Resistance seam welding is a commonly used welding technique in the manufacturing industry that joins two or more overlapping metal sheets by passing an electric current through them. This process creates a strong, durable bond that is resistant to corrosion and can withstand high temperatures and mechanical stress. Resistance seam welding is widely used in a variety of applications, including automotive, aerospace, and construction. In this ultimate guide, we will explore the techniques, applications, and benefits of resistance seam welding, providing a comprehensive resource for professionals in the welding industry.
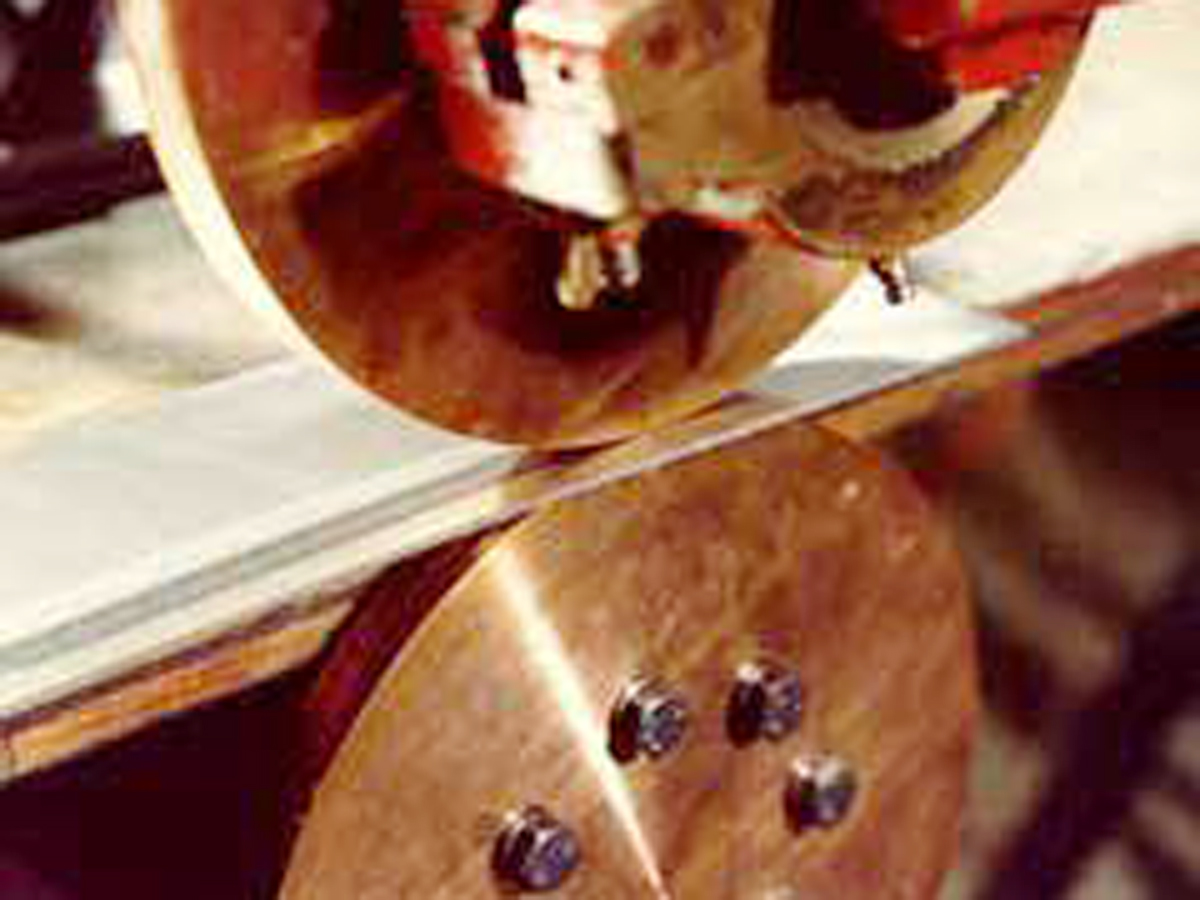
Photos by pdfcoffee
What is Resistance Seam Welding?
