Looking to master the art of plug welding aluminum? From crafting automotive parts to constructing aerospace components, plug welding is a critical technique for joining aluminum pieces effectively. In this article, we delve into the intricacies of plug welding aluminum, exploring the process, best practices, and essential tips to achieve impeccable results.
Whether you are a seasoned welder or just starting, understanding the nuances of plug welding aluminum is vital. With the right knowledge and techniques at your disposal, you can ensure strong, durable welds, ultimately elevating the quality and integrity of your projects.
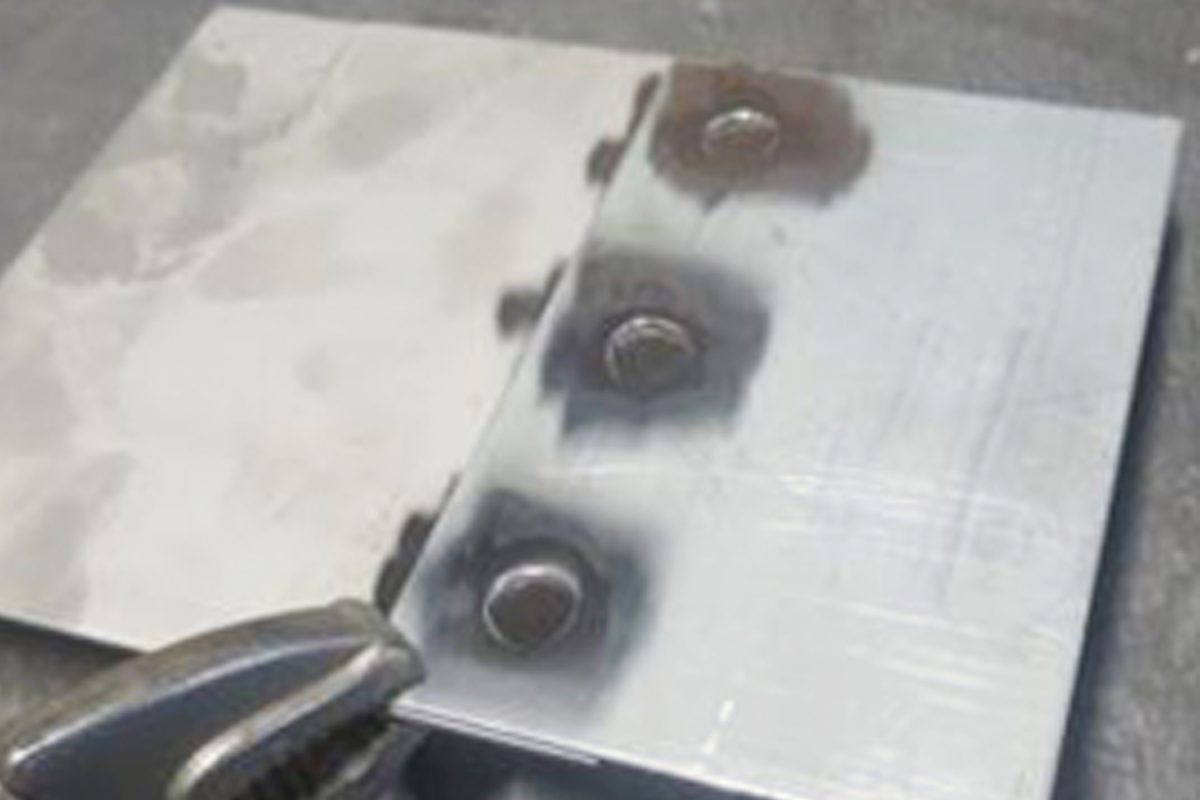
As we uncover the finer points of plug welding aluminum, you will gain insights into selecting the appropriate equipment, preparing the materials, and executing the weld with precision. By the end, you will be equipped with the expertise needed to conquer aluminum plug welding like a seasoned pro. Get ready to elevate your welding prowess and produce top-notch aluminum welds that stand the test of time.
Understanding Plug Welding in Aluminum
Plug welding, also known as plug or slot weld, is a technique used to join two or more pieces of metal together. In aluminum welding, this method involves creating a hole in one piece and welding it to the surface of another. This process is commonly used in industries such as automotive, aerospace, and marine engineering, where the lightweight and durable properties of aluminum are highly valued.
When performed correctly, plug welding creates a strong bond between the pieces, ensuring structural integrity and longevity. Understanding the principles and intricacies of plug welding aluminum is essential for achieving reliable and high-quality welds.
