Are you struggling with welding thin sheet metal? Look no further! In this article, we’ll walk you through the ins and outs of MIG welding thin sheet metal, helping you achieve professional-looking results every time. Whether you’re a newbie or an experienced welder, we’ve got you covered with the latest tips and techniques.
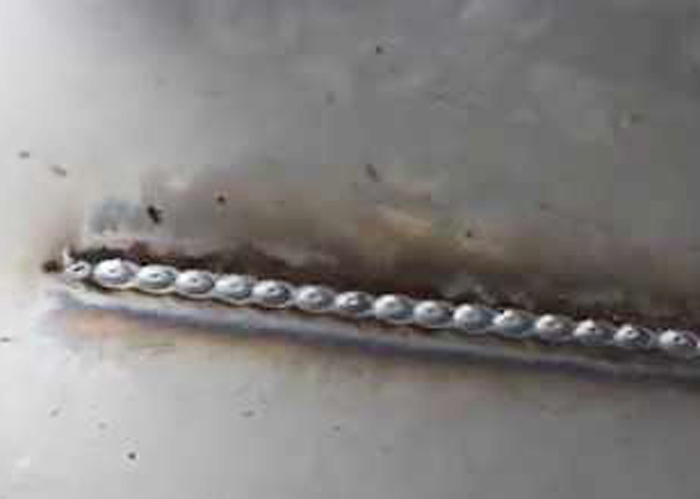
Photos by yt/huayuanwelder9639
Understanding the Thin Sheet Metal
Thin sheet metal refers to metal gauges typically ranging from 30 to 19 gauge, with 30 being the thinnest. It is commonly used in various industries, including automotive, HVAC, and crafts. Understanding the properties of thin sheet metal is crucial for successful MIG welding.
Thin sheet metal is more susceptible to warping and distortion due to its low heat capacity. It requires careful handling to prevent burn-through or excessive heat input. Additionally, thin metal sheets are prone to oil, rust, and contaminants, which can affect the quality of your welds.
To ensure a clean and strong weld, it’s important to properly prepare the thin sheet metal before welding. Cleaning the surface, removing any rust or oil, and ensuring proper fit-up are essential steps in the preparation process.
Benefits and challenges of MIG welding thin sheet metal
MIG welding is a popular choice for joining thin sheet metal due to its versatility and ease of use. It offers several benefits that make it suitable for welding thin gauges.
One of the main advantages of MIG welding is its ability to provide a continuous and stable arc, resulting in smooth and consistent welds. The wire electrode melts and fuses with the base metal, creating a strong and reliable bond. MIG welding also allows for higher travel speeds, increasing productivity.
However, MIG welding thin sheet metal does come with its challenges. The heat input must be carefully controlled to prevent warping or burn-through. Thin metal sheets are highly sensitive to heat, so finding the right balance between penetration and heat input is crucial.
Preparing the thin sheet metal for welding
Proper preparation of the thin sheet metal is essential for achieving high-quality welds. Here are some steps to follow when preparing the metal for MIG welding:
- Clean the surface: Remove any rust, oil, or contaminants from the metal surface using a wire brush or sandpaper. This will ensure proper adhesion and prevent defects in the weld.
- Fit-up and alignment: Ensure that the pieces to be welded are properly aligned and fit together tightly. Proper fit-up helps in achieving good penetration and reduces the risk of burn-through.
- Use clamps or magnets: To hold the metal pieces in place during welding, use clamps or magnets. This will prevent any movement or distortion during the welding process.
Remember, a clean and well-prepared metal surface is the foundation for a successful weld. Take your time to prepare the metal properly before starting the welding process.
Selecting the right MIG welding machine and settings
Choosing the right MIG welding machine and settings is crucial for achieving optimal results when welding thin sheet metal. Here are some factors to consider:
- Welding machine selection: Look for a MIG welding machine that offers precise control over voltage and wire feed speed. A machine with a lower amperage range and finer adjustments will give you better control over heat input.
- Wire selection: For thin sheet metal, choose a smaller diameter wire, such as 0.023 or 0.030 inches. Thinner wire allows for lower heat input and better control.
- Shielding gas: Depending on the type of metal you are welding, select the appropriate shielding gas. For mild steel, a mix of 75% argon and 25% carbon dioxide (CO2) is commonly used. This gas mixture provides good arc stability and penetration.
- Wire feed speed and voltage settings: Start with the manufacturer’s recommended settings for the specific wire diameter and metal thickness. Adjust the wire feed speed and voltage as needed to achieve a stable arc and proper penetration.
Remember to test your settings on scrap metal before welding on the actual workpiece. Fine-tune the settings until you achieve the desired results.
