Ultrasonic spot welding is a widely used technique in various industries, including automotive, electronics, and packaging. This efficient and precise welding method offers numerous benefits, such as high bonding strength, fast production cycle, and minimal heat impact on surrounding materials. However, understanding the intricacies of ultrasonic spot welding and its applications can be complex.
That’s why we have created this ultimate guide to provide you with everything you need to know about this cutting-edge welding technique. Whether you are a professional welder or someone interested in learning about the latest advancements in manufacturing technology, this guide will serve as a comprehensive resource for all your ultrasonic spot welding needs.
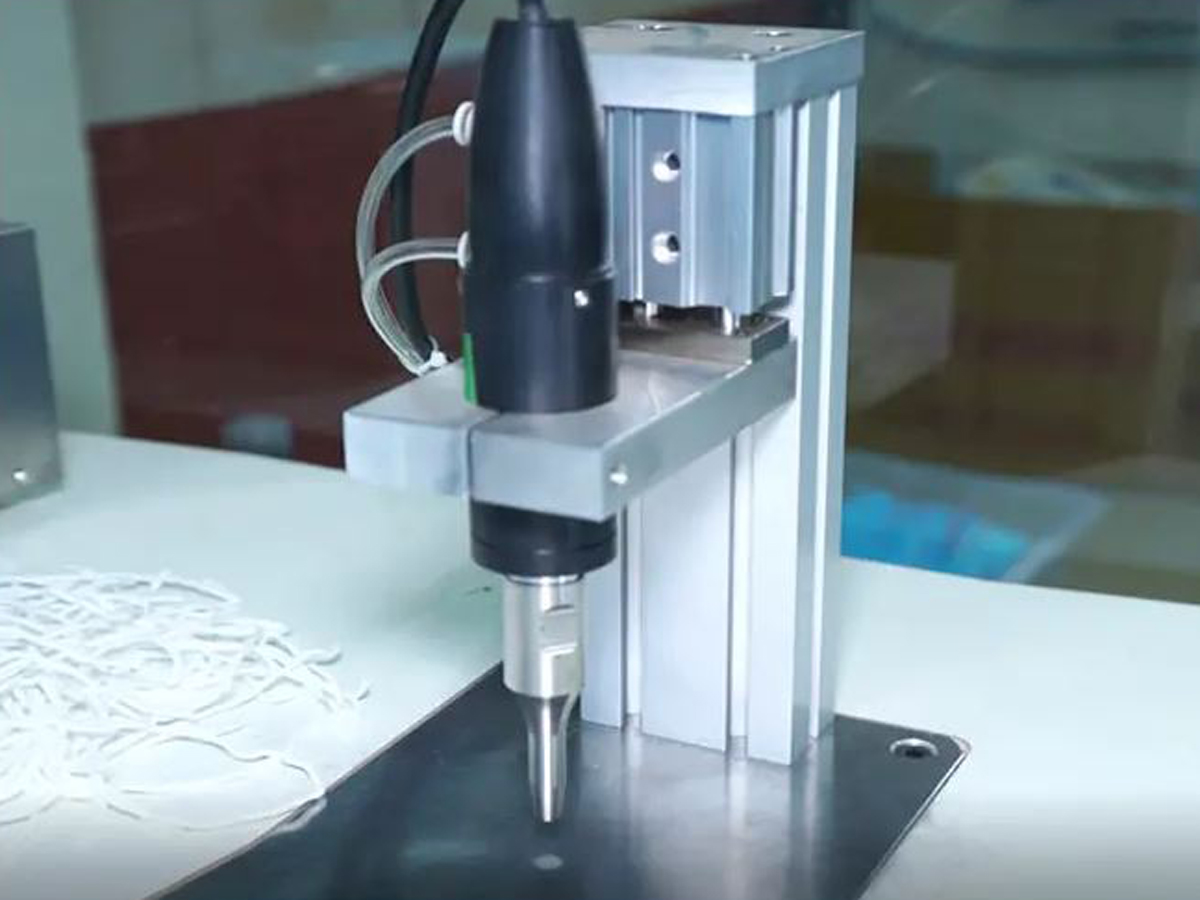
Photos by ilserraglio.com
Understanding the Science Behind Ultrasonic Welding
Understanding the science behind ultrasonic spot welding is essential to grasp the fundamentals of this advanced welding technique. Ultrasonic spot welding is based on the principle of acoustic energy transfer. The process involves applying high-frequency vibrations to the materials being welded, generating friction and heat at the contact point. The heat softens the material, allowing it to bond under pressure. These high-frequency vibrations are typically in the range of 20 kHz to 70 kHz.
