Welcome to our comprehensive guide on Mig welding titanium. In this guide, we will be sharing valuable tips, techniques, and best practices to help you enhance your welding skills and produce high-quality results when working with titanium. Titanium is a challenging material to weld due to its high melting point and reactivity to oxygen. However, with the right knowledge and equipment, Mig welding titanium can be done efficiently and safely.
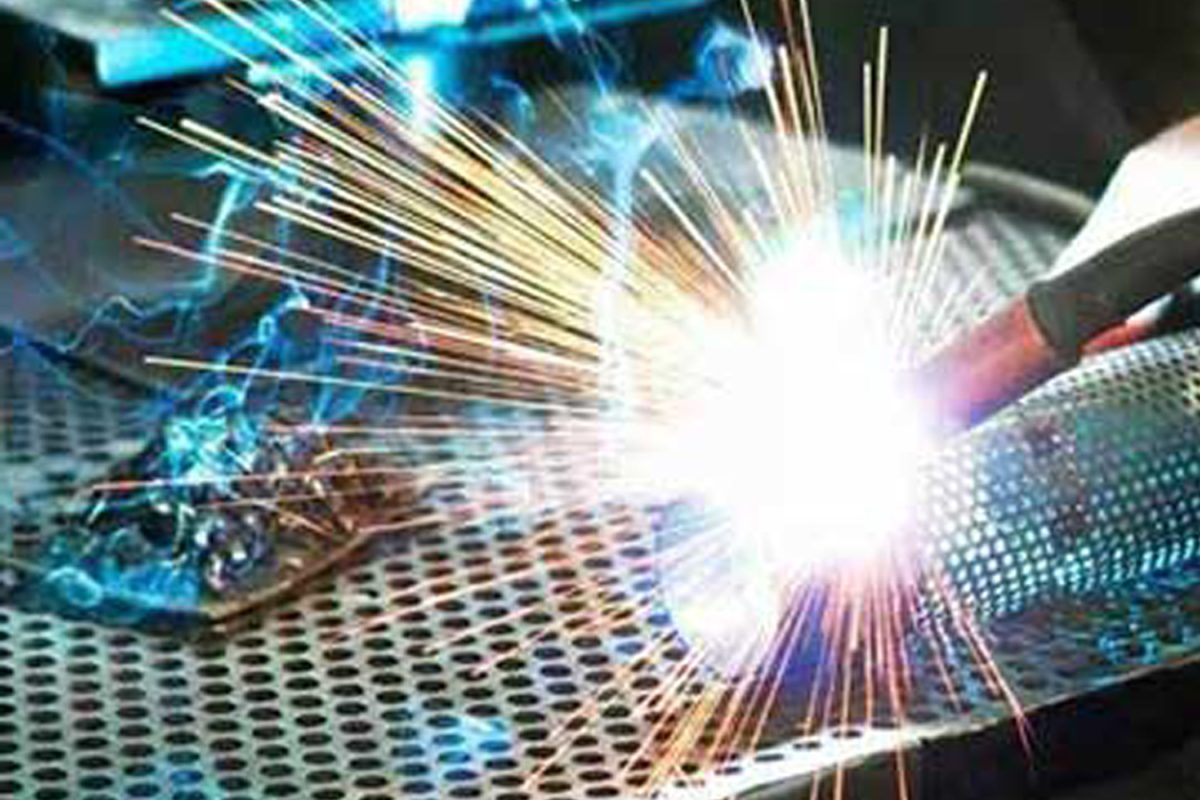
Image by hynickelalloy
Whether you are a beginner welder looking to expand your skills or a seasoned professional seeking to perfect your techniques, this guide is for you. Let’s begin by exploring the advantages of Mig welding titanium and why it’s a preferred choice for many welding projects.
Advantages of Mig Welding Titanium
When it comes to welding, titanium is a popular choice for many different projects because of the several benefits it has to offer over other metals. Mig welding titanium is especially advantageous as it is a quick and efficient method of welding the metal. Here are some of the significant benefits of using Mig welding for titanium:
1. Strength
Titanium is known for its exceptional strength-to-weight ratio, making it a popular choice for applications where strength and durability are essential. When welded with the Mig welding process, titanium can retain its strength and integrity, creating reliable welds that are strong enough to handle heavy loads and high-stress environments.
2. Corrosion Resistance
One of the most significant advantages of titanium is its resistance to corrosion. This property makes it an excellent choice for welding in harsh environments, such as chemical plants or offshore oil rigs. When welded with Mig welding, the corrosion resistance of titanium is maintained, making it an ideal material for long-lasting structures and projects.
3. Heat Resistance
Titanium has a high melting point, making it an excellent choice for applications requiring high heat resistance. When welded with Mig welding, titanium can withstand high temperatures and retain its strength and integrity, making it an ideal choice for aerospace and other high-stress applications.
4. Lightweight
Compared to many other metals, titanium is incredibly lightweight, making it an ideal choice for projects that require strength without adding significant weight. When welded with Mig welding, titanium retains its lightweight properties, making it an ideal material for aerospace, automotive, and medical projects.
Overall, Mig welding titanium offers several advantages that make it a popular choice for many different welding projects. From its superior strength and corrosion resistance to its heat resistance and lightweight properties, titanium is an excellent choice for many different applications.