Resistance seam welding is a versatile welding technique that offers numerous benefits in various industries. To fully understand this process, it is essential to grasp the underlying principles and techniques involved. Resistance seam welding involves passing an electric current through overlapping metal sheets to create a strong bond. The sheets are held together between two electrodes, and pressure is applied to ensure a secure connection. As the electric current flows through the metal, resistance generates heat, which melts the metal at the joint. When the current is stopped, the molten metal solidifies, forming a continuous seam.
This process is highly efficient and delivers consistent results, making it ideal for high-volume production. It offers several advantages, including enhanced structural integrity, resistance to corrosion, and superior heat resistance. These properties make resistance seam welding suitable for a wide range of applications, such as automotive bodywork, aerospace components, and structural fabrication.
Different Techniques for Resistance Seam Welding
Resistance seam welding employs various techniques to achieve optimal weld quality and meet specific industry requirements. Understanding these techniques is crucial for ensuring successful welds and efficient production.
Spot Welding
Spot welding is the most common technique used in resistance seam welding. It involves creating welds at discrete points along the seam, rather than welding the entire length simultaneously. This technique is ideal for thin or irregularly shaped materials, as it allows for precise control and minimizes the risk of distortion.
Roll Spot Welding
Roll spot welding is a variation of spot welding that utilizes rolling electrodes to create a continuous seam. It is commonly used to join two overlapping sheets of metal with a circular or semi-circular cross-section. This technique improves the overall strength and integrity of the welds, particularly in applications that require high resistance to tensile forces.
Stitch Welding
Stitch welding involves creating intermittent spot welds along the seam, instead of continuous ones. This technique is often used for thicker materials or joints with irregular spacing. It provides more flexibility in terms of joint design and allows for easier weld inspection and repair.
Projection Welding
Projection welding utilizes specially designed projections or embossments on one or both metal sheets to concentrate the electric current and generate localized heat at specific points. This technique is commonly used in applications where two or more metal parts need to be joined together, such as in wire basket fabrication or automotive assembly.
In the following section, we will explore the diverse applications of resistance seam welding across various industries, highlighting the benefits and specific requirements of each application. Stay tuned for an in-depth analysis!
Applications of Resistance Seam Welding
Resistance seam welding has a wide range of applications across various industries, thanks to its ability to provide strong, durable, and consistent welds. Let’s delve into some of the key applications where resistance seam welding is commonly used:
Automotive Industry
Resistance seam welding plays a vital role in the automotive industry, especially in the assembly of car body parts. From joining panels, doors, and hoods to constructing fuel tanks and exhaust systems, resistance seam welding ensures structural integrity and enhances the overall safety of vehicles. Its ability to create strong and leak-proof welds makes it crucial for manufacturing high-quality automobiles.
Aerospace Industry
In the aerospace industry, resistance seam welding is extensively used for joining thin sheets of metal, primarily aluminum. It enables the fabrication of aircraft components like wings, fuselages, and fuel tanks, ensuring both strength and lightweight construction. The precise control and reduced distortion offered by resistance seam welding make it an ideal choice for aerospace applications.
Electrical Appliances
Resistance seam welding finds significant applications in the manufacturing of electrical appliances, such as air conditioners, refrigerators, and washing machines. By effectively joining metal components like cabinets, frames, and heat exchangers, it guarantees the longevity and reliability of these appliances. Additionally, the high-speed production capabilities of resistance seam welding make it a cost-effective solution for the electrical appliance industry.
Sheet Metal Fabrication
Various industries, including construction, furniture, and HVAC, rely on resistance seam welding for sheet metal fabrication. From creating ductwork and ventilation systems to assembling metal furniture frames, resistance seam welding provides secure and aesthetically pleasing welds. Its versatility in joining both thick and thin materials makes it a preferred choice in the sheet metal fabrication sector.
These are just a few examples of the diverse applications of resistance seam welding. In the next section, we will explore the specific benefits associated with this welding technique and how it contributes to increased efficiency and cost-effectiveness in manufacturing processes. Stay tuned!
