Arc welding is an essential process that joins metals together using intense heat, but it comes with its own set of risks. In this article, we will explore the vital topic of arc welding safety and provide you with valuable tips and guidelines to ensure a safe working environment. Whether you are a seasoned welder or just starting out, understanding the potential hazards and knowing how to protect yourself is crucial.
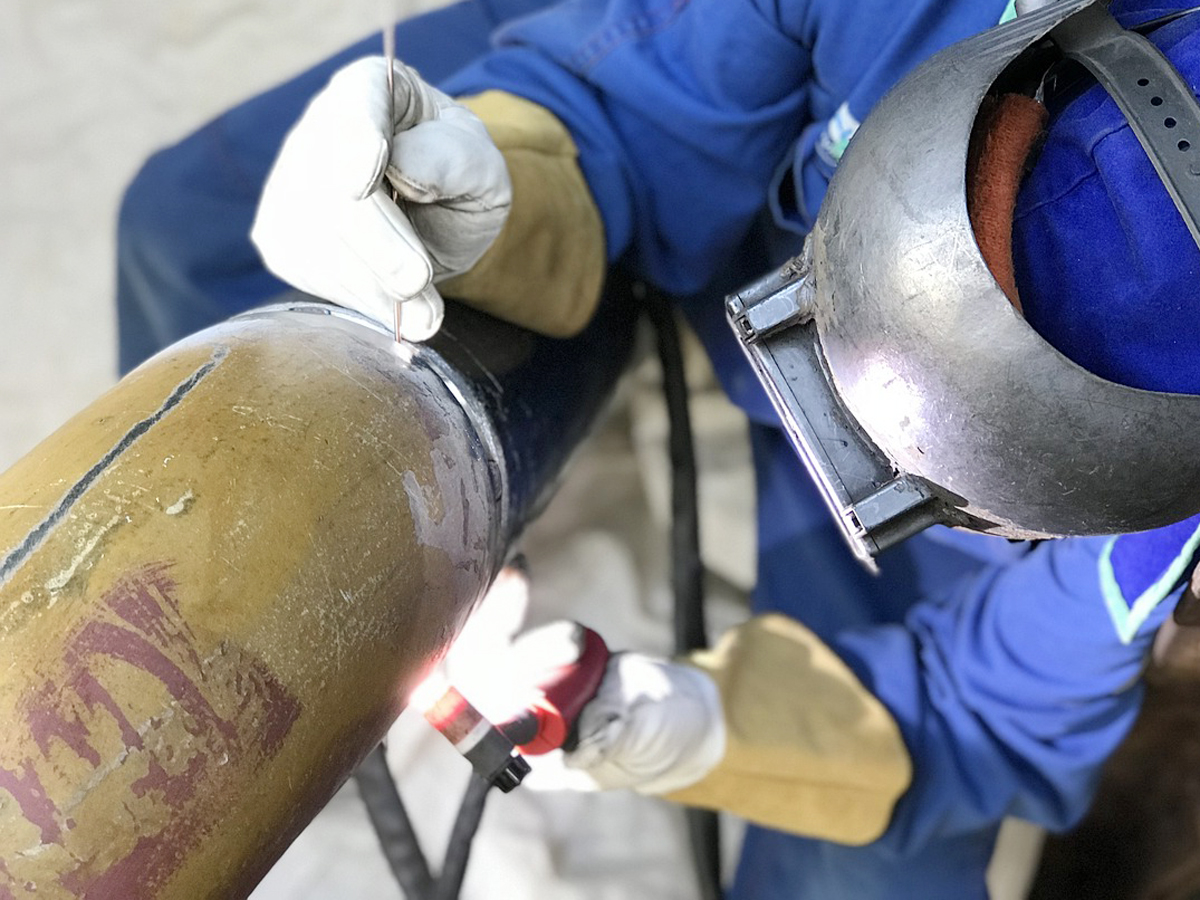
Photo by wyllyston
Importance of Arc Welding Safety
Arc welding safety is of utmost importance for welders as it involves working with high temperatures, electrical currents, and hazardous materials. By prioritizing safety, welders can significantly reduce the risk of accidents and injuries. One of the key aspects of arc welding safety is the use of personal protective equipment (PPE) to shield the body from potential harm.