The Mig Welding Titanium Process: Equipment and Safety Precautions
Before diving into the Mig welding titanium process, it is important to have the right equipment on hand.
Mig Welding Titanium Equipment
When selecting equipment for Mig welding titanium, it is crucial to choose a unit that can handle the unique properties of titanium. Typically, you will need a welding machine with a pulsing feature, as well as a wire feeder that can push the wire through the welding gun at a consistent rate.
You will also need a shielding gas to protect the weld pool from contamination. Argon is ideal for welding titanium as it prevents oxidation.
Mig Welding Titanium Safety Precautions
Welding titanium poses some unique Mig welding safety hazards that welders must take into consideration.
Firstly, titanium dust can be highly flammable and explosive, so it’s vital to keep your workplace clean and free of debris. Secondly, titanium reacts with oxygen at high temperatures, producing harmful fumes and oxides. It is critical to ensure you have adequate ventilation, or you risk exposure to these hazardous substances.
To protect yourself from harmful radiation and burns, it’s crucial to wear appropriate protective gear, such as a welding helmet, gloves, and clothing.
Now that you have your equipment and safety protocols in place, let’s explore the Mig welding titanium process in detail.
Tips and Techniques for Successful Welding
Mastering Mig welding titanium requires specific techniques to ensure optimal results. Below are some valuable tips and techniques that will help you master the art of Mig welding titanium:
- Set the proper voltage and wire speed for the thickness of the titanium
- Preheat the material before welding to reduce the risk of cracking
- Use a shielding gas with a high argon content to prevent oxidation
- Manage heat input by controlling the travel speed and pausing to allow the material to cool
- Keep the weld pool small to reduce heat input and prevent warping
- Clean the material thoroughly and remove all contaminants before welding
- Manage the weld pool carefully to prevent spatter and maintain good fusion
- Use a back purge to prevent contamination on the backside of the weld
- Utilize pulse welding to help control the heat input and reduce distortion
By implementing these tips and techniques, you’ll be able to produce high-quality Mig welds on titanium with ease. Don’t hesitate to experiment and find what works best for you and your welding project!
Mig Welding Titanium Joints and Filler Wire Selection
When welding titanium, creating strong and durable joints is crucial. The most common types of joints used in titanium welding are butt joints, lap joints, corner joints, and T-joints. Butt joints are the most straightforward joint to weld, while lap joints are the most common joint type used in aerospace applications.
When selecting filler wire for titanium welding, it’s crucial to choose a product with a similar composition to the base metal. The most commonly used filler wire for welding titanium is commercially pure titanium. However, if you need higher strength and toughness, you may need to use alloys such as Ti-6Al-4V.
Joint Type | Filler Wire Selection |
---|---|
Butt joint | Commercially pure titanium |
Lap joint | Commercially pure titanium |
Corner joint | Ti-6Al-4V |
T-joint | Ti-6Al-4V |
It’s worth noting that unlike other metals, titanium filler wire cannot be reused. Therefore, you should ensure you have sufficient filler wire available before starting the welding process.
- Select the correct joint type according to the welding project requirements
- Choose filler wire with a similar composition to the base metal
- Make sure to have enough filler wire available as it cannot be reused
Conclusion
Now that you’ve reached the end of this article, you should have a solid understanding of the Mig welding titanium process. With the help of this guide, you can confidently tackle welding projects involving titanium. Remember to always prioritize safety measures, such as wearing protective gear and taking necessary precautions when dealing with the high heat produced during welding.
Implement the tips and techniques shared in this article to ensure optimal results. Whether it’s setting the right voltage and wire speed or selecting the appropriate filler wire, every step is crucial to creating strong and durable joints. Now, it’s time to put your new skills to the test and create exceptional work with Mig welding titanium!
FAQ
What is Mig welding titanium?
Mig welding titanium is a welding process that uses a continuous wire-fed electrode to join pieces of titanium together. It is known for its strength, corrosion resistance, and versatility.
What are the advantages of Mig welding titanium?
Mig welding titanium offers several advantages, including superior strength, excellent resistance to corrosion, and the ability to weld thin materials without distortion. Additionally, it provides high-quality welds with minimal spatter and a clean appearance.
What equipment do I need for Mig welding titanium?
To Mig weld titanium, you will need a Mig welder capable of handling titanium, a suitable gas mixture (typically argon with a small amount of helium), and the appropriate consumables, such as titanium filler wire and shielding gas.
What safety precautions should I take when Mig welding titanium?
When Mig welding titanium, it is crucial to wear appropriate personal protective equipment (PPE) such as gloves, a welding helmet with a shade specifically for titanium, and a welding jacket. Ensure proper ventilation in your workspace and follow all safety protocols for handling and storing titanium and its alloys.
What are some tips for successful Mig welding titanium?
To achieve successful Mig welding with titanium, it’s important to set the proper voltage and wire speed, manage heat input, and control the weld pool. Additionally, maintaining clean and contaminant-free surfaces, using a back purging technique, and practicing proper joint preparation are essential.
How do I select filler wire and joints for Mig welding titanium?
When selecting filler wire for Mig welding titanium, choose a wire that matches the composition of the base metal. As for joints, consider designs that ensure proper fit-up and maximize joint strength. Common joint types for titanium include butt joints, fillet joints, and T-joints.