Are you a beginner looking to learn the basics of torch cutting? Look no further! In this article, we will guide you through the essential steps and techniques to get you started with torch cutting. Whether you are interested in metalworking, plumbing, or automotive repairs, torch cutting can be a valuable skill to have in your toolbox.
Torch cutting involves the use of a high-temperature flame produced by a torch to cut through various materials, such as metal. With the right knowledge and practice, you can achieve accurate and clean cuts for your projects. We will cover important aspects like selecting the right torch, setting up the equipment safely, and proper cutting techniques.
By understanding the fundamentals of torch cutting, you will gain the confidence to tackle a wide range of projects with ease. So, if you’re ready to take your DIY skills to the next level, join us as we dive into the world of torch cutting basics for beginners. Let’s fire up those torches and start cutting!
What is torch cutting?
Torch cutting is a process that involves the use of a torch to create high-temperature flames for cutting through various materials. This technique is commonly used in metalworking, plumbing, and automotive repairs, where precise and clean cuts are required. The torch produces a flame that can reach temperatures of up to 6,000 degrees Fahrenheit, melting and severing the material being cut.
There are different types of torch cutting methods, each suitable for specific materials and applications. The most common methods include oxy-fuel cutting, plasma arc cutting, and carbon arc cutting. These methods utilize different fuel sources and cutting principles to achieve desired results.
Torch cutting is a versatile technique that can be used to cut through a wide range of materials, including steel, stainless steel, cast iron, copper, and aluminum. It is important to select the appropriate method and equipment based on the material you are working with to ensure optimal cutting performance and safety. Let’s explore the different types of torch cutting methods in more detail.
Torch Cutting Basics: Types of methods
Oxy-fuel cutting
Oxy-fuel cutting is one of the most commonly used torch cutting methods. It involves the use of a fuel gas, such as acetylene, combined with oxygen to create a high-temperature flame for cutting. The fuel and oxygen are supplied through separate hoses and mixed in the torch before ignition.
To perform oxy-fuel cutting, the torch is held at a specific angle and distance from the material being cut. The heat generated by the flame melts the material, while the oxygen stream blows away the molten metal, creating a clean cut. Oxy-fuel cutting is ideal for cutting thicker materials and is widely used in industries like construction, shipbuilding, and manufacturing.
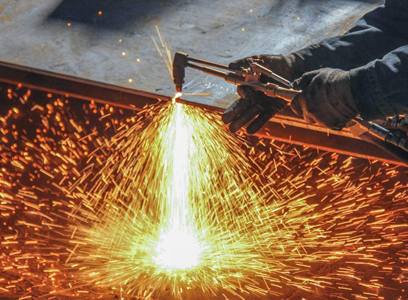
Plasma arc cutting
Plasma arc cutting is another popular method of torch cutting. It utilizes a plasma torch that generates a high-velocity jet of ionized gas, known as plasma, to cut through electrically conductive materials. The plasma is created by passing an electric current through a gas, such as nitrogen or argon, which is forced through a small nozzle.
When the plasma jet comes into contact with the material, it rapidly heats and melts the metal, while a high-velocity gas stream blows away the molten metal, resulting in a precise and clean cut. Plasma arc cutting is known for its ability to cut through a wide range of materials with varying thicknesses, making it suitable for both industrial and artistic applications.
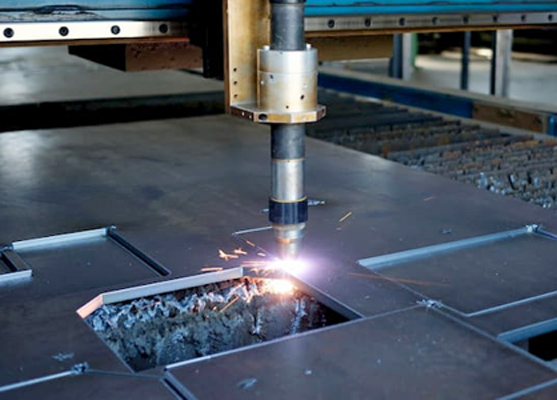
Carbon arc cutting
Carbon arc cutting, also known as air arc cutting, is a torch cutting method that uses the heat generated by a carbon arc to melt and remove the material being cut. It involves the use of a carbon electrode and a high-amperage power source to create an electric arc between the electrode and the material.
As the arc is established, the intense heat causes the material to melt and form a pool of molten metal. The operator then uses compressed air to blow away the molten metal, creating a cut. Carbon arc cutting is commonly used for gouging, beveling, and removing defective welds in metal fabrication and repair work.
Each torch cutting method has its advantages and limitations, and it’s important to consider factors like material thickness, cutting speed, and the desired quality of the cut when choosing the appropriate method for your project. Now that we have covered the types of torch cutting methods, let’s explore the advantages of torch cutting.
