Laser welding stainless steel has emerged as a game-changing technology in the manufacturing industry, offering a seamless and precise method for joining stainless steel components. By harnessing the power of focused laser beams, this advanced technique ensures minimal heat distortion and superior welding quality. The process of laser welding stainless steel provides unmatched precision, creating strong, clean, and aesthetically pleasing welds with minimal post-welding work required.
This innovative welding method not only enhances efficiency but also elevates the overall quality of the final product. The laser’s ability to deliver concentrated heat results in less material wastage and a finer finish, setting a new benchmark for metal joining processes. As the demand for immaculate stainless steel welds continues to rise across various industries, the significance of laser welding in meeting these requirements cannot be overstated. From automotive to aerospace applications, the versatility and reliability of laser welding stainless steel have positioned it as the go-to solution for achieving impeccable welds across diverse manufacturing sectors.
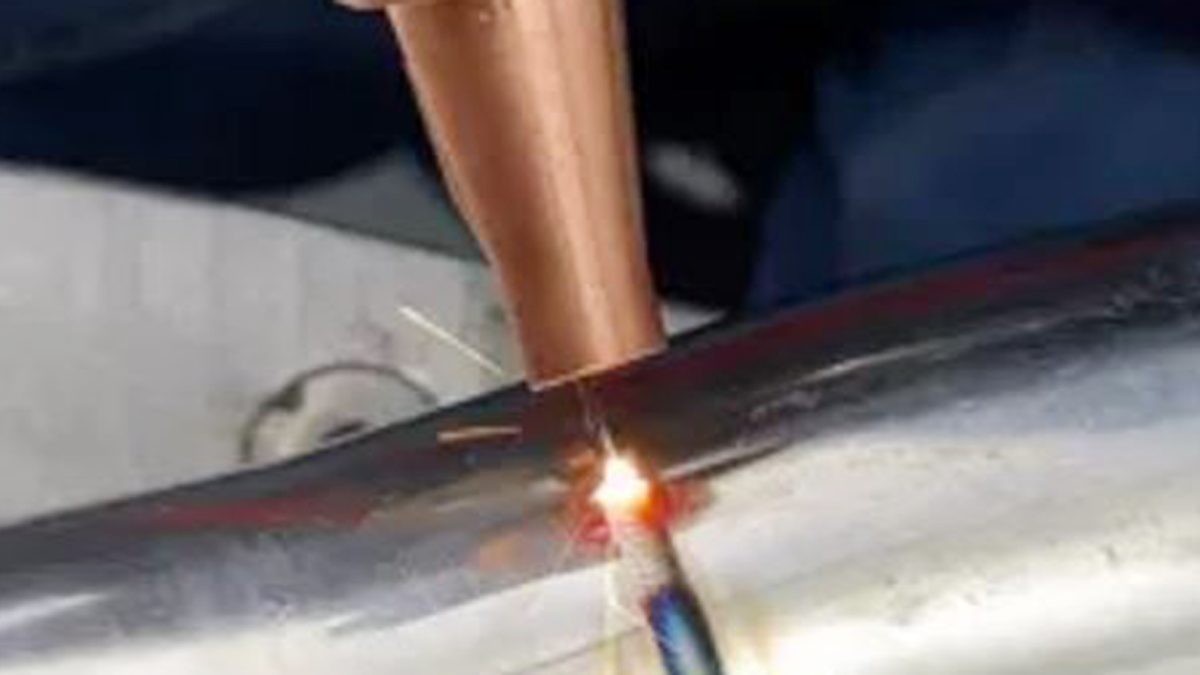
Laser Welding and Its Applications
Laser welding is a process that utilizes a highly concentrated beam of light energy to fuse metals together. This technology has found widespread applications in various industries, including automotive, aerospace, medical, and consumer electronics. When it comes to stainless steel, laser welding offers numerous advantages over traditional welding methods, making it an ideal choice for applications that demand precision and high-quality welds.
Laser welding provides a non-contact process, which minimizes the risk of contamination and reduces the need for extensive cleaning after welding. The ability to focus the laser beam precisely allows for intricate and detailed welds, making it suitable for joining thin stainless steel components without causing damage to the surrounding areas. The speed and accuracy of laser welding contribute to increased productivity and cost-effectiveness, making it a preferred choice for manufacturers looking to streamline their production processes.