During ultrasonic spot welding, the ultrasonic horn applies force to the workpieces, creating a compressive force that facilitates the welding process. The horn also generates the vibrations necessary for the heat generation. Additionally a collet or anvil holds the workpieces in place, ensuring they remain aligned during welding.
Benefits of Ultrasonic Spot Welding
Ultrasonic spot welding offers numerous benefits that make it a highly favorable welding technique in various industries. Firstly, ultrasonic spot welding is a fast and efficient process. With the use of high-frequency vibrations, the welding cycle time is significantly reduced compared to traditional welding methods. This increased speed also leads to higher productivity and cost savings.
Secondly, ultrasonic spot welding provides a strong and reliable weld. The heat generated during the process allows for excellent bond strength, ensuring a durable and long-lasting joint. The precision of the technique also results in minimal distortion and damage to the surrounding areas, making it ideal for delicate or intricate components.
Furthermore, ultrasonic spot welding offers environmental advantages. The process is clean, as it does not require the use of any additional materials such as filler metals or fluxes. It also produces minimal fumes, making it a safer option for the operator and the surrounding environment.
Applications and Industries that Utilize Ultrasonic Spot Welding
Ultrasonic spot welding finds applications in a wide range of industries, thanks to its versatility and effectiveness. Let’s explore some of the most common industries where this welding technique is heavily utilized.
1. Automotive Industry: Ultrasonic spot welding is extensively used in the automotive industry for joining various components such as electrical connections, airbags, fuel filters, and even plastic and metal parts. The strong, reliable welds produced by this technique ensure the durability and safety of these vital components.
2. Electronics Industry: In the electronics industry, ultrasonic spot welding is employed to assemble small electronic devices, microchips, sensors, and other delicate components. The precise and controlled nature of the process makes it perfect for joining these intricate parts without causing any damage.
3. Medical Device Manufacturing: Ultrasonic spot welding is a popular choice in the production of medical devices such as catheters, syringes, and surgical instruments. The clean and hygienic nature of the process, along with its ability to create strong and secure bonds, makes it ideal for these critical applications.
4. Packaging Industry: Ultrasonic spot welding plays a crucial role in the packaging industry, where it is used for sealing plastic films for various products. This technique ensures airtight seals, preventing moisture or contaminants from entering the packaging and preserving the quality of the contents.
These are just a few examples of the industries that benefit from ultrasonic spot welding. The versatility and effectiveness of this welding technique make it a go-to choice for manufacturers across various sectors.
Step-by-Step Guide to Welding
Now that we have explored the wide range of applications and industries that benefit from ultrasonic spot welding, it’s time to dive into the step-by-step process of this welding technique. Whether you are a seasoned professional or new to ultrasonic spot welding, this guide will provide you with valuable insights and expert tips to ensure successful implementation in your manufacturing processes.
Step 1: Preparation
Before beginning the welding process, it is crucial to prepare the materials that need to be joined. This involves ensuring that the surfaces are clean and free from any contaminants or oxides that could interfere with the welding process.
Step 2: Fixture Assembly
Next, assemble the fixture, which holds the materials in place during the welding process. This ensures proper alignment and positioning of the components, resulting in strong and consistent welds.
