-on experience. Here are the steps you can follow to pursue a career in aerospace welding:
Step 1: Obtain a high school diploma or equivalent
The first step to becoming an aerospace welder is to obtain a high school diploma or equivalent. A strong foundation in math, science, and technical subjects will be beneficial in understanding the principles of welding and materials science.
Step 2: Enroll in a welding program or vocational school
After completing high school, you can enroll in a welding program or vocational school that offers specialized training in aerospace welding. These programs typically cover topics such as welding techniques, metallurgy, blueprint reading, and safety procedures. Hands-on training in a well-equipped welding lab is an integral part of the program, allowing you to gain practical experience in welding.
Step 3: Gain practical experience through an apprenticeship or internship
To further enhance your skills and knowledge in aerospace welding, it is advisable to gain practical experience through an apprenticeship or internship. These opportunities provide valuable hands-on experience under the guidance of experienced professionals. You will have the opportunity to work on real-world projects and learn from seasoned aerospace welders.
Step 4: Obtain relevant certifications
Certifications are an essential credential in the field of aerospace welding, as they demonstrate your expertise and competence. The American Welding Society (AWS) offers several certifications, such as Certified Welding Inspector (CWI) and Certified Welding Educator (CWE). These certifications require passing a written and practical exam, demonstrating your knowledge and skills in welding.
Step 5: Continuously update your skills and knowledge
Aerospace welding is a constantly evolving field, and it is important to continuously update your skills and knowledge to stay ahead. Attend workshops, seminars, and conferences to learn about the latest advancements in welding technology and techniques. Stay informed about industry standards and best practices to ensure that your skills remain relevant and up-to-date.
Step 6: Build a strong professional network
Networking is crucial in any profession, and aerospace welding is no exception. Build a strong professional network by joining industry organizations, attending trade shows, and connecting with fellow professionals. Networking can open doors to new opportunities, provide mentorship, and keep you updated on the latest trends and job openings in the field.
By following these steps, you can establish a successful career as an aerospace welder. Remember that dedication, continuous learning, and a passion for the field are key to excel in this demanding and rewarding profession.
Education and training requirements for aerospace welding
A career in aerospace welding requires a combination of education and training to develop the necessary skills and knowledge. While a high school diploma or equivalent is the minimum educational requirement, specialized training in welding is essential to excel in this field. Here are the education and training requirements for aerospace welding:
High school diploma or equivalent
To pursue a career in aerospace welding, it is essential to have a high school diploma or equivalent. A strong foundation in math, science, and technical subjects will be beneficial in understanding the principles of welding and materials science.
Welding program or vocational school
After completing high school, aspiring aerospace welders can enroll in a welding program or vocational school that offers specialized training in welding. These programs typically cover topics such as welding techniques, metallurgy, blueprint reading, and safety procedures. Hands-on training in a well-equipped welding lab is an integral part of the program, allowing students to gain practical experience in welding.
Apprenticeship or internship
To further enhance their skills and knowledge, students can gain practical experience through an apprenticeship or internship. These opportunities provide valuable hands-on experience under the guidance of experienced professionals. Students will have the opportunity to work on real-world projects and learn from seasoned aerospace welders.
Certifications
Certifications are an important credential in the field of aerospace welding, as they demonstrate expertise and competence. The American Welding Society (AWS) offers several certifications, such as Certified Welding Inspector (CWI) and Certified Welding Educator (CWE). These certifications require passing a written and practical exam, demonstrating knowledge and skills in welding.
In addition to formal education and training, continuous learning and professional development are crucial for aerospace welders. Attending workshops, seminars, and conferences can provide opportunities to learn about the latest advancements in welding technology and techniques. Staying informed about industry standards and best practices ensures that skills remain relevant and up-to-date.
Overall, a combination of education, specialized training, hands-on experience, and certifications is necessary to become an aerospace welder. Continuous learning and professional development are also essential to stay current in this rapidly evolving field.
Skills and qualities needed to excel in aerospace welding
Aerospace welding is a demanding field that requires a unique set of skills and qualities to excel. In addition to technical expertise in welding techniques and materials science, aerospace welders must possess certain personal qualities that contribute to their success. Here are some of the skills and qualities needed to excel in aerospace welding:
Technical skills
Aerospace welders must have a strong foundation in welding techniques, such as TIG welding, laser beam welding, and electron beam welding. They should be proficient in reading blueprints, understanding welding symbols, and interpreting technical specifications. Knowledge of metallurgy and materials science is essential to select the right welding processes and materials for each project.
Attention to detail
Aerospace welding requires meticulous attention to detail, as even the smallest imperfection in a weld can have serious consequences. Aerospace welders must have a keen eye for precision and be able to consistently produce high-quality welds. They should pay close attention to welding parameters, joint fit-up, and cleanliness of the workpiece to ensure the integrity of the weld.
Problem-solving skills
Aerospace welders often encounter challenges and obstacles during the welding process. They must have strong problem-solving skills to identify and troubleshoot issues that may arise. The ability to think critically and find innovative solutions is crucial in ensuring the successful completion of a welding project.
Manual dexterity
Aerospace welding requires excellent manual dexterity, as welders must manipulate welding torches, electrodes, and workpieces with precision. They should have steady hands and good hand-eye coordination to achieve accurate welds.
Conclusion
Aerospace welding plays a crucial role in the aviation industry by joining metal components to ensure structural integrity and safety. It involves precise techniques and adherence to strict quality standards. Becoming an aerospace welder requires specialized training, including formal education and practical experience. As the demand for air travel continues to grow, the importance of skilled aerospace welders will only increase.