Welcome to our guide to mastering the art of Tig welding galvanized steel. Galvanized steel is a unique material that poses particular challenges when it comes to welding. However, with the right techniques, you can produce high-quality welds on galvanized steel that are strong, durable, and long-lasting.
In this article, we will explore the essential techniques and tips to help you become a master at Tig welding galvanized steel. From safety precautions to troubleshooting, we will cover all aspects of welding this unique material. By the end of this guide, you will have the knowledge and skills necessary to weld galvanized steel like a pro.
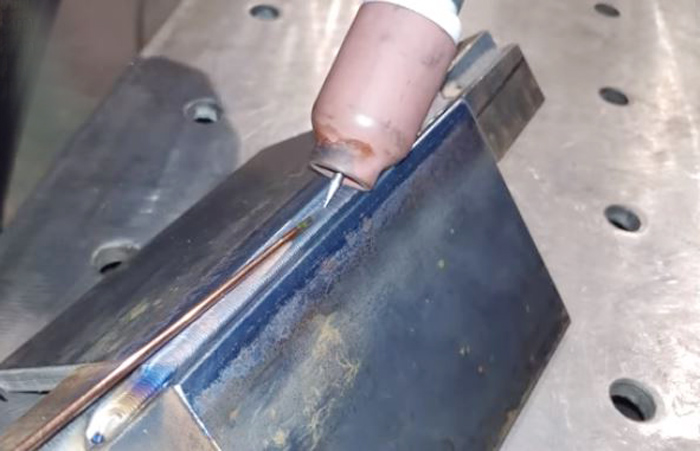
Photos by weldHAGOJIBI on YT
Galvanized Steel and Its Welding Challenges
Galvanized steel is a popular material in various industries due to its durability and corrosion resistance. However, welding galvanized steel presents unique challenges that require proper technique and precautions for successful welds.
What is Galvanized Steel?
Galvanized steel is steel that has been coated with a layer of zinc to protect it from rusting and corrosion. Zinc is chosen due to its ability to form a protective layer that prevents the steel’s exposure to moisture and oxygen, one of the main causes of rust.
Welding Galvanized Steel
Welding galvanized steel requires extra attention due to the potential for zinc fumes and porosity in the weld. Zinc has a low boiling point that can cause it to vaporize and create hazardous fumes. Porosity occurs when air pockets form within the weld due to contamination from the zinc coating.
Galvanized Steel Welding Precautions
Before welding galvanized steel, it is crucial to take the necessary precautions to ensure the safety of the welder and the quality of the weld. Some essential precautions include:
- Welding in a well-ventilated area to minimize exposure to zinc fumes
- Wiping the surface of the galvanized steel with a wire brush or grinder to remove the zinc coating before welding
- Using a respirator or other protective equipment to prevent inhaling zinc fumes
- Using low currents and short arc lengths to avoid excessive heat that can vaporize the zinc coating
TIG Welding Techniques for Galvanized Steel
TIG welding galvanized steel requires specific techniques to ensure a quality weld. In this section, we will discuss the TIG welding process for galvanized steel, the best TIG welding practices, joint design, and weld preparation.
TIG Welding Process for Galvanized Steel
The TIG welding process for galvanized steel is similar to other TIG welding processes. It’s requires some adjustments to ensure a quality weld.
First, you should use a lower amperage setting to avoid burning off the zinc coating or creating excessive fumes. It is also crucial to use a clean tungsten electrode to prevent contamination and ensure a stable arc.
Additionally, you should use a filler metal that matches the base metal’s strength properties and melt temperature. Galvanized steel is prone to cracking due to its high zinc content, so it is essential to maintain a consistent travel speed and avoid overheating the material.
Best Tig Welding Galvanized Steel Practices
To achieve the best Tig welding galvanized steel, it is essential to follow these best practices:
- Clean the surface of the material before welding to ensure good penetration and adhesion.
- Use a low-amperage start to prevent burning through the zinc coating.
- Use a back-purge gas to prevent contamination of the weld.
- Maintain a consistent travel speed and avoid overheating the material.
- Use the correct filler metal and match it to the base metal’s properties.
Joint Design
Joint design is essential when welding galvanized steel. Ensure that the joint is clean and properly fitted before welding to prevent gaps or weak spots.
A butt joint with a single V or U-groove is the most common joint type for galvanized steel. Tack welds should be used to hold the pieces in place before welding to prevent misalignment.
Weld Preparation
Prep work is essential to ensure a quality weld on galvanized steel. Before welding, remove any surface contaminants, such as oil, grease, or dirt, using a wire brush or grinder.
It is also crucial to remove the zinc coating from the edges of the joint and about 1/4 inch back from the joint’s edge to avoid burning off the zinc coating or creating excessive fumes.
