In the world of metal fabrication and welding, electron beam welding is a cutting-edge technology that offers precision and efficiency. By harnessing the power of high-energy electrons, this process can create strong and durable welds with minimal heat distortion. However, not all electron beam welding systems are the same. In this article, we will explore different types of electron beam welding based on the accelerating voltage, processing chamber pressure, and electron gun mounting position.
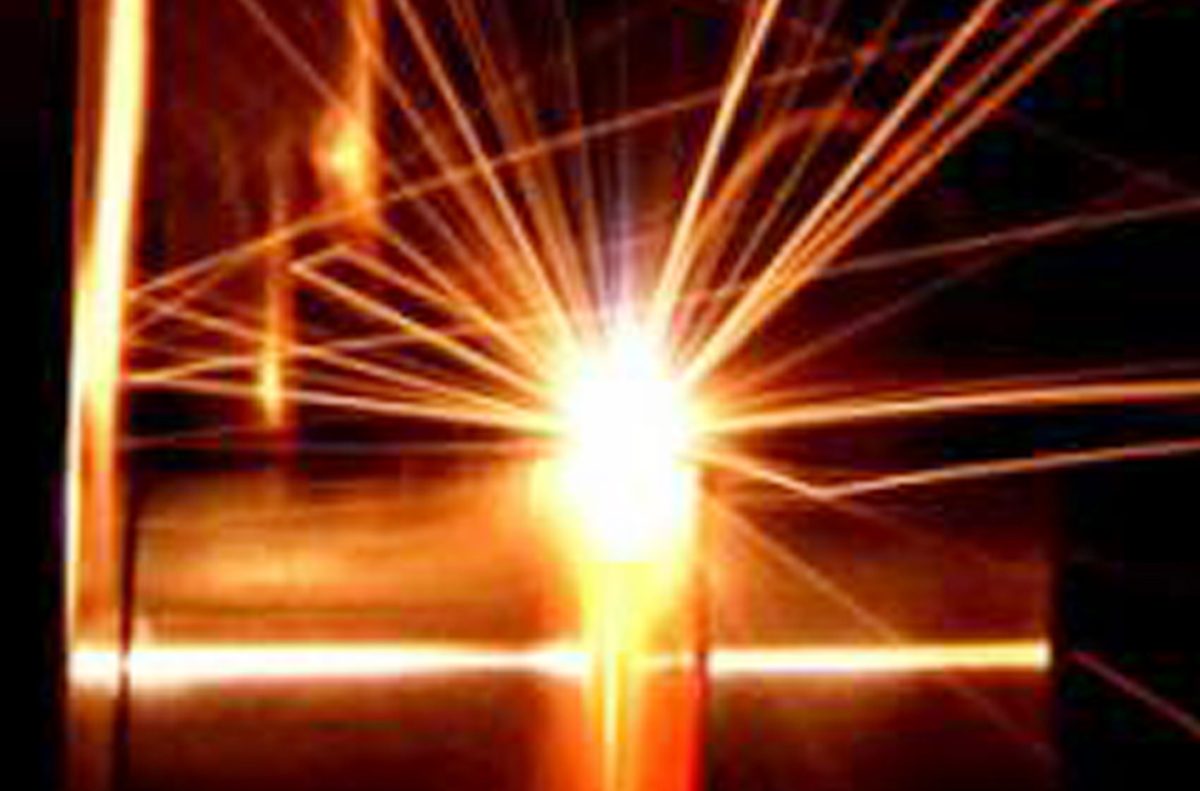
How electron beam welding works
Electron beam welding is a process that utilizes a focused beam of high-energy electrons to join metal parts together. This beam is generated by an electron gun, which emits electrons in a vacuum environment. The electrons are accelerated to high speeds using an electric field, creating a concentrated and powerful beam. This beam is then directed towards the workpiece, where it melts the metal and forms a weld joint.
The key advantage of electron beam welding is its ability to deliver a high amount of energy in a small and controlled area. This allows for precise and deep penetration, resulting in strong and defect-free welds. Additionally, the lack of contact between the welding tool and the workpiece reduces the risk of contamination or damage to the materials.
Accelerating voltage
The accelerating voltage in electron beam welding refers to the electric potential difference applied to accelerate the electrons. This voltage plays a crucial role in determining the depth and speed of the weld penetration. Higher accelerating voltages result in deeper and faster welds, while lower voltages are suitable for more delicate materials or thinner sections.
The choice of accelerating voltage depends on the specific welding requirements and the properties of the materials being welded. For thicker sections or materials with higher melting points, higher accelerating voltages are generally used to ensure sufficient penetration. On the other hand, lower voltages are preferred for thin or heat-sensitive materials to minimize the risk of distortion or burn-through.
