Mig welding carbon steel is a special type of welding that finds use in the construction industry. This type of welding is done to join two or more flat plates of metal together at a joint. The joint can be either welded directly onto another component or used as part of a larger structure like a building or bridge. This guide provides information on what mig welding carbon steel structures is, how it is done and the possible challenges associated with this method. This is apractical guide to using mig welder.
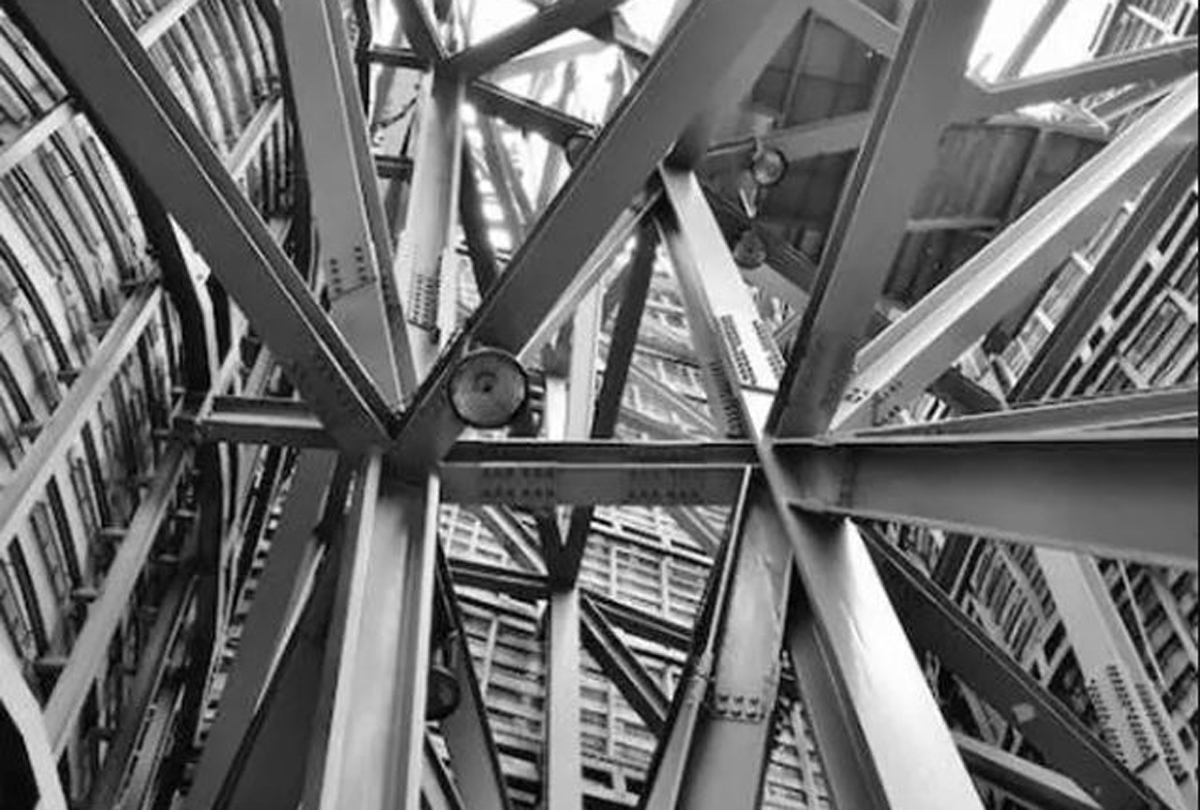
What is mig welding carbon steel?
Mig welding is a special type of welding that finds use in the industry sector. It is used to join two or more flat plates of metal together at a joint. Mig welding consists of a gas shielding arc and is a relatively low speed process that is used to join metals with different carbon contents, like carbon steel and aluminum. When welding with a mig welder, the electrodes are essentially the same as for stick welding, with the only difference being the shielding gas. There are no spatter issues like with stick welding, and the weld joint is smooth with no clogging. It is common to see carbon steel welded using a mig welder.
The carbon content in carbon steel makes it difficult to weld using a gas arc welding method. Therefore, the joint is welded using a shielded arc welding method. Shielded arc welding is a low heat welding method that uses a low voltage and a small amount of shielding gas to weld the joint.
Welding parameters for mig welding carbon steel
Voltage – We weld at a high voltage of between 30kV and 40kV. This is high enough to weld the base material of the joint and also heat up the base material sufficiently to melt the filler wire and electrode.
Amperage – We weld at between 10-12A for mig welding carbon steel. This is high enough to weld the base material of the joint and also heat up the base material sufficiently to melt the filler wire and electrode.
Gas flow – We use Argon as our shielding gas for mig welding carbon steel. The gas flow rate varies depending on the base material of the joint and also the thickness of the base material being welded. For example, if we are welding a steel pipe, we would use less gas flow than if welding steel plate.
Equipment required to weld using mig welder
Mig welder – This is used to create the arc and transfer the electricity to the welding electrodes.
Shielding Gas – This comes in the form of an argon tank. The amount of gas in the tank depends on the amount of welding you want to do.
Ground electrode – This electrode is used to ground the weld.
Power source – This is used to provide the power required to weld using the mig welder.
Welder stand – This is used to set up the welding equipment and also support the work piece during welding.
Benefits of mig welding carbon steel
- It is a cost-effective welding method for joining different types of base materials.
- It has a long service life compared to arc welding.
- It is safe and does not create any sparks that can cause fires. – It has low thermal shock resistance and produces low amounts of heat.
- It is applicable in outdoor environment because it does not produce any toxic fumes.
- It is applicable in all climatic conditions where it is not possible to use an arc welding machine.
Limitations of Mig Welding Carbon Steel
There are some limitations of mig welding carbon steel:
- It is not suitable for welding large structures like ship hulls or bridges.
- It has low ductility and yield strength.
- It is not suitable for welding structural components that have important properties like high strength or high impact resistance.
- Visual quality of the weld is poor.
- The base material joint gets weak easily.
- The weld is prone to cracking.
- It is not suitable for joints that require high weld strength.
- It is not suitable for joints that have different carbon contents like carbon steel and aluminium.
- It is not suitable for long service life projects.
Last word about mig welding carbon steel
Mig welding carbon steel is a type of welding that finds use in the construction sector. It is used to join two or more flat plates of metal together at a joint. Various welding parameters are used to make this type of welding work, and the shield gas that is used is Argon. The welding parameters used for mig welding are high enough to weld the base material of the joint and also heat up the base material sufficiently to melt the filler wire and electrode. Therefore, there is no danger of the joint breaking due to the heat from the arc.
The joint is smooth with no clogging and is also safe and produces no sparks that can cause fire. All these make mig welding carbon steel a cost-effective welding method for joining different types of base materials. It has a long service life compared to arc welding, is safe and does not create any sparks that can cause fires. It produces low amounts of heat and also produces low thermal shock resistance. If you have any questions regarding mig welding carbon steel, please don’t hesitate to contact us.