With the growing demand for steel, manufacturers are now able to produce it in larger quantities and at a lower cost. It is no longer restricted to traditional uses such as building structures or fittings, but can also be used for industries that require strong and lightweight materials. Tig welding carbon steel is a process that involves combining carbon steel with other alloys called Tig processes. It not only mixes the two metals together to make stronger steels but also creates more stable welds by ensuring consistent penetration of the electrode into the joint so there are no cracks or fractures from thermal stresses later on.
Read on to learn more about working with carbon steel and how tig welding can help you if you’re planning to get started.
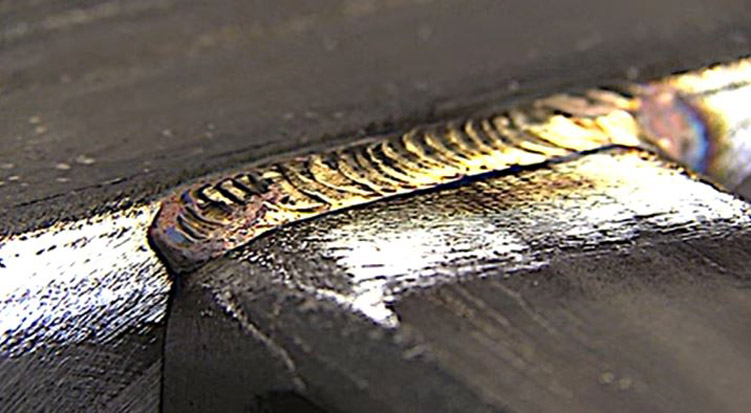
Photo by weldingtipsandtricks
What is carbon steel ?
Carbon steel is a type of steel that contains carbon. It is an alloy, so the carbon content is higher in some steels than others. The carbon content determines the properties of the steel, including its strength and malleability, so it’s important to know what type of carbon steel is being welded. Carbon is an alloying element in steel, which means it’s added to make the alloy more dense. The amount of carbon in a particular type of steel will determine its performance, durability, and cost. Steel with a low, 1.25% carbon content is known as mild steel and has a higher malleability, so it can be shaped easily with rolls, hammers, and other equipment.
It’s used in a wide variety of products, including cars, appliances, tools, and construction. Steel with a 2.5% carbon content is known as low-carbon steel, making it stronger, but more expensive. It’s used in a variety of products, including construction, appliances, tools, and ships. Steel with a 5.5% carbon content is known as high-carbon steel, making it stronger, but more expensive. It’s used in a variety of products, including ships, bridges, and cars.
Required to welding carbon steel
Carbon steel is used in many applications that require a high level of durability, strength, and resistance to stress and impact from external forces. For example, car parts such as axles, transmissions, and engines are frequently made from carbon steel. Specialized welding processes are used to produce high-quality welds that require high temperatures, great skill, and the right equipment. However, not all welding processes can be used on carbon steel, so the manufacturer must verify that tig welding is the right option for creating the desired product.
When working with carbon steel, the manufacturer must verify that the equipment is capable of handling the material, which determines the type of equipment that should be used. This can include pressure welders, arc welders, or MIG welders.
How to Tig Welding Carbon Steel
Carbon steel is a challenging material for welding, therefore, welding it requires advanced welding skills and equipment to ensure the weld is strong and durable. For tig welding carbon steel, the welder has two options. The first is to use a pure-carbon electrode with a minimum 10% carbon content. The other option is to use a tungsten electrode with a minimum 17% tungsten content.
As the welder switches the welding gun to pure-carbon electrodes, the joint becomes easier to weld because the relative coefficient of friction between the joint and the electrodes is low. On the other hand, welding with a tungsten electrode makes the joint more difficult to weld because the relative coefficient of friction between the joint and the electrodes is higher.
Pros of Tig Welding Carbon Steel
Tig welding carbon steel is a strong bonding process that produces a longer-lasting weld. The process also allows you to maintain a consistent penetration into the joint, which prevents cracking and breaking due to thermal stress. Similar to the way electroplating is used to make alloys stronger and more durable, tig welding uses the sintering process of welding to join the metals together. This creates a dense and stable weld, which is ideal when operating machinery that requires a sturdy joint. Tig welding also uses low-oxygen gas as a shielding gas source, which keeps the weld cleaner, producing a stronger joint and less damage to the environment.
Cons of Tig Welding Carbon Steel
Tig welding carbon steel requires advanced skills and equipment that are not accessible to all welders. If you are new to welding or have no experience, you may find it difficult to overcome the challenges presented by the material. Additionally, tig welding carbon steel can be more expensive than other materials, as it is not common in the industry. Another potential negative of tig welding carbon steel is that it produces more heat than other welding processes, which means it’s more difficult to control the temperature. If the weld is too hot, it can damage the joint, which can lead to excessive wear on the equipment.
Last Word about Tig Welding Carbon Steel
Carbon steel is a challenging material that requires advanced welding skills and equipment. However, using a pure-carbon electrode with a minimum 10% carbon content with a tungsten electrode with a minimum 17% tungsten content can produce a strong weld that is resistant to thermal stress and lasts longer. While the process of welding carbon steel is difficult, it produces stronger joints and lasts longer than other materials, making it a worthwhile investment for manufacturers. If you are planning to work with carbon steel, learn more about welding carbon steel, such as how it’s used, how it’s made, and how to work with carbon steel.