Step 3: Ultrasonic Generator Setup
Configure the ultrasonic generator settings based on the materials being welded. This includes adjusting the frequency, amplitude, and time parameters to achieve optimal weld strength and integrity.
Step 4: Clamping the Materials
Position the materials to be welded between the ultrasonic horn and anvil, ensuring proper alignment. Apply sufficient clamping pressure to hold the materials securely in place during the welding process.
Step 5: Ultrasonic Activation
Activate the ultrasonic generator, which produces high-frequency vibrations. These vibrations are transferred through the ultrasonic horn to the materials, generating heat at the interface and causing localized melting and bonding.
Step 6: Weld Validation
After the welding cycle is complete, perform a visual inspection or conduct non-destructive testing to verify the quality and integrity of the weld. This step ensures that the desired strength and durability are achieved.
Step 7: Post-Weld Processing
Depending on the application and industry requirements, additional post-weld processes such as cleaning, trimming excess material, or surface finishing may be necessary.
By following these step-by-step instructions, you can effectively utilize ultrasonic spot welding to achieve strong, reliable, and high-quality welds in various manufacturing processes. In the next section, we will discuss the benefits and advantages of ultrasonic spot welding compared to other welding techniques. Stay tuned for an in-depth analysis!
Common Challenges and Troubleshooting Tips for Ultrasonic Spot Welding
While ultrasonic spot welding offers numerous benefits and advantages, like any other welding technique, it also comes with its own set of challenges. Understanding these challenges and having troubleshooting tips at hand can help you overcome any issues that may arise during the welding process.
One common challenge in ultrasonic welding is leakage of energy, resulting in weak welds. This can be caused by improper alignment of the materials or inadequate clamping pressure. To troubleshoot this issue, ensure that the materials are properly aligned and securely clamped. Adjusting the ultrasonic generator settings, such as increasing the amplitude, can help improve the weld strength.
Another challenge is material adhesion or sticking to the ultrasonic horn or anvil. This can occur due to the presence of contaminants or excessive heat. To address this, regularly clean the ultrasonic horn and anvil to remove any buildup and ensure smooth contact between the materials and the horn/anvil during welding.
Furthermore, inconsistent weld quality can be a challenge. This can be attributed to variations in material properties or improper adjustment of the ultrasonic generator parameters. To overcome this challenge, carefully select materials with consistent properties and fine-tune the generator settings based on the specific materials being welded.
Lastly, variation in weld size or shape can occur, especially when joining materials with different thicknesses. To address this, ensure that the materials are properly aligned and that the clamping pressure is evenly distributed. Adjusting the amplitude or time parameters may be required to achieve uniform welds.
By being aware of these common challenges and having troubleshooting strategies in place, you can ensure successful ultrasonic spot welding and achieve high-quality, reliable welds.
Equipment and Tools Required for Successful Welding
To achieve successful ultrasonic spot welding, it is important to have the right equipment and tools. While the specific requirements may vary depending on the application, there are some common elements that are essential for this welding technique.
First and foremost, you will need an ultrasonic welding machine. This machine consists of several components, including an ultrasonic generator, a transducer, a horn, and an anvil. The ultrasonic generator produces the high-frequency vibrations, which are then converted into mechanical vibrations by the transducer. These vibrations are transmitted to the materials being welded through the horn and anvil.
The horn plays a crucial role in ultrasonic spot welding as it focuses the mechanical vibrations onto the joint area, causing the materials to bond together. It is important to select a horn that is suitable for your specific application, taking into account factors such as material type, thickness, and desired weld strength.
In addition to the welding machine, you will also need proper fixtures and clamping devices to hold the materials securely in place during the welding process. These fixtures help ensure proper alignment and consistent contact between the materials and the horn/anvil, resulting in high-quality welds. It is important to use the appropriate tooling for ultrasonic spot welding. This may include specially designed tips or inserts that are compatible with your chosen horn and materials. Using the right tooling can help improve the efficiency and effectiveness of the welding process.