The ability to control the heat input during laser welding helps in minimizing distortion and preserving the material’s integrity, resulting in aesthetically pleasing welds that meet stringent quality standards. As a result, laser welding has become an indispensable technique for achieving high-quality stainless steel welds in a wide range of industrial applications.
Advantages of Laser Welding Stainless Steel
Laser welding stainless steel offers a plethora of advantages that set it apart from conventional welding methods. One of the most significant benefits is the minimal heat-affected zone (HAZ) associated with laser welding. This means that the surrounding material experiences minimal thermal distortion, preserving the structural integrity of the stainless steel components.
In addition to reduced heat distortion, laser welding produces narrow and deep weld seams, resulting in superior mechanical properties and enhanced aesthetic appeal. The precision and control offered by laser welding contribute to the production of clean, high-quality welds with minimal post-welding finishing required. This not only saves time and resources but also ensures that the welded components meet the highest standards of visual and structural integrity.
Moreover, laser welding allows for the joining of dissimilar materials, opening up new possibilities for innovative product designs and multi-material assemblies. The ability to weld thin and delicate stainless steel components without compromising their structural integrity makes laser welding an ideal choice for applications where precision and strength are paramount.
Factors Affecting the Quality of Laser Welds in Stainless Steel
Several factors play a crucial role in determining the quality and integrity of laser welds in stainless steel. One of the primary considerations is the selection of the appropriate laser parameters, including power density, pulse duration, and beam focus. These parameters must be carefully optimized to ensure the desired penetration depth, weld width, and heat input, thereby achieving a strong and reliable weld joint.
The composition of the stainless steel alloy also influences the welding process, as different grades of stainless steel exhibit varying responses to laser welding. Factors such as the material’s thermal conductivity, reflectivity, and susceptibility to cracking must be taken into account when setting up the welding parameters to achieve consistent and high-quality welds.
Furthermore, proper joint fit-up and alignment are critical to the success of laser welding stainless steel. Precise control of the joint geometry and gap distance is essential to ensure full penetration and uniform fusion across the weld interface. Additionally, the use of shielding gases and specialized welding techniques, such as keyhole or conduction mode welding, can significantly impact the quality and appearance of the welds, making them essential considerations in the laser welding process.
Types of Laser Welding Techniques for Stainless Steel
Laser welding techniques for stainless steel can be broadly categorized into two primary methods:
Conduction mode welding and keyhole mode welding. Conduction mode welding, also known as heat conduction welding, utilizes lower power densities to generate shallow welds with minimal penetration. This method is suitable for thin stainless steel sheets and delicate components where controlling heat input and minimizing distortion are paramount.
On the other hand, keyhole mode welding involves higher power densities that create a deep, narrow weld seam by vaporizing the material and forming a stable keyhole within the weld pool. This technique is well-suited for thicker stainless steel sections and applications that require robust and deep weld penetration. Keyhole mode welding offers higher welding speeds and greater depth-to-width ratios, making it ideal for achieving strong and reliable weld joints in challenging stainless steel welding scenarios.
Each welding technique has its unique advantages and applications, and the selection of the appropriate method depends on the specific requirements of the stainless steel components being welded. By understanding the characteristics and capabilities of conduction mode and keyhole mode welding, manufacturers can leverage the full potential of laser welding to achieve optimal results in their stainless steel welding processes.
Preparing Stainless Steel for Laser Welding
Proper preparation of stainless steel surfaces is critical to ensuring successful laser welding and achieving high-quality weld joints. Before initiating the welding process, it is essential to thoroughly clean the surfaces to remove any contaminants, such as oil, grease, or oxides, that could interfere with the weld quality. This can be achieved through solvent cleaning, mechanical abrasion, or chemical treatments, depending on the nature of the surface contaminants.
In addition to surface cleaning, proper joint design and fit-up play a crucial role in preparing stainless steel for laser welding. Precision machining and accurate alignment of the components to be welded are essential to ensure optimal weld penetration and fusion. Maintaining tight tolerances and minimizing gaps between the mating surfaces is imperative for achieving strong and uniform welds in stainless steel.
The selection of suitable filler materials, if required, and the implementation of effective shielding gas strategies are essential aspects of preparing steel for welding. The use of compatible filler metals and appropriate shielding gases can enhance the weld pool stability, promote metallurgical compatibility, and minimize the risk of weld defects, ultimately contributing to the overall quality and integrity of the laser welds.
