Welcome to our comprehensive guide on dual shield flux core welding, where we will explore the crucial aspects of welding process, settings and gas usage. Dual shield flux core welding involves using a shielding gas to protect the weld from atmospheric contamination, resulting in superior weld quality. Whether you are a beginner or an experienced welder, this guide will equip you with the necessary knowledge to optimize your welding settings and gas usage for exceptional results.
Before diving into the settings and gas usage, it’s important to understand the basics of dual shield flux core welding. This includes the welding parameters and techniques used in the process. In the following section, we will explore the fundamental principles of dual shield flux core welding to lay a solid foundation for the rest of the guide.
So let’s get started and dive into the world of dual shield flux core welding, where we’ll show you everything you need to know about the settings and gas usage. Read on to learn how to achieve the best results with dual shield flux core welding.
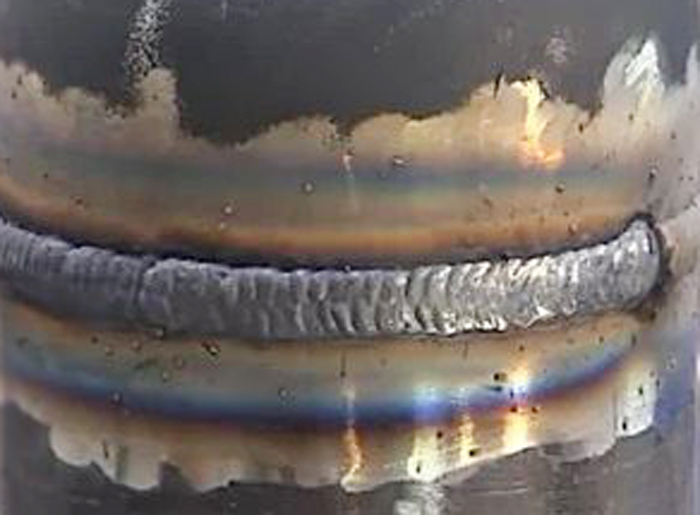
Photos by weldingtipsandtricks
The Process of Dual Shield Flux Core Welding
If you are new to dual shield flux core welding, it’s essential to understand the fundamental principles of the welding process. Proper knowledge of welding parameters and technique will help you achieve the desired weld quality.
Dual shield flux core welding is a variation of flux core welding, where a tubular electrode filled with flux is used as a consumable electrode. The difference is that dual shield flux core welding uses an additional shielding gas to protect the weld from contamination.
The welding parameters involved in dual shield flux core welding include voltage, amperage, and wire feed speed. These parameters determine the heat input and the amount of welding wire deposited into the weld. Properly adjusting these parameters is crucial for achieving an optimal balance between penetration and deposition rate.
Dual Shield Flux Core Welding Technique
The welding technique used in dual shield flux core welding is similar to other types of welding. Proper joint preparation and fit-up are essential for achieving a successful weld. The welding torch should be held at the correct angle and distance from the workpiece. The travel speed should be consistent to ensure that the weld bead is formed evenly.
One key difference with dual shield flux core welding is the need for an additional shielding gas. The gas flows through the welding gun and around the weld pool to protect it from atmospheric contamination. The correct gas flow rate and coverage are crucial for ensuring that the weld is adequately protected.
Welding Parameters and Technique: Key Takeaways
- Understand the fundamental principles of dual shield flux core welding.
- Adjust the welding parameters, including voltage, amperage, and wire feed speed, to achieve optimal results.
- Follow proper welding techniques, including joint preparation, torch angle, and travel speed.
- Ensure proper gas flow rate and coverage to protect the weld from contamination.
Benefits of Dual Shield Flux Core Welding
Dual shield flux core welding offers several benefits over other welding methods, particularly due to the effectiveness of the gas shielding system. Let’s take a closer look at some of the advantages:
- Better penetration: The dual shield welding process produces deeper penetration and stronger welds compared to other processes, thanks to the combination of two shielding methods: the flux core and the gas shielding system.
- Reduced spatter: Dual shield welding reduces spatter and slag, which means less time spent cleaning up spatter and slag, leading to increased productivity.