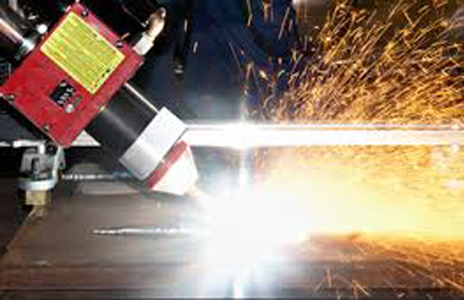
Advantages of Torch Cutting Basics
Torch cutting offers several advantages that make it a popular choice for various applications. Here are some of the key advantages of torch cutting:
Versatility
Torch cutting can be used to cut through a wide range of materials, including metals like steel, stainless steel, and aluminum. This versatility makes it a valuable skill for individuals working in industries like construction, fabrication, and maintenance.
Portability
Torch cutting equipment is relatively compact and portable, allowing for flexibility and ease of use in different work environments. Whether you’re working in a workshop or on a job site, torch cutting equipment can be easily transported and set up.
Cost-effective
Torch cutting is generally more cost-effective compared to other cutting methods, such as laser cutting or waterjet cutting. The equipment and consumables required for torch cutting are relatively affordable, making it an accessible option for DIY enthusiasts and small businesses.
Quick setup
Torch cutting equipment can be set up and ready to use within minutes, allowing for efficient project completion. This quick setup time makes torch cutting a practical choice for time-sensitive tasks or projects with tight deadlines.
Cutting thickness
Torch cutting methods, such as oxy-fuel cutting, are capable of cutting through thick materials. This makes torch cutting an ideal choice for applications that require heavy-duty cutting, such as shipbuilding, structural steel fabrication, and pipeline construction.
While torch cutting offers many advantages, it is crucial to prioritize safety when working with high-temperature flames and potentially hazardous materials. Let’s dive into the equipment and safety precautions necessary for torch cutting.
Torch cutting equipment and safety precautions
Before you begin torch cutting, it is essential to gather the necessary equipment and take appropriate safety precautions to ensure a safe and successful cutting experience. Here are some key equipment and safety measures to consider:
Torch and fuel source
The torch is the primary tool used for torch cutting, and selecting the right torch for your application is crucial. Depending on the cutting method and material thickness, you may need a specific type of torch. For example, oxy-fuel cutting requires a torch that can handle both fuel gas and oxygen, while plasma arc cutting requires a plasma torch.
In addition to the torch, you will also need a fuel source, such as acetylene or propane, depending on the cutting method. It is important to follow the manufacturer’s guidelines and recommendations for selecting and using the appropriate fuel source for your torch.
Personal protective equipment (PPE)
Wearing the appropriate personal protective equipment (PPE) is essential to protect yourself from potential hazards associated with torch cutting. Here are some PPE items you should always wear:
- Safety goggles or face shield: Protect your eyes from sparks, debris, and harmful UV rays generated during torch cutting.
- Flame-resistant clothing: Wear flame-resistant clothing to protect your body from burns and flying sparks. Avoid wearing loose-fitting clothing that could catch fire.
- Welding gloves: Use heavy-duty welding gloves to protect your hands from heat, sparks, and molten metal.
- Respiratory protection: Depending on the cutting method and materials being cut, you may need to wear a respiratory mask or respirator to protect yourself from fumes and airborne particles.
- Hearing protection: If you’re working in a noisy environment, wear earplugs or earmuffs to protect your hearing.
Ventilation
Proper ventilation is crucial when torch cutting to ensure the safe dispersal of fumes and gases generated during the cutting process. If you’re working indoors or in an enclosed space, make sure there is adequate ventilation to remove harmful fumes and maintain a safe working environment. If necessary, use exhaust fans or open windows and doors to improve airflow.
Fire safety
Torch cutting involves working with high-temperature flames, so it’s important to have fire safety measures in place. Here are some precautions to consider:
- Clear the work area of flammable materials, such as paper, rags, and solvents, to minimize the risk of fire.
- Have a fire extinguisher readily available and ensure it is in good working condition.
- Keep a fire-resistant blanket or welding curtain nearby to smother any potential fires.
- Never leave the torch unattended while it is lit, and always turn off the torch and fuel source when not in use.
By following these equipment recommendations and safety precautions, you can significantly reduce the risk of accidents and ensure a safe torch cutting experience. Now that we have covered the equipment and safety measures, let’s dive into the various cutting techniques for different materials.
Torch cutting techniques for various materials
The technique used for torch cutting may vary depending on the material being cut. Different materials have different melting points and properties, which require specific cutting approaches for optimal results. Here are some torch cutting techniques for various commonly used materials:
Cutting steel
Steel is one of the most commonly cut materials using torch cutting methods. To cut steel effectively, follow these steps:
- Prepare the steel: Clean the surface of the steel to remove any dirt, rust, or paint that could interfere with the cutting process.
- Set up the torch: Adjust the flame settings on your torch according to the thickness of the steel. Consult the manufacturer’s guidelines for recommended settings.
