Are you looking to learn the art of MIG welding thick steel? Look no further! In this informative article, we will guide you through the process of welding thick steel using the MIG welding technique.
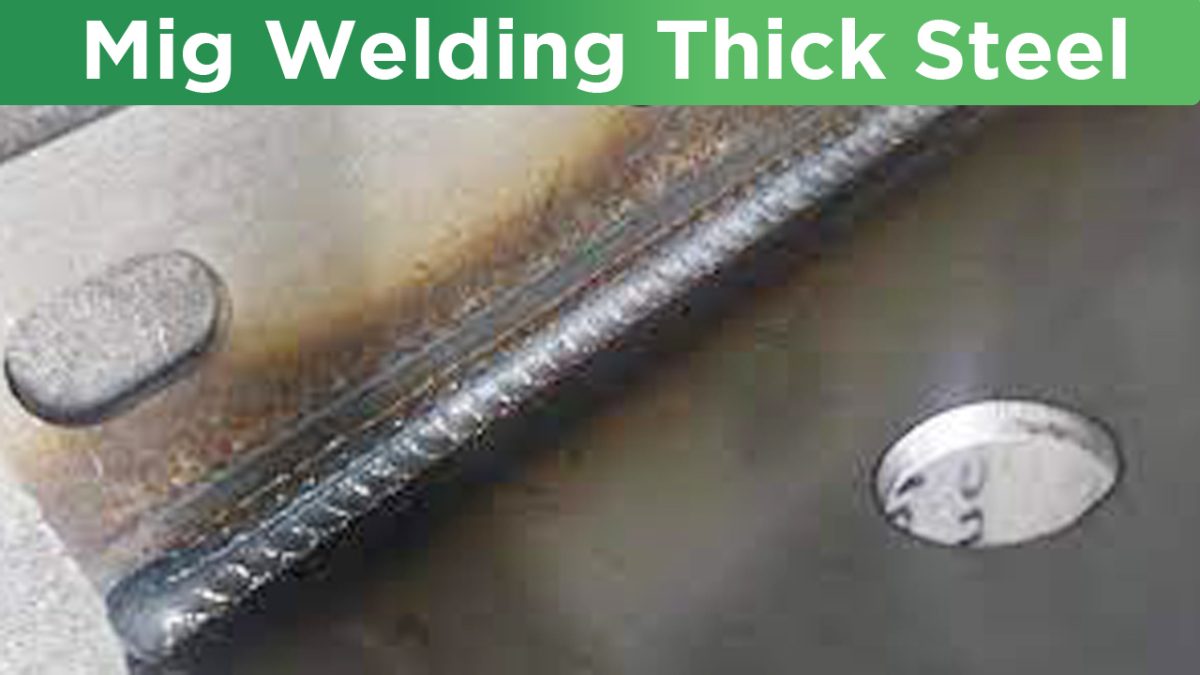
The challenges of welding thick steel
Welding thick steel presents its own unique set of challenges. Thicker steel requires higher heat input and greater penetration to achieve a strong and durable weld. Additionally, the high thermal conductivity of thick steel can result in increased heat dissipation, making it more difficult to maintain proper heat levels during the welding process.
To overcome these challenges, MIG welding is an excellent choice. This welding technique uses a consumable wire electrode that is continuously fed through a welding gun, along with a shielding gas to protect the weld pool from atmospheric contamination. MIG welding offers excellent control, speed, and versatility, making it ideal for working with thick steel.
When welding thick steel, it’s crucial to select the right MIG welder and equipment. Let’s explore the factors to consider when choosing the right MIG welder for thick steel.
Choosing the right MIG welder for thick steel
When selecting a MIG welder for thick steel, there are several factors to consider. The first is the power output of the welder. Thicker steel requires higher amperage to achieve proper penetration. Therefore, it’s essential to choose a MIG welder with sufficient power output to handle the thickness of the steel you’ll be working with.
Another crucial factor to consider is the duty cycle of the welder. Since welding thick steel often requires longer weld times, it’s important to choose a welder with a high duty cycle. The duty cycle refers to the amount of time a welder can operate continuously without overheating.
Additionally, consider the wire feed speed range of the welder. Thicker steel typically requires a higher wire feed speed to achieve proper penetration. Ensure that the MIG welder you choose has a wide enough wire feed speed range to accommodate your needs.
Now that you have selected the right MIG welder, let’s move on to the next crucial aspect of welding thick steel – selecting the appropriate shielding gas.
Selecting the appropriate shielding gas for thick steel welding
Shielding gas plays a vital role in MIG welding, as it protects the weld pool from atmospheric contamination, such as oxygen and nitrogen. When welding thick steel, it’s essential to choose a shielding gas that provides adequate protection and promotes proper weld formation.
The most commonly used shielding gas for MIG welding thick steel is a mixture of argon and carbon dioxide. This gas combination offers excellent weld quality, good penetration, and reduces the risk of porosity in the weld. The exact ratio of argon to carbon dioxide depends on the specific requirements of the welding application.