- Higher deposition rates: The higher deposition rates of dual shield welding mean that more weld metal is deposited in less time, resulting in shorter welding times and reduced labor costs.
- Improved weld quality: The gas shielding system in dual shield welding helps to protect the weld from oxidation and other atmospheric contaminants, resulting in higher quality welds with fewer defects.
- Applicable to a wide range of materials: Dual shield flux core welding can be used on various materials, such as carbon steel, stainless steel, and high-strength low-alloy steel.
Overall, the dual shield welding process with the gas shielding system is a versatile and effective welding method that offers superior weld quality and productivity.
Selecting the Right Gas for Dual Shield Flux Core Welding
Choosing the appropriate gas for dual shield flux core welding is critical in achieving optimal results. The gas shielding system is an essential component of the welding process, and selecting the right gas can significantly impact the quality of your weld.
Types of Dual Shield Welding Gas
There are various types of gas used in dual shield flux core welding, and each has different properties and applications. Some of the most commonly used gases include:
Gas | Shielding Properties | Typical Applications |
---|---|---|
CO2 | Excellent penetration | General fabrication, structural steel |
Ar/CO2 Blend | Improved arc stability and reduced spatter | Automotive, heavy equipment |
Ar/O2 Blend | Improved weld quality and reduced porosity | Pressure vessels, pipe welding |
When selecting the gas for your dual shield flux core welding, consider the material you will be welding, the welding conditions, and the desired weld quality.
Gas Shielding System
The gas shielding system in dual shield flux core welding helps protect the weld from atmospheric contamination and oxidation. It also helps to stabilize the arc and enhance the penetration. The gas flow rate and coverage are critical elements in the shielding system and should be monitored closely.
To ensure proper gas usage, follow these guidelines:
- Maintain a consistent gas flow rate
- Ensure complete coverage of the weld with the gas
- Keep the gas nozzle close to the weld for maximum shielding effect
- Use the appropriate gas flow rate and coverage for the welding parameters
By selecting the right gas and following proper gas usage practices, you can achieve exceptional welding results and enhance your welding skills.
Dual Shield Flux Core Welding Setting
Properly setting up your welding equipment is crucial for achieving consistent and high-quality welds. Here’s a step-by-step guide on configuring your welding settings:
- Ensure your welding machine is set to DC electrode positive (DCEP) polarity.
- Set the voltage to the recommended level for the thickness of the material being welded. Refer to the manufacturer’s recommendations for the specific wire and gas combination you are using.
- Adjust the amperage to the recommended level for the wire diameter and plate thickness. This will typically fall within a range provided by the manufacturer.
- Feeder speed is determined by the wire diameter and the amperage. Adjust the feeder speed until the wire is feeding at the recommended rate for the amperage being used.
- When using dual shield flux core wire, it’s important to use the correct drive rolls for the wire being used. Check the manufacturer’s recommendations for the appropriate drive rolls.
Once your welding settings are configured, it’s important to ensure proper gas usage:
- Check the gas flow regulator to ensure it’s set to the recommended gas flow rate. This should be provided by the manufacturer.
- Monitor the gas flow during welding to ensure it’s consistent. A flow meter can help you measure the gas flow rate accurately.
- Keep the welding torch at a 90-degree angle to the workpiece to ensure proper gas coverage.
- When welding outside or in windy conditions, consider using a windscreen or other barrier to protect the weld from contamination.
Adjusting Welding Parameters
Once you have set up your welding equipment and selected the appropriate gas for dual shield flux core welding, it’s time to start adjusting your welding parameters. Welding parameters are the various settings that control the welding process, including voltage, current, wire feed speed, and travel speed. One critical parameter to consider is the voltage. Increasing the voltage can increase the heat input, resulting in deeper penetration. However, too much voltage can cause excessive spatter and poor bead appearance. Lowering the voltage, on the other hand, can decrease penetration and increase the risk of incomplete fusion.
Another essential parameter to optimize is the wire feed speed. Increasing the wire feed speed can increase the deposition rate, but it can also lead to excessive spatter. Lowering the wire feed speed can improve control and reduce spatter, but it may also result in lower productivity.
