Welcome to our comprehensive guide on types of welding. Whether you are a seasoned pro or just getting started, understanding the different methods of welding is essential for successful and efficient projects. In this article, we will explore the various welding techniques used in industries such as construction, automotive, and manufacturing.
From the tried and true method of shielded metal arc welding (SMAW) to the high-tech precision of laser welding, we will delve into the unique characteristics and applications of each technique. We will discuss the advantages and disadvantages of different welding methods, helping you choose the right one for your specific needs.
Our expert team has researched and compiled accurate and up-to-date information on each welding technique, ensuring that you have the knowledge you need to take your welding skills to the next level. Whether you are welding steel, aluminum, or other materials, this guide will provide the insights you need to make informed decisions and achieve outstanding results.
Get ready to expand your welding knowledge and become a true master of your craft. Let’s dive into the fascinating world of welding techniques.
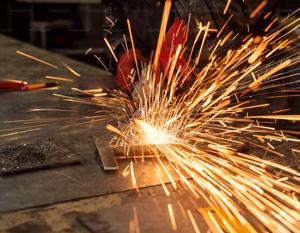
Photo by hollyfab
Different Types of Welding Processes
Shielded Metal Arc Welding (SMAW)
Shielded Metal Arc Welding, also known as SMAW or stick welding, is one of the most popular and widely used welding techniques. It involves using a consumable electrode coated with flux to create an arc between the electrode and the workpiece. The heat generated by the arc melts the electrode, creating a weld pool that cools and solidifies to form a strong bond.
SMAW is versatile and can be used on various materials, including steel, stainless steel, and cast iron. It is commonly used in construction, shipbuilding, and pipeline welding. One of the advantages of SMAW is its portability, as it does not require a shielding gas. It is a slower process compared to other welding methods, and the slag created during the process needs to be removed.
Gas Metal Arc Welding (GMAW)
Gas Metal Arc Welding, also known as GMAW or MIG (Metal Inert Gas) welding, is a semi-automatic process that uses a wire electrode and a shielding gas to create a weld. The wire electrode is continuously fed through a welding gun, and the shielding gas protects the weld from atmospheric contamination.
GMAW is known for its speed and versatility, making it suitable for a wide range of applications, including automotive, manufacturing, and fabrication. It can be used on various materials, including steel, aluminum, and stainless steel. One of the advantages of GMAW is its ability to produce high-quality welds with minimal post-weld cleaning. It requires a clean welding environment and can be affected by wind or drafts.
Flux-Cored Arc Welding (FCAW)
Flux-Cored Arc Welding, also known as FCAW, is a variation of GMAW that uses a tubular wire electrode filled with flux instead of a solid wire electrode. The flux inside the electrode creates a shielding gas and provides additional protection against impurities and contamination. FCAW can be done with or without shielding gas, depending on the type of electrode used.
FCAW is commonly used in construction, shipbuilding, and heavy fabrication. It is suitable for welding thick materials and can be used on steel, stainless steel, and aluminum. One of the advantages of FCAW is its deep penetration and high deposition rates, which make it ideal for welding in challenging positions. It produces more smoke and fumes compared to other welding methods.
Gas Tungsten Arc Welding (GTAW)
Gas Tungsten Arc Welding, also known as GTAW or TIG (Tungsten Inert Gas) welding, is a precise and versatile welding technique that uses a non-consumable tungsten electrode and a separate filler material. The weld area is protected from atmospheric contamination by a shielding gas, usually argon or helium.
GTAW is commonly used in aerospace, automotive, and high-end fabrication industries. It can be used on various materials, including stainless steel, aluminum, and copper alloys. One of the advantages of GTAW is its ability to produce high-quality welds with excellent control over the heat input. It is suitable for welding thin materials and can produce aesthetically pleasing welds. It requires a higher level of skill and is a slower process compared to other welding methods.
Submerged Arc Welding (SAW)
Submerged Arc Welding, also known as SAW, is a welding technique that involves feeding a continuous wire electrode and a granular flux into the weld area. The flux creates a blanket that shields the arc and the molten weld pool from atmospheric contamination.
SAW is commonly used in heavy fabrication and welding of thick materials. It is suitable for welding carbon steel, stainless steel, and low-alloy steels. One of the advantages of SAW is its high deposition rates, making it an efficient process for large-scale projects. It also produces high-quality welds with deep penetration. However, it requires specialized equipment and is not suitable for welding in tight spaces or vertical positions.
Laser Beam Welding (LBW)
Laser Beam Welding, also known as LBW, is a high-tech welding technique that uses a concentrated beam of laser light to create a weld. The laser beam melts the workpiece, and a filler material may or may not be used, depending on the application.
LBW is commonly used in industries such as automotive, aerospace, and electronics. It is suitable for welding thin materials and can produce precise and high-quality welds. One of the advantages of LBW is its ability to weld dissimilar materials and create strong and aesthetically pleasing joints. It requires expensive equipment and is limited to specific applications.
Electron Beam Welding (EBW)
Electron Beam Welding, also known as EBW, is a high-precision welding technique that uses a focused beam of high-velocity electrons to create a weld. The electrons generate heat when they strike the workpiece, melting the material and creating a weld.
EBW is commonly used in industries such as aerospace, medical, and electronics. It is suitable for welding materials with high melting points and can produce deep and narrow welds with minimal distortion. One of the advantages of EBW is its ability to weld materials without the need for filler material, resulting in clean and precise welds. However, it requires specialized equipment and a vacuum environment.
Conclusion
Understanding the different types of welding techniques is crucial for anyone involved in welding projects. Each welding method has its unique characteristics, advantages, and disadvantages, making it suitable for specific applications. From the versatility of shielded metal arc welding (SMAW) to the precision of laser welding, there is a welding technique for every project.
By having a thorough knowledge of these welding methods, you can make informed decisions and choose the right technique for your specific needs. Whether you are welding steel, aluminum, or other materials, knowing the strengths and limitations of each method will help you achieve outstanding results.