Imagine having the power to seamlessly mend plastic components, restore your car’s structural integrity, and enhance its aesthetic appeal with a professional touch. Whether you are a seasoned auto enthusiast or a DIY-er, mastering the art of plastic welding empowers you to tackle a wide range of automotive fixes with confidence and precision. With the right tools and techniques at your disposal, plastic welding becomes a cost-effective and sustainable solution, adding value to your vehicle in the long run. As the automotive industry continues to evolve, the demand for reliable plastic welding solutions escalates, making it an indispensable skill for any car owner.
In this guide, we will delve into the world of automotive plastic welding, explore the essential tools and kits, and provide expert tips to elevate your craftsmanship. Buckle up as we embark on a journey to uncover the boundless potential of automotive plastic welding and kits to transform your vehicle maintenance routine.
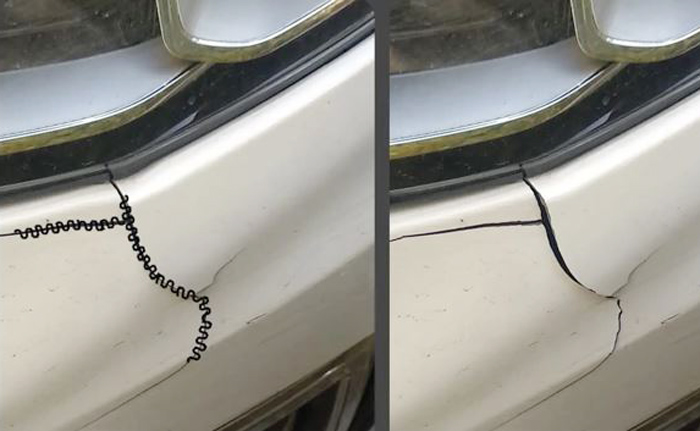
Definition Automotive Plastic Welding
Automotive plastic welding is a specialized technique used to join plastic components together. It involves the use of heat and pressure to melt and fuse the plastic, creating a strong and durable bond. Unlike traditional bonding methods that rely on adhesives or mechanical fasteners, plastic welding offers a seamless and homogeneous connection, preserving the structural integrity of the plastic parts. This technique is widely employed in automotive repairs to fix cracked bumpers, broken taillights, damaged interior panels, and various other plastic components. By understanding the principles of automotive plastic welding, you gain the ability to restore your vehicle to its original condition with precision and expertise.
Plastic welding in the automotive industry has gained traction due to its versatility and effectiveness in repairing a wide range of plastic materials commonly used in vehicles. Whether it’s polypropylene, polyethylene, ABS, or other thermoplastics, automotive plastic welding provides a reliable solution for addressing structural damage and cosmetic imperfections. By mastering this technique, car owners and professionals alike can elevate the quality of their repairs, ensuring long-lasting and visually appealing results. As we delve deeper into the advantages of automotive plastic welding, you’ll discover the transformative impact it can have on your vehicle maintenance approach.
Advantages of Automotive Plastic Welding
The advantages of automotive plastic welding extend beyond the mere act of joining plastic components. This technique offers several benefits that set it apart from traditional repair methods. Firstly, plastic welding provides a seamless and nearly invisible repair, preserving the original aesthetics of the vehicle. Unlike adhesives or fillers, which can often leave visible seams or marks, plastic welding creates a homogeneous bond that seamlessly blends with the surrounding plastic surfaces. This results in a professional-looking repair that restores the car’s visual appeal and maintains its resale value.
In addition to its cosmetic benefits, automotive plastic welding also ensures structural integrity and longevity. The fused plastic joint created through welding is as strong as the original material, providing a durable and reliable repair solution. This is particularly crucial in areas of the vehicle that are subjected to stress, such as bumpers, fenders, and other exterior components. By using plastic welding to address structural damage, car owners can rest assured that their repairs will stand the test of time, withstanding the rigors of everyday use and environmental exposure.
Another key advantage of automotive plastic welding is its cost-effectiveness. Unlike replacing entire components or using labor-intensive repair methods, plastic welding allows for targeted and localized repairs. This minimizes the need for expensive part replacements and reduces labor costs, making it a more budget-friendly option for both DIY enthusiasts and professional repair shops.
The sustainability aspect of plastic welding cannot be overlooked. By repairing and reusing plastic components, rather than discarding and replacing them, automotive plastic welding aligns with eco-friendly practices, contributing to a more sustainable approach to vehicle maintenance and repair.
Types of Plastic Welding Kits for Automotive Use
When it comes to automotive plastic welding, having the right tools and equipment is paramount to achieving professional results. There are several types of plastic welding kits designed specifically for automotive use, each catering to different repair needs and skill levels. Understanding the various types of welding kits and their applications is crucial for selecting the most suitable option for your specific requirements.