Travel speed is also an important parameter to consider. A slower travel speed can produce deeper penetration, but it can also increase the risk of burn-through. A faster travel speed can increase productivity, but it may also result in a weaker joint and insufficient penetration. It’s essential to remember that each parameter is interconnected and affects the others. Therefore, it’s crucial to find the right balance between the different parameters to achieve optimal welding results.
Tips for Adjusting Welding Parameters
- Start by setting the parameters at the recommended levels and adjust them gradually as needed
- Keep track of the adjustments made, including the parameter values and the resulting weld quality
- Test welds on scrap material to assess the impact of the parameter changes
- Monitor the welding parameters continuously during the welding process to ensure consistency
- Consider using advanced techniques such as pulse welding to achieve increased control and precision
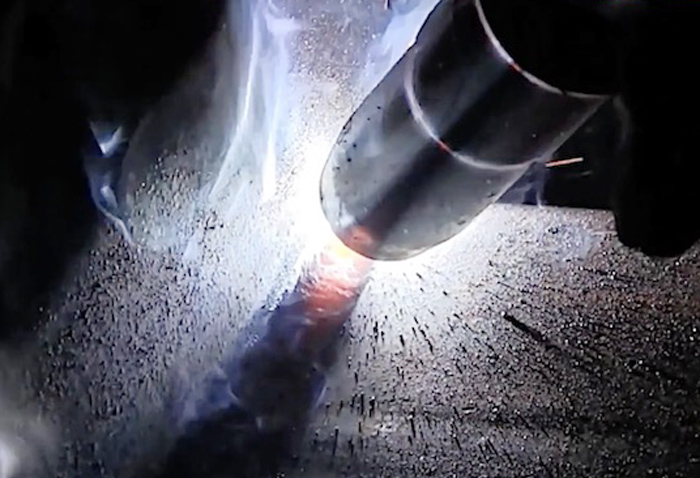
Photos by weldingtipsandtricks
Dual Shield Flux Core Welding Gas Flow Rate and Coverage
The gas shielding system is a crucial aspect of dual shield flux core welding. Proper gas usage is essential for achieving optimal weld quality and preventing atmospheric contamination. Maintaining the appropriate gas flow rate and coverage ensures sufficient protection for the weld and enhances welding efficiency. Here are some guidelines on how to set and adjust the gas flow rate and coverage for dual shield flux core welding:
- Consult the welding specifications for recommended gas flow rates and coverage.
- Use a flowmeter to measure the gas flow rate accurately.
- Adjust the gas flow rate based on the diameter of the welding wire and the welding amperage. As a rule of thumb, the gas flow rate should be approximately 15-25 CFH (cubic feet per hour) for a 0.035-inch diameter wire and 25-40 CFH for a 0.045-inch diameter wire. Higher amperages require higher gas flow rates.
- Ensure that the gas coverage extends at least 1 inch beyond the weld puddle on each side. This ensures optimal protection of the molten metal from atmospheric gases.
When adjusting the gas flow rate and coverage, it’s important to monitor the sound of the arc. Proper gas flow will produce a steady, smooth hissing sound. If the sound becomes erratic or discontinuous, it may indicate insufficient gas flow or coverage.
Common Gas Shielding Systems for Dual Shield Flux Core Welding | Gas Type | Advantages |
---|---|---|
GMAW (Gas Metal Arc Welding) Shielding System | Argon/CO2 Mixtures | Enhanced weld penetration, reduced spatter and fumes |
FCAW (Flux-Cored Arc Welding) Shielding System | CO2 | Cost-effective, readily available |
SAW (Submerged Arc Welding) Shielding System | Granular Flux | Provides high deposition rates, excellent weld quality |
The above table provides a summary of common gas shielding systems used in dual shield flux core welding. Selecting the appropriate gas type for your welding needs is key for achieving optimal welding results. Consult with your gas supplier or welding equipment manufacturer for further guidance on selecting the right gas shielding system for your welding operation.
Troubleshooting Welding Issues
Despite the best efforts and attention to detail, welding issues can still occur when performing dual shield flux core welding. By understanding the common problems that may arise, you can take proactive steps to troubleshoot and resolve them.
Problem 1: Porosity in the Weld
Possible Cause: Porosity can occur when the gas shielding system is not functioning correctly, resulting in atmospheric contamination of the weld pool.