Importance of accelerating voltage
The accelerating voltage in electron beam welding has a significant impact on the overall welding process. By adjusting the voltage, welders can control the depth of penetration, the width of the weld bead, and the overall heat input. This level of control allows for precise and tailored welds, ensuring optimal joint strength and quality.
The choice of accelerating voltage also affects the weld speed. Higher voltages result in faster welding speeds, which can be beneficial for large-scale production or time-sensitive projects. Conversely, lower voltages may require slower welding speeds to achieve the desired penetration, which can be advantageous for intricate or complex welds.
Processing chamber pressure
The processing chamber pressure in electron beam welding refers to the pressure of the gas or vacuum environment in which the welding process takes place. This pressure plays a critical role in controlling the environment in which the electron beam interacts with the workpiece.
The choice of processing chamber pressure depends on several factors, including the materials being welded, the desired weld quality, and the specific requirements of the welding process. In a high-pressure environment, such as a gas-filled chamber, the electron beam interacts differently with the workpiece compared to a low-pressure or vacuum environment. This can affect the behavior of the beam, the heat distribution, and the overall weld quality.
Effects of processing chamber pressure
The processing chamber pressure in electron beam welding has a direct impact on the resulting weld quality. In a high-pressure environment, the gas molecules can scatter the electron beam and lead to increased heat dissipation. This can result in a wider and shallower weld bead, reduced depth of penetration, and potentially weaker joint strength.
Conversely, in a low-pressure or vacuum environment, the electron beam can travel more freely and reach higher speeds. This can result in deeper penetration, narrower weld beads, and increased joint strength. However, operating in a vacuum can also pose challenges, as it requires specialized equipment and additional safety measures to maintain the vacuum environment.
Electron gun mounting position
The electron gun mounting position in electron beam welding refers to the angle and accessibility of the electron beam as it is directed towards the workpiece. This position plays a crucial role in determining the weld quality and joint design.
The choice of electron gun mounting position depends on the specific welding requirements and the geometry of the workpiece. Different mounting positions can be used to achieve various weld configurations, such as butt joints, fillet joints, or overlap joints. By adjusting the mounting position, welders can control the angle of the beam and the overlap of the weld, ensuring optimal joint strength and aesthetics.
Significance of electron gun mounting position
The electron gun mounting position in electron beam welding is significant as it directly affects the weld quality and the overall welding process. By choosing the appropriate mounting position, welders can optimize the weld bead shape, control the heat input, and minimize the risk of defects or distortions.
For example, a perpendicular mounting position, where the electron beam is directed straight onto the workpiece, is commonly used for butt joints or flat welding surfaces. This position provides optimal penetration and joint strength. However, for fillet joints or curved surfaces, an angled mounting position may be necessary to ensure proper fusion and avoid excessive heat input.
Comparing different types of electron beam welding
The different types of electron beam welding can be categorized based on the accelerating voltage, processing chamber pressure, and electron gun mounting position. By comparing these types, welders can choose the most suitable option for their specific project requirements.
For example, high-voltage electron beam welding is often used for thick or heavy materials that require deep penetration and fast welding speeds. On the other hand, low-voltage electron beam welding is suitable for thin or heat-sensitive materials that require precise control and minimal distortion.
Similarly, the choice of processing chamber pressure depends on the desired weld quality and the specific welding process. High-pressure electron beam welding can be used for certain applications where increased heat dissipation or wider weld beads are acceptable. In contrast, low-pressure or vacuum electron beam welding is preferred for applications that require deep penetration, narrow weld beads, and enhanced joint strength.
Finally, the electron gun mounting position determines the angle and accessibility of the electron beam. Different mounting positions can be utilized to achieve various weld configurations and joint designs. Welders must consider the geometry of the workpiece and the specific requirements of the weld when choosing the mounting position.
Conclusion
Electron beam welding is a versatile and efficient technology that offers precise and strong welds for metal fabrication. By understanding the different types of electron beam welding based on the accelerating voltage, processing chamber pressure, and electron gun mounting position, welders can select the most suitable option for their specific project requirements.
The choice of accelerating voltage determines the depth and speed of weld penetration, while the processing chamber pressure controls the welding environment and affects the weld quality. The electron gun mounting position influences the weld angle and joint design, ensuring optimal joint strength and aesthetics.
By harnessing the power of electron beam welding and choosing the right parameters, welders can revolutionize their metal fabrication processes, achieving superior weld quality and cost-effectiveness. So, embrace the advancements in electron beam welding and unlock a world of possibilities for your welding projects.