Advantages of Plug Welding Aluminum
The advantages of plug welding aluminum are numerous, making it a preferred method for joining aluminum components. One of the primary benefits is the ability to create a strong and seamless joint without the need for additional fasteners or hardware. This results in a clean and visually appealing finish, especially in applications where aesthetics are important.
Additionally, plug welding allows for the distribution of stress and load across the joint, reducing the likelihood of material failure or fatigue. This is particularly crucial in industries where safety and structural integrity are paramount, such as in the construction of aircraft components or marine vessels.
Plug welding aluminum offers excellent heat dissipation properties, making it suitable for applications that require efficient thermal conductivity. This characteristic is especially advantageous in heat-sensitive environments, where maintaining the structural integrity of the welded components is critical.
Challenges and Considerations for Plug Welding Aluminum
While plug welding aluminum offers various advantages, it also presents unique challenges that require careful consideration. Aluminum is known for its high thermal conductivity and low melting point, posing challenges to the welding process. Controlling the heat input and avoiding excessive heat buildup is crucial to prevent distortion and material degradation.
Another consideration when plug welding aluminum is the potential for weld porosity, which can compromise the integrity of the joint. Proper shielding gas selection and welding parameter adjustments are essential to mitigate the risk of porosity and ensure a defect-free weld.
Additionally, the selection of filler material plays a significant role in the success of plug welding aluminum. Matching the filler material to the base metal composition and employing the appropriate welding technique is essential for achieving strong and reliable welds.
Equipment and Materials for Plug Welding Aluminum
To achieve successful plug welding of aluminum, the use of appropriate equipment and materials is paramount. High-quality welding equipment, such as TIG (tungsten inert gas) or MIG (metal inert gas) welders, is essential for precise control of the welding process and heat input.
When it comes to materials, selecting the right aluminum alloy for the intended application is critical. Different aluminum alloys exhibit varying properties, such as strength, corrosion resistance, and weldability. Understanding the characteristics of the chosen alloy and its compatibility with the welding process is vital for achieving optimal results.
In addition to the base metal and filler material, the use of suitable welding accessories, including clamps, jigs, and fixtures, facilitates the proper alignment and positioning of the workpieces during the plug welding process. This ensures accuracy and consistency in the weld joint, leading to robust and reliable welds.
Step-by-Step Guide to Plug Welding Aluminum
Mastering the art of plug welding aluminum requires a systematic approach and attention to detail. The following step-by-step guide outlines the essential process of plug welding aluminum, from preparation to execution:
- Material Preparation: Begin by selecting the appropriate aluminum alloy for the application and ensuring that the surfaces to be welded are clean and free from contaminants. Proper surface preparation is crucial for achieving strong and durable welds.
- Hole Creation: Mark the location for the plug weld and carefully drill a hole of the specified diameter in the first workpiece. The size of the hole should be in accordance with the welding requirements and the thickness of the base metal.
- Fit-Up and Alignment: Position the pieces to be welded, ensuring proper alignment and fit-up. The accuracy of the fit-up directly influences the quality and strength of the resulting weld joint.
- Welding Setup: Set up the welding equipment, including the appropriate welding machine, filler material, and shielding gas. Adjust the welding parameters, such as current, voltage, and travel speed, to suit the chosen aluminum alloy and thickness.
- Weld Execution: Commence the welding process by depositing the filler material into the prepared hole, forming a secure bond between the workpieces. Control the heat input and welding technique to achieve a consistent and defect-free weld.
- Post-Weld Inspection: After completing the weld, inspect the joint for any defects, such as porosity or incomplete fusion. Non-destructive testing methods, such as visual inspection and penetrant testing, can be employed to ensure the integrity of the weld.
By following these steps with precision and attention to detail, you can master the art of plug welding aluminum and produce high-quality welds that meet the stringent requirements of various industries.
Common Mistakes to Avoid in Plug Welding Aluminum
While plug welding aluminum can yield exceptional results when executed with skill and precision, certain common mistakes can compromise the integrity and quality of the welds. Avoiding these pitfalls is crucial for achieving reliable and durable plug welds in aluminum:
- Inadequate Surface Preparation: Neglecting to thoroughly clean and prepare the welding surfaces can lead to contamination and poor weld quality. Proper surface cleaning and removal of oxides are essential for successful plug welding.
- Incorrect Hole Size: Using a hole that is too large or too small for the intended weld size can result in weak and inconsistent plug welds. Adhering to the recommended hole size based on the material thickness is crucial for achieving optimal results.
- Improper Fit-Up: Poor alignment and fit-up of the workpieces can lead to misalignment and weak weld joints. Ensuring precise fit-up and alignment is essential for creating strong and reliable plug welds.