Common Hazards in Arc Welding
Arc welding poses several hazards that can lead to serious injuries if not properly managed. One of the most significant dangers is the risk of electrical shock. Welders are exposed to high-voltage electricity, and if safety measures are not followed, they can suffer severe shocks. Another common hazard is the intense heat generated during the welding process, which can cause thermal burns. In addition, welders must be cautious of the harmful fumes and gases emitted during welding, which can lead to respiratory problems if inhaled.
Personal Protective Equipment (PPE) for Arc Welding
To ensure maximum safety during arc welding, it is crucial to wear the appropriate personal protective equipment (PPE). The most essential piece of PPE for welders is the welding helmet. A good quality welding helmet with a darkened visor protects the eyes from the intense light and harmful UV radiation produced during arc welding. Welding gloves are also essential to shield the hands from burns and electrical shocks. Additionally, welders should wear flame-resistant clothing, such as a welding jacket and pants, to protect the body from sparks and molten metal splatter.
Preparing the Work Area for Safe Arc Welding
Creating a safe work environment is essential to prevent accidents during arc welding. Before starting any welding operation, it is crucial to ensure that the work area is clean and free from clutter. Remove any flammable materials or objects that could potentially catch fire from nearby. It is also important to have proper ventilation in the workspace to prevent the accumulation of hazardous fumes. Adequate lighting is necessary to ensure visibility and minimize the chances of accidents.
Safe Practices During Arc Welding
Adhering to safe practices while operating the welding equipment is vital to avoid injuries. One of the first things to remember is to always wear the appropriate PPE, including the welding helmet, gloves, and protective clothing. When positioning yourself for welding, ensure that you have a stable and comfortable stance to maintain balance and control. It is important to keep your body and hands away from the welding arc to prevent burns. Never touch the electrode or any metal parts of the welding equipment without proper insulation as they can be electrically charged.
Arc Welding Safety Tips
Here are some additional safety tips to keep in mind while performing arc welding:
- Always inspect the welding equipment before use to ensure it is in proper working condition.
- Use a welding curtain or screen to shield nearby workers or bystanders from the welding arc.
- Avoid welding in damp or wet conditions as it can increase the risk of electrical shock.
- Be aware of your surroundings and the location of flammable materials to prevent fire hazards.
- Take regular breaks during prolonged welding operations to prevent fatigue and maintain focus.
Training and Certification for Arc Welding Safety
Proper training and education are essential for welders to promote a culture of safety in the workplace. It is crucial to undergo comprehensive training programs that cover the basics of arc welding, safety protocols, and emergency procedures. By receiving proper education, welders can develop the necessary skills to identify potential hazards and take appropriate safety measures. Certification programs can also help validate a welder’s competency and ensure adherence to industry standards.
Arc Welding Safety Inspections and Maintenance
Regular inspections and maintenance of welding equipment are crucial to ensure their safe and efficient operation. Welders should regularly check the condition of cables, connectors, and electrodes to identify any signs of damage or wear. Inspecting the welding machine for loose connections and faulty components is also necessary. It is important to follow the manufacturer’s guidelines for maintenance and conduct routine inspections to prevent any potential accidents due to equipment failure.
Prioritizing Arc Welding Safety for a Successful Welding Operation
Arc welding is a valuable technique for joining metals, but it comes with inherent risks. By prioritizing arc welding safety, welders can protect themselves and others from potential hazards. The use of personal protective equipment, creating a safe work environment, and adhering to safe practices are essential for accident prevention. Continuous training, certification, and regular equipment inspections ensure that welders are equipped with the necessary knowledge and tools to carry out welding operations safely. Remember, safety should always be the top priority in any welding operation.
By following the guidelines and tips provided in this article, you can ensure a safe and successful welding operation. Protect yourself, promote a culture of safety, and enjoy the benefits of arc welding without compromising on your well-being. Stay safe and happy welding!