Lastly, it is crucial to have a reliable power source to operate the ultrasonic spot welding machine. Ensure that the power source meets the requirements specified by the manufacturer and that it is capable of providing a consistent and stable supply of electricity.
Industry Standards and Regulations for Ultrasonic Spot Welding
When it comes to any welding technique, including ultrasonic spot welding, adherence to industry standards and regulations is crucial. These standards and regulations ensure the safety of workers and the quality of the finished welds. One of the most important standards to consider is the American Welding Society (AWS) D17.1 Specification for Fusion Welding for Aerospace Applications. This specification provides guidelines on the techniques, procedures, and materials used in aerospace applications, including ultrasonic spot welding.
Another key standard is the ISO 17664:2017 Health and safety in welding and allied processes – Sampling of airborne particles and gases in the operator’s breathing zone. This standard outlines the requirements for monitoring and assessing the air quality during welding processes, including ultrasonic spot welding, to protect the health and well-being of operators.
Additionally, it is important to be familiar with any specific industry regulations that may apply to your particular application. For example, the medical device industry has its own set of regulations, such as the FDA’s Quality System Regulation (21 CFR Part 820), which sets forth requirements for the design, manufacture, and labeling of medical devices.
By following these industry standards and regulations, you ensure the integrity and safety of your welding operations.
Advancements and Future Trends in Ultrasonic Spot Welding
Ultrasonic spot welding has come a long way since its inception, and there have been significant advancements in both technology and techniques. These advancements have not only improved the efficiency and effectiveness of ultrasonic welding but have also opened up new possibilities for its applications. One notable advancement is the development of advanced control systems. These systems utilize real-time data monitoring, feedback control, and automation to optimize the welding process. This not only improves the consistency and reliability of the welds but also reduces the need for manual intervention, resulting in increased productivity.
Another significant development is the integration of robotics with ultrasonic spot welding. Robotic systems offer precise control and repeatability, making them ideal for high-volume production and complex assemblies. With the ability to handle varying part geometries and perform multiple welds simultaneously, robotic ultrasonic spot welding is revolutionizing industries such as automotive, electronics, and medical devices.
As technology continues to evolve, ultrasonic welding is expected to witness further advancements. This includes improvements in equipment design, such as the miniaturization of transducers and advancements in power supply technology.
There is also ongoing research on developing new materials, such as dissimilar materials, that can be successfully welded using ultrasonic spot welding. Finally, ultrasonic spot welding has come a long way and is constantly evolving. Keeping up with the latest advancements and future trends in this field will enable you to stay ahead of the competition and maximize the benefits of this versatile welding technique.
Advantages of Ultrasonic Spot Welding for Industrial Applications
Ultrasonic spot welding has proven to be a highly advantageous welding technique for various industrial applications. Its unique capabilities and advancements make it a preferred choice for industries ranging from automotive to electronics and medical devices. One major advantage of ultrasonic spot welding is its ability to join dissimilar materials. With the right parameters and equipment, it is possible to weld materials that traditionally cannot be joined through other welding methods. This opens up a world of possibilities for designing and producing complex assemblies that require different materials for different functionalities.
Ultrasonic spot welding offers exceptional precision and reliability. The advanced control systems and integration of robotics ensure consistent weld quality across high-volume production. This level of control also minimizes the risk of human error and eliminates the need for extensive post-weld inspections, saving both time and resources. Ultrasonic welding is a non-destructive welding technique. It does not distort or damage the surrounding areas of the weld, making it ideal for delicate components and assemblies. This allows for the production of high-quality, aesthetically pleasing products that meet stringent industry standards.
Conclusion
Ultrasonic spot welding is an invaluable welding technique for industrial applications. Its advancements in technology, such as advanced control systems and robotic integration, enhance efficiency, productivity, and weld quality. With the ability to join dissimilar materials and provide non-destructive welds, ultrasonic spot welding is a versatile solution that should be considered for any industrial welding needs.