Other shielding gas options for welding thick steel include 100% carbon dioxide and argon-helium mixtures. However, these gases may result in increased spatter and lower weld quality compared to the argon-carbon dioxide mix.
Now that you have selected the appropriate shielding gas, let’s move on to the next crucial step – preparing the welding joint for thick steel.
Preparing the welding joint for thick steel
Proper preparation of the welding joint is essential for achieving strong and durable welds when working with thick steel. Here are the steps to follow for preparing the welding joint:
- Clean the joint: Thoroughly clean the surfaces to be welded to remove any dirt, rust, or contaminants. Use a wire brush or grinder to ensure a clean and smooth welding surface.
- Bevel the edges: Depending on the thickness of the steel, beveling the edges of the joint may be necessary to achieve proper penetration. Beveling creates a V-shaped groove that allows the weld to penetrate deeper into the joint.
- Align the joint: Ensure that the pieces to be welded are properly aligned and held securely in place. Proper alignment is crucial for achieving strong and visually appealing welds.
Once the welding joint is properly prepared, it’s time to adjust the MIG welding settings for thick steel.
Adjusting the MIG welding settings for thick steel
Achieving the right MIG welding settings is crucial for successful welds on thick steel. Here are the key settings to consider:
- Wire diameter and type: Select a wire diameter suitable for the thickness of the steel. Thicker steel typically requires a larger diameter wire. Additionally, choose a wire type compatible with the base metal to ensure optimal weld quality.
- Voltage and amperage: Set the voltage and amperage based on the thickness of the steel and the wire diameter. Higher amperage and voltage settings are generally required for thicker steel to achieve proper penetration.
- Wire feed speed: Adjust the wire feed speed to maintain a stable arc and achieve proper weld bead formation. Thicker steel typically requires a higher wire feed speed to ensure sufficient weld penetration.
Now that you have adjusted the MIG welding settings, let’s move on to the techniques for welding thick steel.
Techniques for welding thick steel
When welding thick steel, it’s important to use the right techniques to ensure strong and durable welds. Here are some essential techniques to consider:
- Proper torch angle: Maintain a consistent torch angle of around 10-15 degrees to achieve proper heat distribution and penetration. Avoid excessive torch angles, as they can lead to insufficient penetration or excessive heat input.
- Travel speed: Control your travel speed to achieve proper fusion and avoid overheating the weld. Too slow of a travel speed can result in excessive heat input, while too fast of a speed may lead to insufficient penetration.
- Multiple passes: For thicker steel, multiple passes may be required to achieve proper fusion and penetration. Ensure that each pass is clean and properly prepared before proceeding with the next.
By employing these techniques, you can achieve strong and visually appealing welds on thick steel. However, it’s essential to be aware of common mistakes to avoid.
Common mistakes to avoid when welding thick steel
Welding thick steel can be challenging, and certain mistakes can compromise the quality and integrity of the weld. Here are some common mistakes to avoid:
- Insufficient penetration: Ensure that the weld penetrates through the entire thickness of the steel. Insufficient penetration can result in weak welds and potential failure under stress.
- Overheating: Excessive heat input can lead to distortion, warping, and weakened welds. Control your heat input by adjusting the welding parameters and using proper techniques.
- Lack of preheating: Preheating the steel can help reduce the risk of cracking and improve weld quality. Consider preheating for thicker steel to ensure optimal results.
By avoiding these common mistakes, you can enhance the quality and durability of your welds on thick steel. However, it’s crucial to prioritize safety during the welding process.
Safety precautions for MIG welding thick steel
When working with MIG welding and thick steel, it’s important to prioritize safety. Here are some essential safety precautions to follow:
- Wear protective gear: Always wear appropriate protective gear, including a welding helmet, gloves, and flame-resistant clothing, to protect yourself from sparks, UV radiation, and heat.
- Ensure proper ventilation: Welding thick steel can produce harmful fumes and gases. Ensure adequate ventilation in your workspace or use a fume extraction system to remove hazardous fumes.
- Secure your workpiece: Ensure that your workpiece is securely clamped or held in place to prevent movement during the welding process.
By following these safety precautions, you can minimize the risk of accidents and ensure a safe working environment.
Conclusion and final thoughts
MIG welding is an excellent technique for welding thick steel. By understanding the challenges, choosing the right equipment and shielding gas, preparing the welding joint, adjusting the welding settings, employing proper techniques, avoiding common mistakes, and prioritizing safety, you can achieve strong and durable welds on thick steel.
Whether you’re a professional welder or a DIY enthusiast, mastering the art of MIG welding thick steel opens up a world of possibilities. With practice and attention to detail, you can successfully join thick steel pieces together and create impressive structures and projects.
So, don’t be intimidated by the thickness of the steel. Embrace the challenge, follow the guidelines outlined in this article, and let your welding skills shine!