- Excessive Heat Input: Overheating the aluminum during the welding process can cause distortion, material degradation, and potential weld defects. Controlling the heat input and employing proper welding techniques is vital for achieving high-quality plug welds.
- Incorrect Filler Material Selection: Using an inappropriate filler material or mismatched filler alloy can result in weak and unreliable welds. Selecting the correct filler material that matches the base metal composition is essential for achieving strong weld joints.
By recognizing and avoiding these common mistakes, you can elevate your plug welding skills and produce impeccable aluminum welds that meet the highest standards of quality and performance.
Benefits of Plug Welding Aluminum in Various Industries
The application of plug welding aluminum extends across a wide range of industries, offering numerous benefits in diverse applications. Let’s explore the advantages and uses of plug welding aluminum in various sectors:
Automotive Industry: In the automotive sector, plug welding aluminum is commonly employed in the fabrication of vehicle body components, such as panels, frames, and structural elements. The ability to create secure and visually appealing welds without the need for additional fasteners contributes to the lightweight design and structural integrity of modern vehicles.
Aerospace and Aviation: Plug welding aluminum plays a critical role in the construction of aerospace components, including aircraft structures, fuselage panels, and interior fixtures. The lightweight and high-strength characteristics of aluminum, combined with the seamless and reliable welds achieved through plug welding, contribute to the efficiency and performance of aerospace systems.
Marine Engineering: The marine industry relies on plug welding aluminum for the assembly of watercraft, marine structures, and offshore equipment. The corrosion resistance and durability of aluminum, coupled with the ability to create robust weld joints, make it an ideal choice for maritime applications.
Construction and Architecture: In the construction and architectural sectors, plug welding aluminum finds applications in the fabrication of structural elements, facade systems, and interior fittings. The aesthetic appeal and structural integrity achieved through plug welding contribute to the modern and durable design of architectural structures.
By harnessing the benefits of plug welding aluminum, these industries can leverage the lightweight, durable, and visually appealing properties of aluminum to create high-performance and reliable products.
Training and Certification for Plug Welding Aluminum
As the demand for skilled aluminum welders continues to grow, obtaining proper training and certification in plug welding aluminum is essential for professional development and industry recognition. Various training programs and certification courses are available to equip welders with the knowledge and skills required to excel in aluminum welding, including plug welding techniques.
These programs cover a comprehensive curriculum, encompassing the principles of aluminum metallurgy, welding processes, safety practices, and hands-on training in plug welding aluminum. Additionally, certification courses provide validation of a welder’s proficiency and competence in executing aluminum plug welds to industry standards.
By pursuing training and certification in plug welding aluminum, welders can enhance their career prospects, demonstrate their expertise to potential employers, and contribute to the advancement of the aluminum welding industry.
Plug Welding Aluminum Services and Providers
For organizations and individuals seeking professional plug welding aluminum services, partnering with reputable welding providers is crucial for ensuring the quality and integrity of the welds. Reliable welding service providers offer expertise in plug welding aluminum, backed by state-of-the-art equipment, skilled personnel, and adherence to industry standards.
When selecting a plug welding service provider, consider factors such as their experience in aluminum welding, certifications and accreditations, quality assurance practices, and the ability to tailor their services to specific project requirements. Collaborating with established welding providers ensures that your aluminum plug welding needs are met with precision, reliability, and professionalism.
Additionally, welding service providers may offer consultation and advisory services to assist clients in selecting the most suitable welding techniques, materials, and processes for their aluminum welding projects. By leveraging the expertise of reputable welding providers, organizations can achieve exceptional results in their plug welding endeavors.
Conclusion and Future of Plug Welding Aluminum
Plug welding aluminum is a fundamental technique that holds immense significance in various industries, offering exceptional strength, durability, and aesthetic appeal in joining aluminum components. By understanding the intricacies of plug welding aluminum, addressing its challenges, and leveraging the right equipment and materials, welders can achieve impeccable results and elevate the quality of their projects.
As the demand for lightweight, durable, and visually appealing metal components continues to rise across industries, the future of plug welding aluminum remains promising. Advancements in welding technology, materials research, and industry standards will further enhance the capabilities and potential applications of plug welding aluminum, contributing to the innovation and advancement of aluminum welding practices.
As you embark on your journey to master the art of plug welding aluminum, remember to stay updated on the latest developments in aluminum welding techniques, seek opportunities for continuous learning and skill development, and always strive for precision and excellence in your welds. With the right knowledge, dedication, and passion for aluminum welding, you can achieve remarkable success in plug welding aluminum and make a lasting impact in the world of metal fabrication and engineering.