One common type of plastic welding kit for automotive use is the hot air plastic welding kit. This kit typically includes a heat gun or hot air welder, welding rods, and various accessories for manipulating and smoothing the melted plastic. Hot air welding is a versatile technique that can be used for a wide range of thermoplastics, making it a popular choice for automotive repairs. The heat gun emits a controlled stream of hot air, which softens the plastic surface and the welding rod, allowing them to fuse together seamlessly. Hot air welding kits are ideal for repairing cracks, splits, and other damage on plastic components, providing a strong and nearly invisible bond.
Another type of plastic welding kit commonly used in automotive applications is the ultrasonic plastic welding kit. This advanced welding technique utilizes high-frequency vibrations to create friction and generate heat, melting the plastic and forming a strong weld. Ultrasonic welding is particularly effective for joining small or intricate plastic components, such as sensors, connectors, and interior trim pieces. While ultrasonic welding equipment may be more specialized and suited for professional workshops, it offers unparalleled precision and control for intricate automotive plastic repairs.
For car owners and enthusiasts looking to venture into automotive plastic welding, there are also handheld plastic welding kits available. These compact and portable kits are designed for DIY use, offering a convenient and accessible solution for small-scale repairs. Handheld plastic welders typically utilize a combination of heat and pressure to melt and fuse the plastic, providing a user-friendly approach for beginners and hobbyists.
With the right selection of welding rods and accessories, handheld welding kits can be used to address minor damages and cosmetic imperfections, empowering car owners to take their repairs into their own hands.
Tools and Equipment Required for Automotive Plastic Welding
In addition to the specific welding kits, there are essential tools and equipment that are fundamental to automotive plastic welding. These tools not only facilitate the welding process but also contribute to the precision and quality of the repairs. Understanding the role of each tool and its significance in the welding process is essential for achieving professional-grade results in automotive plastic welding.
One of the primary tools required for automotive plastic welding is a heat source, which can vary depending on the welding technique being used. For hot air welding, a heat gun or hot air welder is essential. These devices emit a controlled stream of hot air at precise temperatures, allowing for the softening and fusion of the plastic material.
When using ultrasonic welding, specialized ultrasonic welding equipment, including a generator and transducer, is needed to produce the high-frequency vibrations required for the welding process. Handheld plastic welding kits typically incorporate a heating element and pressure applicator, enabling users to melt and fuse the plastic manually.
In addition to the heat source, welding rods are indispensable for automotive plastic welding. These rods, also known as filler rods, are made from the same or compatible plastic material as the components being repaired. They act as a reinforcement for the weld, providing additional material to create a strong and durable joint. Welding rods come in various shapes, sizes, and compositions to suit different plastic types and repair scenarios. It’s essential to select the appropriate welding rods for the specific plastic material being welded, ensuring compatibility and optimal bonding strength.
Apart from the core welding tools, supplementary equipment such as scrapers, cutters, and smoothing tools play a crucial role in automotive plastic welding. Scrapers are utilized for removing excess or unevenly melted plastic, ensuring a smooth and uniform surface finish. Cutters enable precise trimming and shaping of the welded area, allowing for seamless integration with the surrounding components. Smoothing tools, such as heated tacking irons or rollers, aid in refining the welded joint, creating a professional and polished appearance. By utilizing these auxiliary tools effectively, automotive plastic welders can achieve seamless and high-quality repairs that meet professional standards.
Steps for Automotive Plastic Welding
Mastering the steps for automotive plastic welding is essential for achieving optimal results and ensuring the longevity of the repairs. While the specific process may vary depending on the type of plastic, the extent of damage, and the chosen welding technique, there are fundamental steps that form the basis of automotive plastic welding. By following these steps with precision and attention to detail, car owners and professionals can elevate their welding proficiency and produce professional-grade repairs.
The first step in automotive plastic welding involves preparing the damaged area for the welding process. This includes cleaning the surface to remove any contaminants, residues, or adhesives that may hinder the welding bond. Proper cleaning and preparation ensure that the plastic surfaces are free from impurities, allowing for optimal fusion and adhesion during the welding process. The damaged area may need to be shaped or trimmed to create clean edges and facilitate a seamless welding joint.
Once the preparation is complete, the next step is to select the appropriate welding technique and equipment based on the type of plastic and the nature of the damage. Whether it’s hot air welding, ultrasonic welding, or handheld welding, the choice of technique should align with the specific requirements of the repair. This involves setting the correct temperature, pressure, and welding rod composition to ensure a strong and durable bond. For hot air welding, adjusting the airflow and temperature of the heat gun is crucial for achieving the optimal melting and fusion of the plastic material.