Best Practices for Laser Welding Stainless Steel
To achieve exceptional results in laser welding stainless steel, adherence to best practices is essential. Implementing proper laser beam delivery and control systems, such as fiber optic beam delivery and advanced beam shaping technologies, ensures precise energy deposition and optimal weld pool dynamics, leading to consistent and high-quality welds.
Maintaining a stable and controlled welding environment, including proper gas shielding and ventilation systems, is crucial for minimizing oxidation and ensuring the cleanliness of the weld zone. Effective control of the welding parameters, such as pulse frequency, beam focus, and travel speed, is essential for achieving the desired weld penetration, fusion, and overall weld quality.
In addition to technical considerations, operator training and proficiency in laser welding techniques are integral to the success of stainless steel welding processes. Providing comprehensive training programs and certifications for laser welding operators enables them to master the intricacies of laser welding technology, optimize process parameters, and troubleshoot potential welding issues, thereby ensuring consistent and reliable weld quality.
Common Challenges and Solutions in Laser Welding Stainless Steel
While laser welding stainless steel offers numerous advantages, it is not without its challenges. One common issue is the formation of weld defects, such as porosity, cracking, or lack of fusion, which can compromise the integrity of the weld joint. Addressing these challenges requires a thorough understanding of the laser welding process and the implementation of effective mitigation strategies.
Controlling the heat input and managing thermal gradients are critical in minimizing the risk of weld defects in stainless steel laser welding. By optimizing the laser parameters and adapting the welding techniques to suit the specific characteristics of the stainless steel alloy being welded, manufacturers can mitigate the risk of defects and ensure the production of high-quality and durable welds.
Another challenge in laser welding stainless steel is managing the potential for material distortion, particularly in thin or heat-sensitive components. Utilizing advanced fixturing and clamping techniques, as well as implementing controlled pre-heating and post-welding cooling processes, can help alleviate the effects of thermal distortion and preserve the dimensional stability of the welded assemblies.
Comparing Laser Welding with Other Stainless Steel Welding Methods
In comparison to traditional welding methods, such as gas tungsten arc welding (GTAW) and gas metal arc welding (GMAW), laser welding offers distinct advantages for joining stainless steel components. Unlike conventional welding processes that rely on electrical arcs and consumable electrodes, laser welding provides a non-contact, high-energy beam that minimizes material contamination, reduces heat-affected zones, and enables precise control over the welding process.
Moreover, laser welding excels in producing narrow and deep weld seams with minimal distortion, resulting in visually appealing and structurally sound welds. This stands in contrast to the broader and shallower weld beads typically associated with traditional welding methods, where greater post-welding finishing and cleanup are often required to achieve the desired weld quality and aesthetics.
Additionally, laser welding’s ability to achieve high welding speeds, intricate weld geometries, and minimal heat input makes it a preferred choice for applications that demand precision, efficiency, and superior weld quality. As a result, laser welding has become the method of choice for achieving impeccable welds in stainless steel components across a wide range of industrial sectors, setting new standards for welding excellence and production efficiency.
Final Thoughts
Laser welding stainless steel represents a paradigm shift in precision joining, offering unparalleled advantages in terms of weld quality, efficiency, and versatility. By harnessing the power of focused laser beams, manufacturers can achieve immaculate welds in stainless steel components, meeting the exacting standards of diverse industries, from automotive and aerospace to medical and consumer electronics.
The ability of laser welding to minimize heat distortion, produce narrow and deep weld seams, and enable precise control over the welding process sets it apart as the go-to solution for achieving superior weld quality in stainless steel. As the demand for flawless stainless steel welds continues to grow, laser welding stands at the forefront of innovation, driving the advancement of manufacturing processes and setting new benchmarks for welding excellence.
With proper training, adherence to best practices, and a deep understanding of laser welding principles, manufacturers can harness the full potential of laser welding technology to elevate the quality and precision of stainless steel welds, shaping the future of metal joining in the manufacturing industry.
In conclusion, laser welding stainless steel has redefined the possibilities of precision welding, ushering in a new era of manufacturing excellence and product innovation. As industries continue to embrace the advantages of laser welding, the pursuit of flawless stainless steel welds will only continue to evolve, driven by the unparalleled capabilities of laser welding technology.