Solution: Check the gas flow rate and coverage, ensuring they are within the recommended range. Adjust as necessary to achieve adequate shielding. Additionally, inspect the gas delivery system for leaks or other malfunctions.
Problem 2: Burn-Through on Thin Materials
Possible Cause: Burn-through can occur when the welding parameters are set too high for thin materials, resulting in excessive heat input and penetration.
Solution: Adjust the welding parameters, such as the voltage and wire speed, to reduce the heat input and penetration. Consider using a thinner wire and reducing the amperage to prevent burn-through.
Problem 3: Inconsistent Weld Bead Shape
Possible Cause: Inconsistent weld bead shape can occur when the welding technique is not consistent, or the welding parameters are not adjusted correctly.
Solution: Maintain a consistent welding technique, ensuring the gun angle and travel speed remain constant throughout the weld. Adjust the welding parameters to achieve the desired bead shape, such as increasing the voltage for a wider bead.
Problem 3: Excessive Spatter
Possible Cause: Excessive spatter can occur when the welding parameters are not optimized for the wire diameter or when contaminants are present on the workpiece.
Solution: Adjust the welding parameters, such as the voltage, wire speed, and amperage, to achieve the appropriate spatter level for the wire diameter. Clean the workpiece thoroughly to remove any contaminants before welding.
Problem 4: Inconsistent Arc Stability
Possible Cause: Inconsistent arc stability can occur when the welding parameters are unstable or when the welding gun is not positioned correctly.
Solution: Adjust the welding parameters to achieve stable arc conditions, such as reducing the wire feed speed or increasing the voltage. Check the welding gun position and maintain a consistent distance from the workpiece throughout the weld.
By addressing these common welding issues, you can ensure a more productive and successful dual shield flux core welding operation. Remember to always follow proper safety precautions and consult with welding experts when necessary.
Safety Precautions for Dual Shield Flux Core Welding
When it comes to dual shield flux core welding, safety is paramount. As with any welding process, there are potential hazards that must be considered and addressed before beginning work. In this section, we will outline important safety precautions to keep in mind when handling gases and welding equipment.
Handling Gases
The gas shielding system is a crucial component of dual shield flux core welding, but the gases themselves can pose a threat if not handled properly. Here are some tips to keep in mind:
- Only use gases that are recommended for dual shield flux core welding.
- Store gases in a well-ventilated area away from sources of heat and flames.
- Always wear appropriate personal protective equipment (PPE) when working with gases, including goggles and gloves.
- Never tamper with gas cylinders or valves.
Protecting Yourself
Welding equipment can also pose a safety risk if not handled properly. Here are some precautions to take when working with dual shield flux core welding equipment:
- Wear appropriate PPE, including welding helmets, gloves, and protective clothing.
- Ensure that your work area is well-ventilated to prevent exposure to fumes and gases.
- Inspect your equipment regularly to ensure that it is in good working condition.
- Be aware of your surroundings and the location of other workers to avoid accidental collisions.
By following these safety precautions, you can protect yourself and others while achieving exceptional welding results with dual shield flux core welding.
Dual Shield Flux Core Welding Tips and Techniques
Looking to take your dual shield welding process to the next level? Here are some advanced tips and techniques that can help improve your welding technique:
1. Perfect Your Torch Angle
The torch angle is critical for maintaining proper penetration and control over the weld pool. A torch angle between 5-15 degrees is ideal for dual shield flux core welding. Also, make sure to keep the travel speed steady to avoid any unevenness in the weld.
2. Choose the Right Wire Size
The wire size used for dual shield flux core welding can significantly impact the quality of the weld. A thicker wire diameter can provide a higher deposition rate, while a thinner wire is better suited for welding thinner materials. Make sure to choose the right wire size based on the material thickness and welding parameters.
3. Use Backing Bars
Backing bars can help prevent warping and distortion in the welding material. Using a backing bar can also enhance the overall appearance of the weld. When using a backing bar, make sure to position it correctly and ensure adequate gas flow around the weld joint.