After the welding technique and equipment are chosen, the actual welding process begins. This involves applying heat and pressure to the plastic surfaces, melting the material and the welding rod, and creating a homogeneous and robust joint. Careful control and manipulation of the welding tools are essential during this stage to achieve a uniform and well-bonded weld. Depending on the extent of the damage and the size of the repair area, multiple passes or layers of welding may be necessary to reinforce the joint and ensure its strength.
Once the welding is complete, the final steps involve refining and finishing the welded area to achieve a seamless and professional appearance. This includes trimming any excess material, smoothing the welded joint, and blending it with the surrounding surfaces. Additionally, post-welding processes such as cooling, annealing, or stress-relieving may be employed to enhance the strength and durability of the weld. By meticulously following these steps and techniques, automotive plastic welders can produce repairs that meet industry standards and exceed expectations.
Safety Measures for Automotive Plastic Welding
As with any automotive repair or maintenance task, safety should always be a top priority when engaging in plastic welding. The process of melting and fusing plastic materials involves the use of heat, potentially hazardous fumes, and the manipulation of hot tools and equipment. By observing essential safety measures, automotive plastic welders can ensure their well-being and the integrity of their repairs.
One crucial safety measure in automotive plastic welding is the use of personal protective equipment (PPE). This includes safety goggles or a full-face shield to protect the eyes and face from hot plastic particles, UV radiation, and potential splashes. Heat-resistant gloves are also essential to safeguard the hands from burns and thermal injuries when handling heated tools and welding equipment. Additionally, wearing a respirator or working in a well-ventilated area is crucial to minimize exposure to fumes and airborne contaminants generated during the welding process.
Another important safety consideration is the proper handling and storage of welding equipment and materials. Heat guns, hot air welders, and other heat-emitting devices should be used with caution to avoid accidental burns and fires. Furthermore, welding rods and plastic materials should be stored in a cool, dry, and secure environment to prevent degradation and potential hazards. It’s also advisable to keep flammable materials and sources of ignition away from the welding area to minimize the risk of fire or combustion accidents.
In addition to personal protective measures, proper training and familiarity with the specific welding techniques and equipment are essential for safe and effective automotive plastic welding. Beginners and DIY enthusiasts should seek comprehensive instruction and practice in a controlled environment before attempting complex or critical repairs. Professionals and experienced welders should regularly update their knowledge of safety protocols and industry best practices to minimize risks and ensure the well-being of themselves and others involved in the welding process.
Common Applications of Automotive Plastic Welding
Automotive plastic welding finds myriad applications in vehicle repairs, restoration, and customization. From addressing structural damage to enhancing cosmetic features, plastic welding is a versatile and indispensable technique that caters to a wide range of automotive needs. Understanding the common applications of automotive plastic welding provides insight into the diverse ways in which this technique can be utilized to maintain and improve vehicles.
One of the primary applications of automotive plastic welding is the repair of cracked or damaged bumpers. Bumpers are prone to impact damage, scratches, and cracks, which can compromise their structural integrity and visual appeal. By employing plastic welding, car owners and repair shops can seamlessly mend bumper damage, reinforcing the impacted areas and restoring the original appearance. This not only ensures the functionality of the bumper in absorbing impacts but also enhances the overall aesthetic of the vehicle.
Another common application of automotive plastic welding is the repair of broken or damaged taillights, headlights, and other exterior lighting components. These plastic housings and lenses are susceptible to cracks, moisture ingress, and discoloration, which can impair their performance and safety. Plastic welding offers a reliable solution for repairing these components, ensuring a watertight seal, structural stability, and optical clarity. By effectively addressing lighting component damage through plastic welding, car owners can maintain the safety and functionality of their vehicle’s lighting systems.
Interior plastic components, such as dashboard panels, trims, and consoles, also benefit from automotive plastic welding. These parts are often subject to wear and tear, leading to cracks, warping, or detachment. By utilizing plastic welding techniques, car owners and technicians can rejuvenate and reinforce interior components, restoring their original appearance and functionality. This not only enhances the comfort and aesthetics of the vehicle’s interior but also prolongs the lifespan of the plastic components.
Final Thoughts
Automotive plastic welding is instrumental in customizing and modifying vehicles. Enthusiasts and professionals use plastic welding to create custom body panels, aerodynamic modifications, and unique aesthetic enhancements. By seamlessly integrating new plastic elements and refinements with the existing vehicle structure, plastic welding enables the realization of personalized automotive designs and improvements. This aspect of automotive plastic welding showcases its versatility and adaptability in catering to the evolving needs and preferences of car owners and enthusiasts.