Benefits of Resistance Seam Welding
Resistance seam welding offers a wide array of benefits that make it a preferred welding technique in various industries. Let’s take a closer look at the advantages it provides:
Efficient Production: One of the key benefits of resistance seam welding is its ability to facilitate efficient production processes. The high-speed nature of this technique allows for rapid and continuous welding, significantly reducing assembly time. This increased productivity helps manufacturers meet tight deadlines and produce a higher quantity of products within a shorter timeframe.
Strong and Durable Welds: Resistance seam welding produces strong and durable welds that are able to withstand substantial stress and pressure. This makes it an ideal choice for applications that require structural integrity, such as in the automotive and aerospace industries. The consistent heat generated by resistance seam welding ensures a uniform and reliable bond, resulting in long-lasting and reliable welds.
Reduced Distortion and Heat Affected Zone: Compared to other welding techniques, resistance seam welding minimizes distortion and the heat-affected zone (HAZ) in the welded workpiece. This is crucial in industries, such as aerospace, where components need to maintain their original shape and dimensions. The precise control offered by resistance seam welding ensures minimal warping and deformation, resulting in high-quality and accurate welds.
Cost-Effectiveness: Resistance seam welding is a cost-effective welding solution for many industries. Its high-speed production capabilities and minimal need for additional finishing processes result in reduced labor and operational costs. Furthermore, the strong and leak-proof welds achieved by resistance seam welding eliminate the need for additional reinforcements or sealants, saving both time and money in the manufacturing process.
Environmentally Friendly: Another advantage of resistance seam welding is its environmentally friendly nature. Unlike other welding techniques that may produce harmful fumes or require the use of consumables, resistance seam welding operates using only electricity and pressure. This eliminates the need for additional chemicals or gases, making it a cleaner and safer welding method.
Tips for Successful Resistance Seam Welding
To ensure successful resistance seam welding, it is important to follow certain guidelines and best practices. Here are some tips to help you achieve optimal results:
Proper Preparation for Welding
Before starting the resistance seam welding process, make sure to prepare the workpiece properly. Clean any dirt, oil, or rust from the surfaces to be welded. This will ensure better conductivity and improve the quality of the weld. Additionally, ensure that the workpiece is properly aligned and held securely in the welding fixture or clamps.
Select the Right Materials
Choosing the appropriate materials for resistance seam welding is crucial. Consider factors such as the type of metal, its thickness, and the required strength of the weld. Select electrodes and weld wheels that are compatible with the materials being welded to ensure a successful bond. Using the wrong materials can lead to weak welds or damage to the workpiece.
Optimize Welding Parameters
To achieve the desired results, it is important to optimize the welding parameters. Factors such as current, voltage, weld time, and electrode force should be adjusted according to the specific requirements of the application. Consult the equipment manufacturer’s guidelines and conduct test runs to determine the optimal parameters for your specific welding process.
Monitor and Maintain Equipment
Regularly monitor and maintain the resistance seam welding equipment to ensure it is in optimal condition. This includes checking and replacing worn-out electrodes, cleaning the welding wheel, and ensuring proper cooling and lubrication systems are in place. By keeping the equipment in good working order, you can achieve consistent and high-quality welds.
Embrace Continuous Improvement
As with any welding process, continuous improvement is key. Regularly evaluate your resistance seam welding process, identify areas for improvement, and implement changes accordingly. This could involve refining welding parameters, adopting new technologies, or enhancing operator training. By continuously striving for improvement, you can enhance the efficiency, quality, and productivity of your resistance seam welding operations.
By following these tips, you can increase the success rate of your resistance seam welding projects and optimize the overall welding process. In the next section, we will explore the various applications of resistance seam welding across different industries. Stay tuned to discover the diverse range of uses for this versatile welding technique.
Conclusion and Final Thoughts
The previous blog section provided important tips and best practices for achieving successful resistance seam welding. By following these guidelines, you can ensure proper preparation, select the right materials, optimize welding parameters, monitor and maintain equipment, and embrace continuous improvement. These tips are essential for achieving high-quality welds and optimizing the overall welding process.