Techniques for MIG welding thin sheet metal
MIG welding thin sheet metal requires specific techniques to ensure a successful weld. Here are some tips to help you achieve high-quality welds:
- Maintain a short arc length: Keep the arc length as short as possible without touching the metal. A shorter arc length helps to minimize heat input and reduce the risk of burn-through.
- Use a push technique: When MIG welding thin sheet metal, it’s generally recommended to use a push technique. This means pushing the gun away from the weld pool while maintaining a consistent travel speed. Pushing the gun helps to control the heat and prevents the wire from digging into the metal.
- Stitch welding: Instead of continuously welding along the entire length, consider using a stitch welding technique. This involves welding short sections, pausing, and then moving to the next section. Stitch welding helps to control heat buildup and reduce the risk of distortion.
- Tack welding: Use tack welds to hold the workpieces in place before making the final welds. Tack welds provide stability and prevent movement during the welding process.
By practicing these techniques and adjusting your settings accordingly, you’ll be able to achieve strong and aesthetically pleasing welds on thin sheet metal.
Common mistakes to avoid when MIG welding thin sheet metal
Even experienced welders can make mistakes when working with thin sheet metal. Here are some common mistakes to avoid:
- Excessive heat input: Applying too much heat to thin sheet metal can lead to warping, burn-through, or distortion. Always start with low heat settings and gradually increase if needed.
- Poor fit-up: Inadequate fit-up can result in poor weld quality and increased heat input. Ensure that the metal pieces fit together tightly, and use clamps or magnets to hold them in place.
- Insufficient cleaning: Failing to properly clean the metal surface can lead to poor adhesion and weld defects. Take the time to remove any rust, oil, or contaminants before welding.
- Inconsistent travel speed: Maintaining a consistent travel speed is important for achieving uniform welds. Avoid speeding up or slowing down during the welding process, as it can affect the heat input.
By being aware of these common mistakes and taking the necessary precautions, you can avoid costly errors and achieve excellent results when MIG welding thin sheet metal.
Safety precautions for MIG welding thin sheet metal
Safety should always be a top priority when MIG welding, especially with thin sheet metal. Here are some safety precautions to follow:
- Wear protective gear: Always wear a welding helmet, safety glasses, and welding gloves to protect yourself from sparks, UV radiation, and heat.
- Adequate ventilation: Ensure that you’re working in a well-ventilated area or use an exhaust system to remove fumes and gases produced during the welding process.
- Fire prevention: Keep a fire extinguisher nearby and clear any flammable materials from the welding area. Sparks and hot metal can easily ignite combustible materials.
- Grounding: Properly ground the welding machine and workpiece to prevent electrical shocks and ensure safe operation.
Remember, safety should never be compromised. Take the necessary precautions to protect yourself and those around you while MIG welding thin sheet metal.
Troubleshooting common issues in MIG welding thin sheet metal
Even with proper preparation and technique, issues can arise during MIG welding thin sheet metal. Here are some common problems and troubleshooting tips:
- Burn-through: If you’re experiencing burn-through, try reducing the heat input by decreasing the voltage or wire feed speed. You can also use a lower amperage setting or switch to a thinner wire.
- Warping: To minimize warping, use tack welds to hold the workpieces in place and distribute the heat more evenly. Consider stitch welding or alternating between welds to control heat buildup.
- Porosity: Porosity, often seen as small holes in the weld, can be caused by contaminants or insufficient shielding gas coverage. Ensure that the metal surface is clean and the shielding gas flow is adequate.
- Lack of fusion: Insufficient fusion can occur when the wire doesn’t penetrate the base metal properly. Increase the voltage or wire feed speed to achieve better penetration.
Remember, troubleshooting requires patience and experimentation. If you encounter any issues, don’t hesitate to make adjustments and try different techniques until you achieve the desired results.
Conclusion and final tips for successful MIG welding of thin sheet metal
MIG welding thin sheet metal can be challenging, but with the right techniques and precautions, you can achieve professional-looking results. Here are some final tips to keep in mind:
- Practice on scrap metal: Before working on your project, practice your welding techniques on scrap metal of similar thickness. This will allow you to fine-tune your settings and gain confidence.
- Take your time: Welding thin sheet metal requires patience and precision. Don’t rush the process and ensure that you’re maintaining a consistent travel speed and arc length.
- Learn from experience: Welding is a skill that improves with practice. Learn from each weld and take note of what works and what doesn’t. Over time, you’ll become more proficient in MIG welding thin sheet metal.
By following these tips, you’ll be well on your way to mastering the art of MIG welding thin sheet metal. With practice, proper technique, and attention to detail, you’ll achieve strong and beautiful welds on thin gauges. Happy welding!