Prep Work | Description |
---|---|
Surface Preparation | Clean the surface of the material to ensure good adhesion and penetration. |
Remove Zinc Coating | Remove the zinc coating from the edges of the joint and about 1/4 inch back from the joint’s edge to avoid burning off the zinc coating or creating excessive fumes. |
Joint Preparation | Ensure that the joint is clean and properly fitted before welding. |
Tips and Troubleshooting for Tig Welding Galvanized Steel
Welding galvanized steel requires careful consideration of several factors. Here are some tips and troubleshooting guidelines to help you achieve the best results:
Welding Galvanized Steel Tips
- Thoroughly clean the surface of the galvanized steel before welding to remove any dirt, oil, or zinc oxide.
- Choose welding wire or rod that is specifically designed for galvanized steel.
- When preparing the weld joint, ensure that it is tight, with minimal gaps, to prevent excessive zinc vapor from escaping.
- Use a lower welding current and voltage than you would with uncoated steel to avoid burning off the zinc coating.
- When welding in a confined space, use proper ventilation to prevent inhalation of harmful zinc fumes.
Galvanized Steel Welding Guidelines
Following these guidelines will help you produce quality welds on galvanized steel:
Guideline | Description |
---|---|
Preheat the Steel | Galvanized steel can be more difficult to weld due to its higher thermal conductivity. Preheating the steel can help reduce this difficulty. |
Adjust Your Welding Settings | Adjust your welding settings to suit the thickness of the galvanized steel, as well as the joint design and welding position. |
Use Shorter Arcs | Shorter arcs produce less heat and can help prevent the zinc coating from burning off during welding. |
Tig Welding Galvanized Steel Troubleshooting
Here are some of the most common welding problems encountered with galvanized steel, along with potential solutions:
- Porosity: Small holes or cavities in the welded area.
- Ensure that the surface is clean and free of zinc oxide, oil, or dirt.
- Increasing the welding current can also help burn off any impurities present in the weld pool.
Excessive Spatter: Molten metal that scatters beyond the weld pool.
- Lower the voltage and increase the travel speed to reduce spatter.
- Ensure a tight joint fit-up to prevent any gaps where spatter can accumulate.
Burn-Through: When the welder burns a hole through the metal.
- Reduce the welding current and voltage to prevent overheating.
- Use a smaller diameter electrode or wire to reduce heat input.
Zinc Fumes: Harmful fumes produced during welding that can cause metal fume fever.
- Weld in a well-ventilated area or use proper respiratory protection.
- Avoid welding on galvanized steel coated with chromate, which can produce even more toxic fumes.
By following these tips, guidelines, and troubleshooting advice, you will be well on your way to producing successful welds on galvanized steel. Remember to prioritize safety and take precautions to avoid inhaling harmful zinc fumes.
Conclusion
Mastering the art of Tig welding galvanized steel is a challenging and rewarding endeavor. With the right knowledge, preparation, and practice, you can achieve excellent results with this unique material. Remember to always prioritize safety and take the necessary precautions to avoid health hazards such as exposure to zinc fumes and UV radiation.
By following the techniques and tips outlined in this guide, you will have a solid foundation for Tig welding galvanized steel and be well-equipped to troubleshoot common issues. Don’t be discouraged by setbacks – welding is a skill that takes time and dedication to perfect.
FAQs
What safety precautions should I take when welding galvanized steel?
When welding galvanized steel, it is essential to wear appropriate personal protective equipment, including a welding helmet, gloves, and a respirator. Make sure you work in a well-ventilated area to minimize exposure to zinc fumes.
Can I weld galvanized steel using a regular welding machine?
While it is possible to weld galvanized steel using a regular welding machine, it is recommended to use a Tig welding machine. Tig welding provides better control and precision, allowing for high-quality welds on galvanized steel.
How should I prepare the galvanized steel surface before welding?
Before welding galvanized steel, it is crucial to remove any zinc coating in the welding area. This can be done by grinding or sanding the surface until the shiny zinc layer is eliminated. Proper surface preparation ensures a strong bond between the base metal and the weld.
What should I do if I encounter porosity in the welds?
Porosity, or small gas pockets within the weld, can be a common issue when welding galvanized steel. To minimize porosity, make sure to clean the welding area thoroughly and use the appropriate shielding gas. Adjusting the welding parameters, such as the voltage and wire speed, can also help reduce porosity.
How can I avoid excessive zinc fumes when welding galvanized steel?
Excessive zinc fumes can be hazardous to your health. To minimize exposure, welding in a well-ventilated area is crucial. Additionally, consider using a fume extraction system or positioning yourself upwind from the welding fumes. Using lower welding currents and shorter welding times can also help reduce zinc fume generation.
What joint design works best for welding galvanized steel?
For welding galvanized steel, a butt joint or a lap joint is commonly used. These joint designs provide sufficient contact area for a strong weld. Proper fit-up and alignment of the joint are important to ensure a successful weld.