4. Weld with Two Hands
Welding with two hands can provide better control over the welding process, allowing for smoother and more precise welds. Use one hand to hold the torch and the other hand to steady the welding gun, keeping it in the right position to maintain the appropriate angle.
5. Maintain Appropriate Contact-Tip-to-Work Distance
The contact-tip-to-work distance plays an essential role in the quality of the weld. Maintaining the appropriate distance can help ensure a stable arc and proper penetration. Generally, a distance of ⅜ inch to ½ inch is recommended for dual shield flux core welding.
6. Use a Push Technique
The push technique is ideal for dual shield flux core welding as it keeps the shielding gas in front of the weld pool, effectively shielding the molten metal from the atmosphere. Additionally, the push technique can provide better control over the welding speed and the overall quality of the weld.
Final Thoughts
After reading this comprehensive guide, you are now equipped with the knowledge and skills to master the dual shield flux core welding process. With the right settings and gas usage, you can achieve superior weld quality and take your welding skills to the next level.
Remember, understanding the fundamental principles of dual shield flux core welding is crucial to achieving optimal results. Properly setting up your welding equipment, adjusting welding parameters, and maintaining the appropriate gas flow rate and coverage are also key to success.
Safety First
It’s essential to always prioritize safety when working with the dual shield flux core welding process. Follow the recommended safety precautions, including guidelines for handling gases and protecting yourself from potential hazards.
Keep Improving
Finally, don’t be afraid to experiment with advanced tips and techniques to improve your welding efficiency, precision, and overall quality of work. With dedication, practice, and a willingness to learn, you can become a master of dual shield flux core welding.
Thank you for taking the time to read this guide, and best of luck on your welding journey!
FAQ
What is dual shield flux core welding?
Dual shield flux core welding is a welding process that uses a flux-cored electrode and a combination of shielding gases to protect the weld from oxidation and contamination. It is commonly used in heavy fabrication and structural welding applications.
What are the essential settings for dual shield flux core welding?
The essential settings for dual shield flux core welding include voltage, wire feed speed, and travel speed. These settings can vary depending on the specific welding application and the thickness of the materials being welded.
What gases are used in the gas shielding system for dual shield flux core welding?
The most commonly used gases in the gas shielding system for dual shield flux core welding are carbon dioxide (CO2) and argon (Ar). These gases help create a stable arc and protect the weld from atmospheric contamination.
How do I select the right gas for dual shield flux core welding?
Selecting the right gas for dual shield flux core welding depends on factors such as the type of materials being welded and the desired weld quality. It is important to consult with welding professionals or refer to welding guidelines to choose the appropriate gas for your specific welding needs.
How do I properly set up my welding equipment for dual shield flux core welding?
Properly setting up your welding equipment for dual shield flux core welding involves ensuring the correct voltage, wire feed speed, and gas flow rate. It is recommended to follow the manufacturer’s instructions and consult welding experts for guidance on equipment setup.
What welding parameters can be adjusted in dual shield flux core welding?
In dual shield flux core welding, the welding parameters that can be adjusted include voltage, wire feed speed, and travel speed. Adjusting these parameters allows welders to optimize the welding process and achieve the desired weld quality.
Why is gas flow rate and coverage important in dual shield flux core welding?
Gas flow rate and coverage are important in dual shield flux core welding because they ensure effective shielding of the weld. Proper gas flow rate and coverage help prevent oxidation and contamination, leading to improved weld quality.
What are some common welding issues in dual shield flux core welding?
Some common welding issues in dual shield flux core welding include excessive spatter, improper penetration, and porosity in the weld. These issues can be caused by various factors, such as incorrect welding parameters or improper gas usage.
What safety precautions should I follow when performing dual shield flux core welding?
When performing dual shield flux core welding, it is important to follow safety precautions such as wearing appropriate personal protective equipment (PPE), ensuring proper ventilation in the workspace, and handling gases safely. It is also crucial to be aware of potential hazards and take necessary precautions to prevent accidents.
What are some advanced tips and techniques for dual shield flux core welding?
Some advanced tips and techniques for dual shield flux core welding include adjusting welding parameters based on the specific welding application, using different techniques to control heat input, and practicing proper weld joint preparation. These strategies can help welders achieve higher welding efficiency and precision.