- Choose the right cutting tip: Select a cutting tip that is appropriate for the thickness of the steel. The size of the cutting tip determines the size of the cut and affects cutting speed.
- Start the cut: Position the torch at a 45-degree angle to the steel surface, with the tip slightly above the surface. Ignite the torch and move it smoothly along the desired cutting path.
- Maintain a steady cutting speed: Move the torch steadily along the cutting path, maintaining a consistent distance between the torch tip and the steel surface. This will ensure a clean and accurate cut.
- Complete the cut: Once the cut is complete, turn off the torch and allow the steel to cool before handling.
Cutting stainless steel
Stainless steel is a corrosion-resistant material that requires specific techniques for torch cutting. Here’s how to cut stainless steel effectively:
- Prepare the stainless steel: Clean the surface of the stainless steel to remove any contaminants that could affect the cut quality.
- Adjust the torch settings: Set the flame temperature and cutting speed according to the thickness of the stainless steel. Stainless steel requires a higher heat input compared to regular steel.
- Select the appropriate cutting tip: Use a cutting tip specifically designed for stainless steel to achieve optimal results.
- Start the cut: Position the torch at a 45-degree angle to the stainless steel surface, with the tip slightly above the surface. Ignite the torch and begin the cut, maintaining a steady cutting speed.
- Control the heat input: Stainless steel is prone to warping and distortion when exposed to excessive heat. Control the heat input by moving the torch quickly and avoiding prolonged exposure to the same spot.
- Cool the cut: Once the cut is complete, allow the stainless steel to cool before handling. Rapid cooling with water or air can lead to stress and cracking in the material.
Cutting aluminum
Aluminum is a lightweight and highly conductive material that requires specific techniques for torch cutting. Here’s how to cut aluminum effectively:
- Clean the aluminum: Remove any dirt or contaminants from the surface of the aluminum before cutting.
- Set up the torch: Adjust the flame settings on your torch to suit the thickness of the aluminum. Aluminum requires a higher heat input compared to steel.
- Choose the right cutting tip: Select a cutting tip suitable for aluminum cutting. The size of the cutting tip affects cutting speed and the width of the cut.
- Start the cut: Position the torch at a 45-degree angle to the aluminum surface, with the tip slightly above the surface. Ignite the torch and move it smoothly along the desired cutting path.
- Control the heat input: Aluminum conducts heat quickly, so it’s important to control the heat input to prevent warping or melting. Move the torch quickly and avoid prolonged exposure to the same spot.
- Cool the cut: Once the cut is complete, allow the aluminum to cool before handling. Rapid cooling can lead to stress and cracking in the material.
By following these techniques, you can achieve clean and accurate cuts on different materials using torch cutting methods. However, there are some common mistakes that beginners should be aware of and avoid. Let’s explore these common mistakes and how to overcome them.
Common mistakes to avoid in torch cutting
Torch cutting, like any skill, requires practice and attention to detail. Here are some common mistakes beginners should avoid to ensure successful torch cutting:
Incorrect torch setup
Using the wrong torch settings, such as incorrect flame temperature or cutting speed, can result in poor cut quality and inefficient cutting. Always refer to the manufacturer’s guidelines and recommendations for setting up your torch based on the material and thickness you’re working with.
Inconsistent cutting speed
Maintaining a consistent cutting speed is crucial to achieve clean and accurate cuts. Moving the torch too fast can result in a shallow cut, while moving too slowly can cause excessive heat buildup and melting. Practice maintaining a steady cutting speed to achieve optimal results.
Improper torch angle
The torch angle plays a significant role in the quality of the cut. Holding the torch at the wrong angle can cause the cut to be uneven or not penetrate the material properly. Experiment with different torch angles to find the optimal angle for the material you’re cutting.
Failure to clean and prepare the material
Cutting dirty or contaminated materials can lead to poor cut quality and damage to the torch tip. Always clean and prepare the material before cutting to ensure optimal results. Remove any dirt, rust, or paint that could interfere with the cutting process.
Ignoring safety precautions
Safety should always be a top priority when torch cutting. Ignoring safety precautions, such as not wearing the appropriate PPE or not following proper ventilation practices, can result in serious accidents or health hazards. Always prioritize safety and follow the recommended safety measures.
By being aware of these common mistakes and taking the necessary steps to overcome them, you can improve your torch cutting skills and achieve better results. Additionally, here are some tips to help
Conclusion
Torch cutting is a valuable skill for beginners to learn, as it offers versatility, portability, cost-effectiveness, quick setup, and the ability to cut through a wide range of materials. By understanding the basics of torch cutting, beginners can confidently tackle various projects in industries like metalworking, plumbing, and automotive repairs. It is important to choose the appropriate torch cutting method based on the material being worked with, such as oxy-fuel cutting for thicker materials, plasma arc cutting for electrically conductive materials, and carbon arc cutting for gouging and beveling.
Overall, torch cutting provides a practical and efficient solution for achieving accurate and clean cuts in a variety of applications.